6 field repair actions, 7 typical functional problems, 8 inverter fault codes – R&M Materials Handling ELECTRIC CHAIN HOISTS LoadMate Chain Hoist LM 10 Stepless User Manual
Page 75
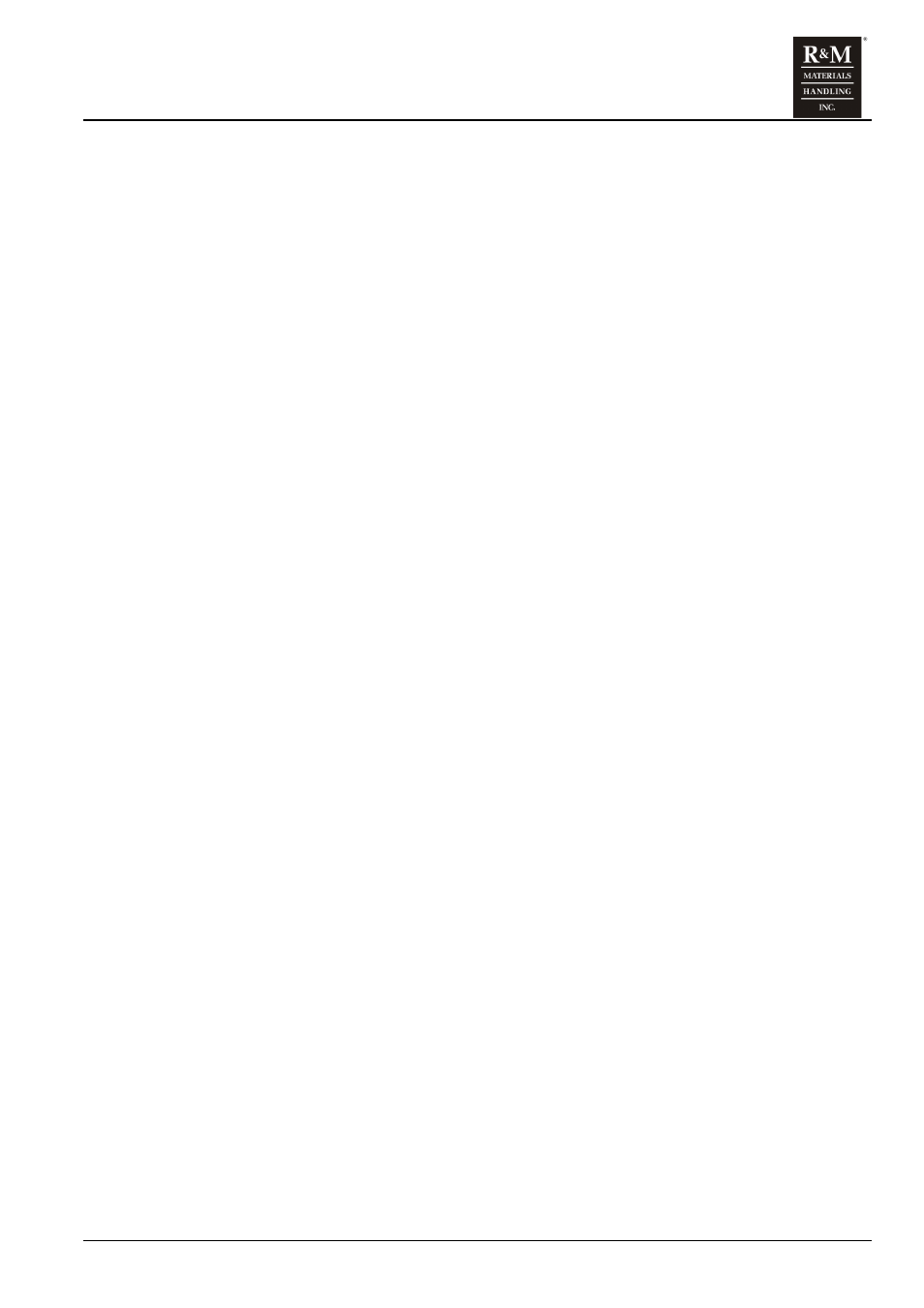
LM10 STEPLESS I&M MANUAL/EN/11.30.2010
75/99
This document and the information contained herein, is the exclusive property of R&M Materials Handling, Inc., and represents a non-public, confidential and proprietary trade secret that
may not be reproduced, disclosed to third parties, altered or otherwise employed in any manner whatsoever without the express written consent of R&M Materials Handling, Inc.
Copyright © (2010) R&M Materials Handling, Inc. All rights reserved.
8.6 Field repair actions
The purpose of troubleshooting and field repair actions is primarily to determine whether the drive or external
devices in fact cause the problems. After that, the next step is to detect the possibly damaged components
inside the drive. If any damage inside the drive is caused by the environment (motor failure, brake failure,
power supply problems etc.) it is very important to repair/change faulty items to prevent reoccurring
problems.
The best way to repair a faulty inverter is to replace it with a new one. If the fault can be located, it is also
possible to replace some of the components. When replacing an inverter or a Control unit with a new one,
the parameter list of the existing drive is needed so that the parameter settings can be copied to new the
one.
8.7 Typical functional problems
•
Inverter does not start when mains are connected.
Check mains voltage between terminal L1, L2 and L3
•
Indicator “Ready” is on and indicator “Fault” is off, but motor does not run.
Check control mode selection
Check voltage at run command terminals
Check state of digital inputs from parameter V2.3
•
Indicator “Ready” is on and indicator “Run” is on, but motor does not run.
Check motor cable connection
•
Motor runs poorly
Check that load is not over nominal
Check that all cables are connected correctly and the junctions are reliable
Check that all motor dependant parameters are correct
Check the voltage of the slowdown limit switch input
Check state of digital inputs from parameter V2.3
Check that motor’s brake opens completely
Check that minimum speed parameters do not have too small values
For traveling application: check u/f-curve tuning and/or Autotuning. If the main girder
is new, it might be necessary to drive trolley several times with no load from end to
end, before beginning of u/f-curve tuning and/or Auto tuning.
•
Some parameters are not accessible or changing is not possible
Check that password has value
2156
Check that parameter value is inside the limits
Parameter value can not be changed in RUN state
Parameter value change must be confirmed with “Enter” button
8.8 Inverter fault codes
If any of the following failures are found, the inverter displays the fault code and closes the mechanical brake
causing the movement to stop. If several faults occur one after another, the latest one is displayed, the
others are stored to fault history page.
When inverter fault supervision trips, the FAULT indicator turns on and the blinking fault code “Fx xx“ (x=
fault accounting number, xx = fault code number) appears on the display.
The drive includes an automatic fault reset operation; the fault code stays on the display until the fault is
removed and the controller released back to 0-position. Some of the fault codes require to switch the power
off before run is possible, for example F1 (overcurrent).