Max1636, Design procedure – Rainbow Electronics MAX1636 User Manual
Page 18
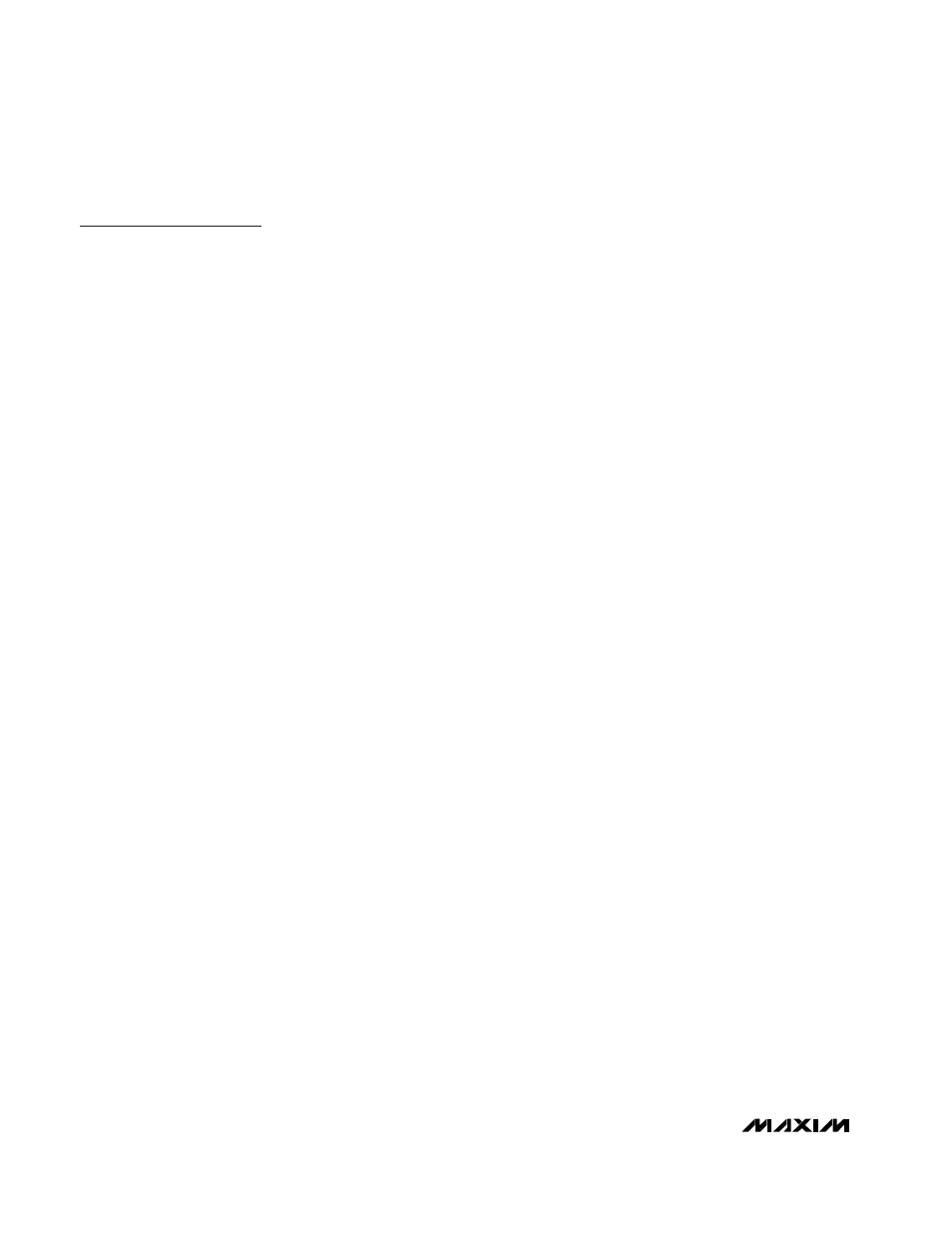
MAX1636
Design Procedure
The five predesigned standard application circuits
(Figure 1 and Table 1) contain ready-to-use solutions
for common application needs. Use the following
design procedure to optimize these basic schematics
for different voltage or current requirements. But before
beginning a design, firmly establish the following:
• Maximum input (battery) voltage, V
IN(MAX)
. This
value should include the worst-case conditions, such
as no-load operation when a battery charger or AC
adapter is connected but no battery is installed.
V
IN(MAX)
must not exceed 30V.
• Minimum input (battery) voltage, V
IN(MIN)
. This should
be taken at full load under the lowest battery condi-
tions. If V
IN(MIN)
is less than 4.5V, use an external cir-
cuit to externally hold VL above the VL undervoltage
lockout threshold. If the minimum input-output differ-
ence is less than 1.5V, the filter capacitance required
to maintain good AC load regulation increases (see
Low-Voltage Operation section).
Inductor Value
The exact inductor value is not critical and can be
freely adjusted to make trade-offs between size, cost,
and efficiency. Lower inductor values minimize size
and cost but reduce efficiency due to higher peak-cur-
rent levels. The smallest inductor is achieved by lower-
ing the inductance until the circuit operates at the
border between continuous and discontinuous mode.
Further reducing the inductor value below this
crossover point results in discontinuous-conduction
operation even at full load. This helps lower output filter
capacitance requirements, but efficiency suffers due to
high I
2
R losses. On the other hand, higher inductor val-
ues mean greater efficiency, but resistive losses due to
extra wire turns eventually exceed the benefit gained
from lower peak-current levels. Also, high inductor val-
ues can affect load-transient response (see the V
SAG
equation in the Low-Voltage Operation section). The
equations in this section are for continuous-conduction
operation.
Three key inductor parameters must be specified:
inductance value (L), peak current (I
PEAK
), and DC
resistance (R
DC
). The following equation includes a
constant, LIR, which is the ratio of inductor peak-to-
peak AC current to DC load current. A higher LIR value
allows smaller inductance but results in higher losses
and higher ripple. A good compromise between size
and losses is a 30% ripple-current to load-current ratio
(LIR = 0.3), which corresponds to a peak inductor cur-
rent 1.15 times higher than the DC load current.
L = V
OUT
(V
IN(MAX)
- V
OUT
) / (V
IN(MIN)
x f x I
OUT
x LIR)
where f = switching frequency, normally 200kHz or
300kHz, and I
OUT
= maximum DC load current. The
peak current can be calculated by:
I
PEAK
= I
LOAD
+ [V
OUT
(V
IN(MAX)
- V
OUT
) / (2 x f x L x V
IN(MAX)
)]
The inductor's DC resistance should be low enough
that R
DC
x I
PEAK
< 100mV, as it is a key parameter for
efficiency performance. If a standard, off-the-shelf
inductor is not available, choose a core with an LI
2
rat-
ing greater than L x I
PEAK2
and wind it with the largest
diameter wire that fits the winding area. For 300kHz
applications, ferrite-core material is strongly preferred;
for 200kHz applications, Kool-Mu
®
(aluminum alloy) or
even powdered iron is acceptable. If light-load efficien-
cy is unimportant (in desktop PC applications, for
example), then low-permeability iron-powder cores may
be acceptable, even at 300kHz. For high-current appli-
cations, shielded-core geometries, such as toroidal or
pot core, help keep noise, EMI, and switching-wave-
form jitter low.
Current-Sense Resistor Value
The current-sense resistor value is calculated accord-
ing to the worst-case, low-current-limit threshold volt-
age (from the Electrical Characteristics table) and the
peak inductor current:
R
SENSE
= 80mV / I
PEAK
Use I
PEAK
from the second equation in the Inductor
Value section. Use the calculated value of R
SENSE
to
size the MOSFET switches and specify inductor satura-
tion-current ratings according to the worst-case high-
current-limit threshold voltage:
I
PEAK
= 120mV / R
SENSE
Low-inductance resistors, such as surface-mount metal
film, are recommended.
Input Capacitor Value
Connect low-ESR bulk capacitors directly to the drain
on the high-side MOSFET. The bulk input filter capaci-
tor is usually selected according to input ripple current
requirements and voltage rating, rather than capacitor
value. Electrolytic capacitors with low enough equiva-
lent series resistance (ESR) to meet the ripple-current
requirement invariably have sufficient capacitance val-
ues. Aluminum electrolytic capacitors, such as Sanyo
OS-CON or Nichicon PL, are superior to tantalum
types, which risk power-up surge-current failure, espe-
cially when connecting to robust AC adapters or low-
impedance batteries. RMS input ripple current (I
RMS
) is
Low-Voltage, Precision Step-Down
Controller for Portable CPU Power
18
______________________________________________________________________________________
Kool-Mu is a registered trademark of Magnetics, Inc.