Advanced instruments inc. 5 operation, Principle of operation – Analytical Industries GPR-3100 Series Oxygen Purity Analyzer User Manual
Page 8
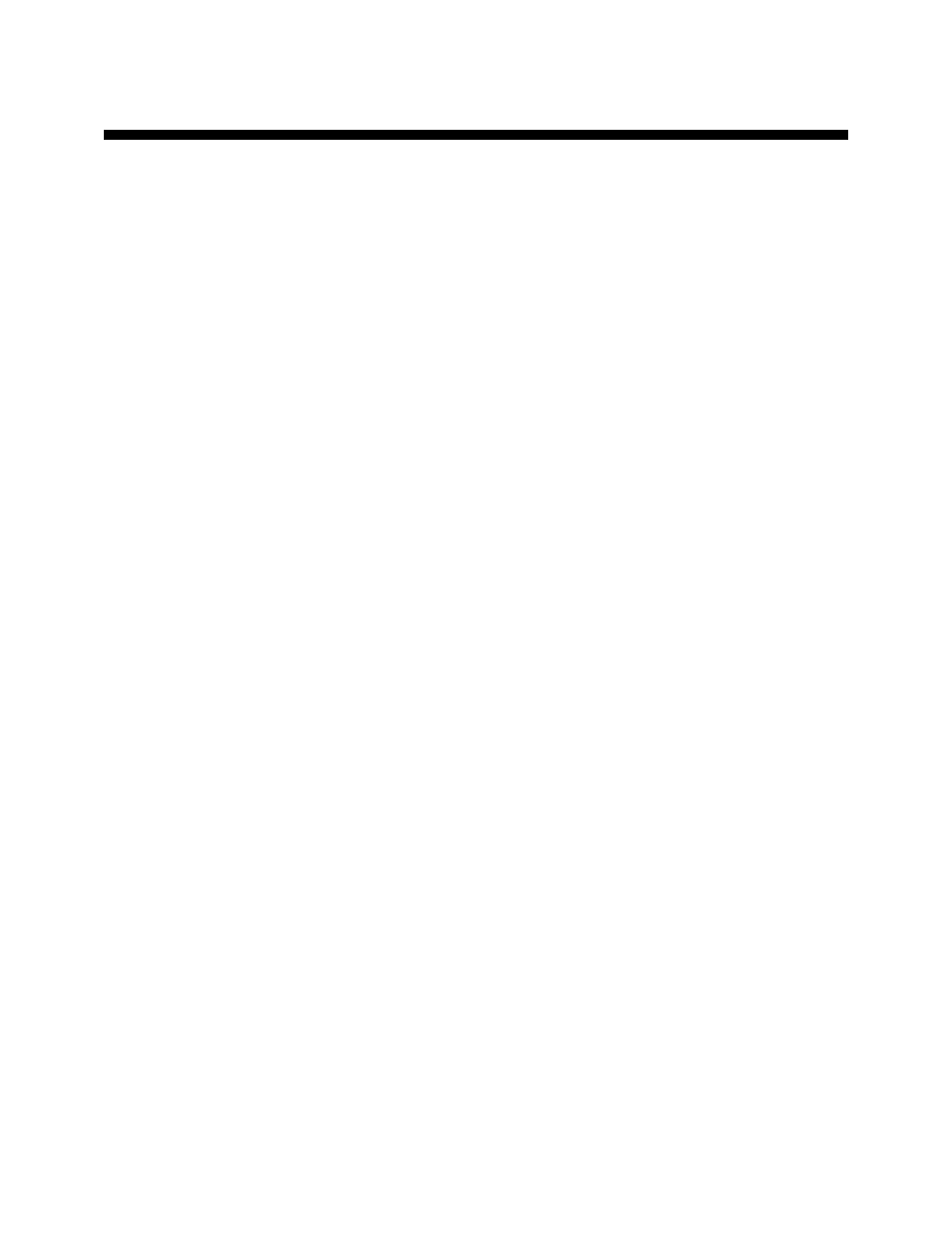
Advanced Instruments Inc.
5 Operation
GPR-3100 Rev 2/05 1
Principle of Operation
The GPR-3100 oxygen analyzer incorporates an advanced galvanic fuel cell type sensor capable of
measuring 100% oxygen on a suppressed range of 90-100% on a continuous basis It is the only
electrochemical sensor based analyzer capable of this measurement.
Background
The production of pure oxygen has been confined to the production of medical grade oxygen (99.0%,
typically specified at 99.5% or greater purity). However, the demand for oxygen is expanding rapidly due
largely to recent developments in chemical processes requiring elevated concentrations of oxygen (85-
95%) that boost yields and reduce emissions without significant cost increases and to a lesser extent the
growth of transfilling oxygen (92%) cylinders for home care use. The oxygen supplied can be be
generated cryogenically or by pressure (PSA) or vacuum (VSA) swing adsorption methods.
Historically producers and users have relied on analyzers based on paramagnetic method for measuring
oxygen purity. These sensor offer highly accurate results especially at the suppressed ranges of 90-100%
oxygen. However, they are very sensitive to changes in the flow rate of sample gas, the presence of
minute particulates and moisture, temperature variations and vibration. Consequently, paramagnetic
analyzers are expensive and require frequent almost daily calibration.
Analyzers based on galvanic sensor concept have always generated an interest for oxygen purity
measurements because they are specific to oxygen, versatile, low maintenance and inexpensive.
However, short sensor life (3-4 months at best) and the gradual drop (drift) in the signal output of the
micro-fuel cell with time has precluded their use.
Major Advancement in Galvanic Fuel Cell Sensor Technology
In competing with paramagnetic devices the focus was primarily on advancing the galvanic sensor
technology but also included temperature controlling the sample gas and automatically compensating the
signal output of the sensor for barometric pressure variations to assure a stable ‘drift free’ oxygen
measurement.
An advanced galvanic sensor has been developed that provides two years of sensor life and is capable of
operating properly on a continuous basis in 100% oxygen concentrations. This proprietary design
addresses the challenges of:
Providing a sufficient amount of anode material to support the reduction of oxygen over several years.
Maintaining at all times a sufficient concentration of hydroxyl ions to support the reduction of oxygen at
and near the sensing cathode.
Preventing the build-up of PbO at and near the sensing cathode (that eventually starts precipitating and
covers the sensing cathode) that can cause the signal output of the sensor to drop (drift) with time.
Through proprietary means the production rate of the reaction product is controlled without sacrificing
either the fast less than 13 second response time or any of the features (described above) of the micro-
fuel cell analyzer. The resulting on-line and portable analyzers are approximately half the cost of their
paramagnetic counterparts.
The performance of the sensor was validated over 14 months of testing and exhibited excellent stability
in 100% oxygen. The sample flow rate was set at 0.1 lpm (and insensitive to changes of up to 1.0 lpm)
with the sample vented to the atmosphere via ¼” diameter tube to minimize the backpressure.