Design procedure – Rainbow Electronics MAX17101 User Manual
Page 24
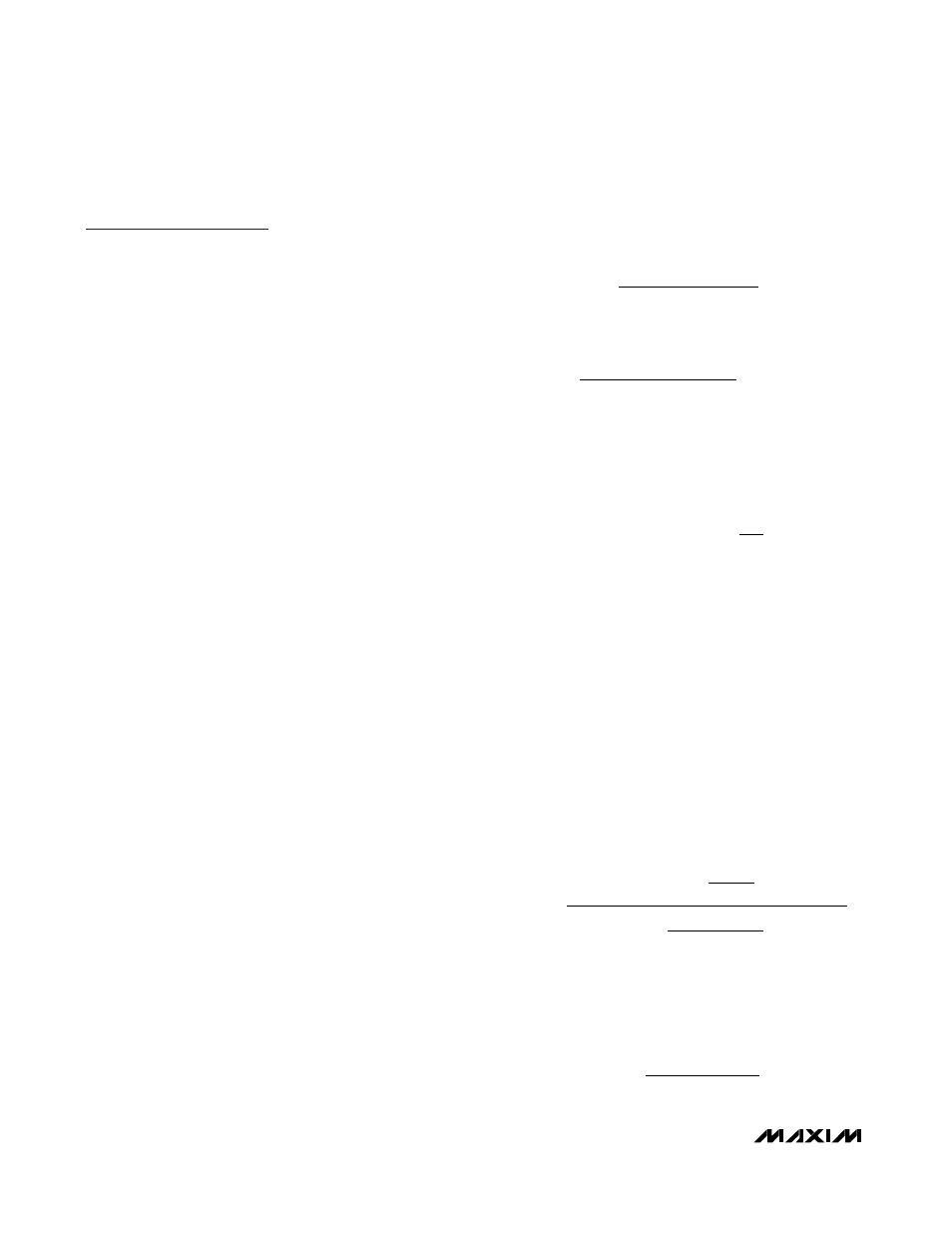
MAX17101
Dual Quick-PWM, Step-Down Controller
with Low-Power LDO, RTC Regulator
24
______________________________________________________________________________________
Design Procedure
Firmly establish the input-voltage range and maximum
load current before choosing a switching frequency and
inductor operating point (ripple-current ratio). The primary
design trade-off lies in choosing a good switching fre-
quency and inductor operating point, and the following
four factors dictate the rest of the design:
•
Input Voltage Range: The maximum value
(V
IN(MAX)
) must accommodate the worst-case, high
AC-adapter voltage. The minimum value (V
IN(MIN)
)
must account for the lowest battery voltage after
drops due to connectors, fuses, and battery-selector
switches. If there is a choice at all, lower input volt-
ages result in better efficiency.
•
Maximum Load Current: There are two values to
consider. The peak load current (I
LOAD(MAX)
)
determines the instantaneous component stresses
and filtering requirements and thus drives output
capacitor selection, inductor saturation rating, and
the design of the current-limit circuit. The conti-
nuous load current (I
LOAD
) determines the thermal
stresses and thus drives the selection of input
capacitors, MOSFETs, and other critical heat-
contributing components.
•
Switching Frequency: This choice determines the
basic trade-off between size and efficiency. The opti-
mal frequency is largely a function of maximum input
voltage due to MOSFET switching losses that are
proportional to frequency and V
IN
2
. The optimum fre-
quency is also a moving target due to rapid improve-
ments in MOSFET technology that are making higher
frequencies more practical.
•
Inductor Operating Point: This choice provides
trade-offs between size vs. efficiency and transient
response vs. output ripple. Low inductor values
provide better transient response and smaller phy-
sical size, but also result in lower efficiency and
higher output ripple due to increased ripple cur-
rents. The minimum practical inductor value is one
that causes the circuit to operate at the edge of cri-
tical conduction (where the inductor current just
touches zero with every cycle at maximum load).
Inductor values lower than this grant no further size-
reduction benefit. The optimum operating point is
usually found between 20% and 50% ripple current.
When pulse skipping (SKIP low and light loads), the
inductor value also determines the load-current
value at which PFM/PWM switchover occurs.
Inductor Selection
The switching frequency and inductor operating point
determine the inductor value as follows:
For example: I
LOAD(MAX)
= 4A, V
IN
= 12V, V
OUT2
=
2.5V, f
SW
= 355kHz, 30% ripple current or LIR = 0.3:
Find a low-loss inductor having the lowest possible DC
resistance that fits in the allotted dimensions. Ferrite
cores are often the best choice, although powdered
iron is inexpensive and can work well at 200kHz. The
core must be large enough not to saturate at the peak
inductor current (I
PEAK
):
Most inductor manufacturers provide inductors in stan-
dard values, such as 1.0μH, 1.5μH, 2.2μH, 3.3μH, etc.
Also look for nonstandard values, which can provide a
better compromise in LIR across the input voltage
range. If using a swinging inductor (where the no-load
inductance decreases linearly with increasing current),
evaluate the LIR with properly scaled inductance values.
Transient Response
The inductor ripple current also impacts transient-
response performance, especially at low V
IN
- V
OUT
dif-
ferentials. Low inductor values allow the inductor
current to slew faster, replenishing charge removed
from the output filter capacitors by a sudden load step.
The amount of output sag is also a function of the maxi-
mum duty factor, which can be calculated from the on-
time and minimum off-time:
where t
OFF(MIN)
is the minimum off-time (see the
Electrical Characteristics
) and K is from Table 3.
The amount of overshoot during a full-load to no-load tran-
sient due to stored inductor energy can be calculated as:
V
I
L
C
V
SOAR
LOAD MAX
OUT OUT
≈
(
)
Δ
(
)
2
2
V
L
I
V
K
V
t
SAG
LOAD MAX
OUT
IN
OFF MIN
=
(
)
⎛
⎝⎜
⎞
⎠⎟
+
Δ
(
)
(
2
))
(
⎡
⎣
⎢
⎤
⎦
⎥
−
(
)
⎛
⎝⎜
⎞
⎠⎟
−
2C
V
V
V
K
V
t
OUT OUT
IN
OUT
IN
OFF M
MIN)
⎡
⎣
⎢
⎢
I
I
LIR
PEAK
LOAD MAX
=
+
⎛
⎝⎜
⎞
⎠⎟
(
)
1
2
L
V
V
V
V
kHz
A
μH
=
Ч
−
Ч
Ч
Ч
=
2 5
12
2 5
12
355
4
0 3
4 65
.
(
.
)
.
.
L
V
V
V
V f
I
LIR
RIPPLE
IN
OUT
IN SW LOAD MAX
=
−
(
)
(
)