R&M Materials Handling ELECTRIC CHAIN HOISTS LoadMate Chain Hoist LM 10 Stepless User Manual
Page 76
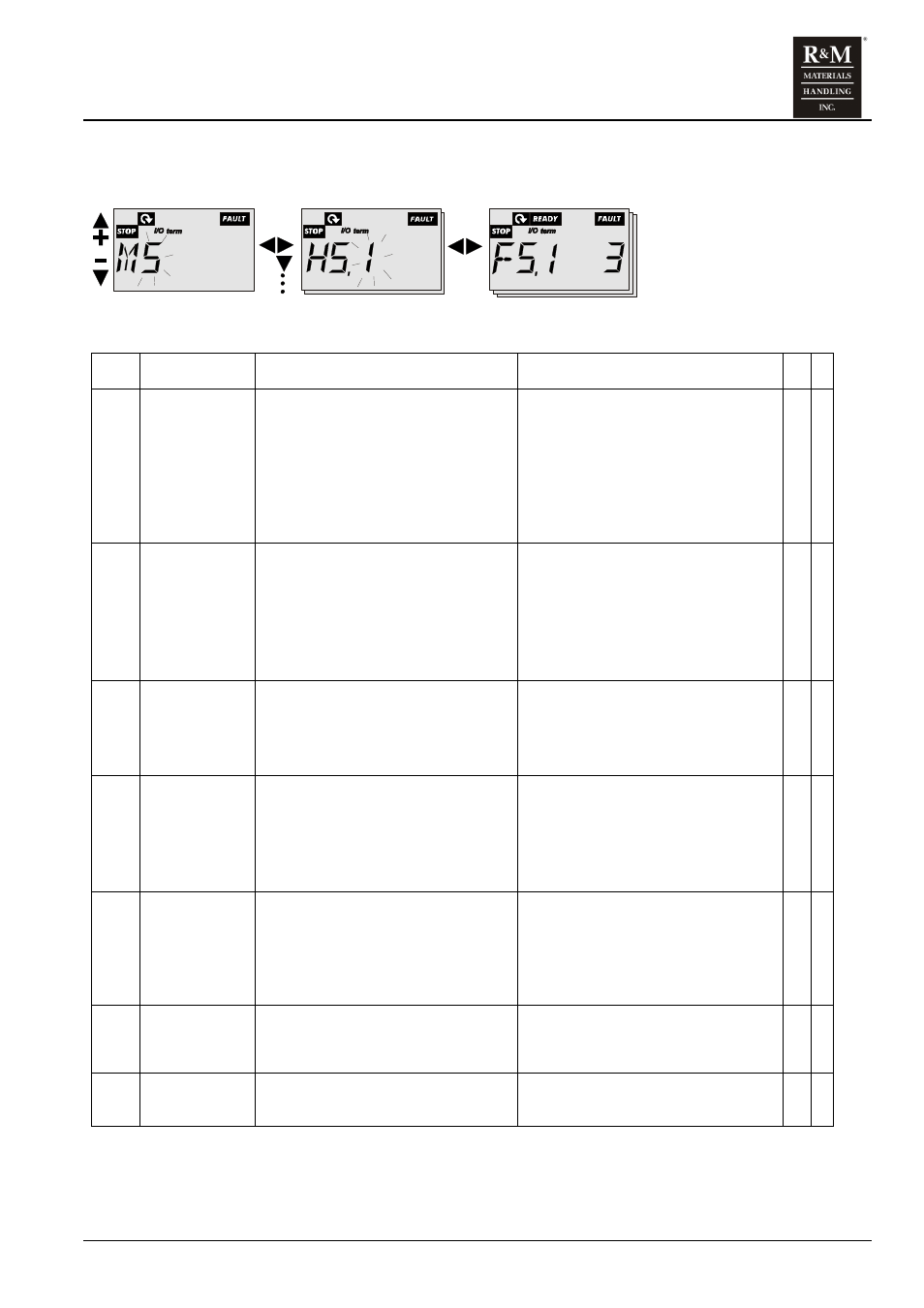
LM10 STEPLESS I&M MANUAL/EN/11.30.2010
76/99
This document and the information contained herein, is the exclusive property of R&M Materials Handling, Inc., and represents a non-public, confidential and proprietary trade secret that
may not be reproduced, disclosed to third parties, altered or otherwise employed in any manner whatsoever without the express written consent of R&M Materials Handling, Inc.
Copyright © (2010) R&M Materials Handling, Inc. All rights reserved.
All faults are stored in the Fault History menu except F51 Stop-Limit, from there they can be seen if
necessary. The fault history stores the last 5 fault codes.
Table 23. Inverter Fault Codes
Fault
code
Fault
Possible cause
Checking
A
B
F 1
Overcurrent
Inverter has measured too high current
(over 4*I
N
peak or over 2.8* I
N
rms) in the
motor output:
sudden heavy load increase
short circuit in the motor or cable
not suitable motor
wrong motor parameters
Reset: switch power off and restart after the
lamps of display are off.
Check:
brake operation
motor type and power rating
parameters
motor cable connection
motor insulation
motor loading
X
F 2
Overvoltage
DC-bus voltage has exceeded 135%
maximum level, 911Vdc
deceleration time is too short
supply voltage raised >1.35 x Un (high
overvoltage spikes at mains or not
sinusoidal wave form)
Reset has an additional 5s time delay.
Check:
adjust the deceleration time P1.1.3 longer
measure main supply voltage level and wave
form while not driving
braking resistor cable
braking resistor type and resistance
braking chopper operation
X
F 3
Earth fault
Current measurement has sensed
unbalance in motor phase currents.
Supervision level is 5% of inverter nominal
current
not symmetric load
insulation failure in the motor or the cable
Reset has an additional 5s time delay.
Check:
motor insulation
motor cable insulation (phase-ground,
phase-phase)
X
F 6
External Stop
ES signal inactive
Check:
ES external connections
Control mode selection P1.1.11
State of input DID5, V2.3.
Thermal protection of motor is normally
connected to ES signal, check motor
temperature.
X
F 9
Undervoltage
DC-bus voltage has dropped below 333Vdc
mains supply voltage interrupted
inverter fault can also cause an
undervoltage trip
external fault during run may cause an
undervoltage trip
In case of temporary supply voltage break,
reset the fault and start again. Check mains
input.
If mains supply is correct, an internal failure
has occurred.
Contact authorized service center.
X
F 11
Output phase
supervision
Current supervision has sensed that at least
one of the motor phases has no current
Check:
motor cable connections
measure motor phase currents and compare
to display value
X
F 13
Inverter under-
temperature
Temperature of heat sink is below
acceptable operating level -10°C (14°F)
Check
ambient temperature
cubicle heating
X