Applications information – Rainbow Electronics MAX6660 User Manual
Page 19
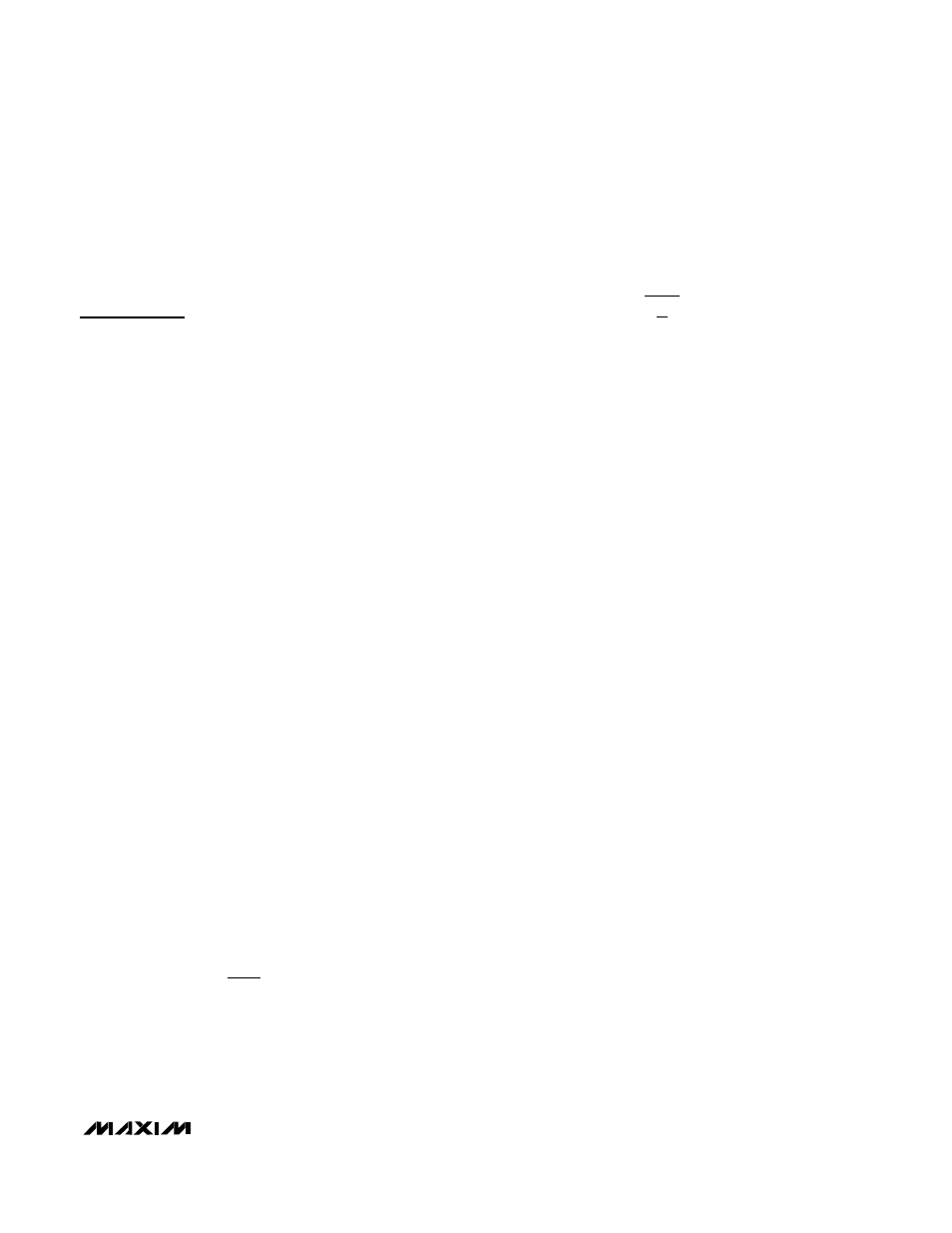
MAX6660
Remote-Junction Temperature-Controlled
Fan-Speed Regulator with SMBus Interface
______________________________________________________________________________________
19
speeds except at very low speeds where a fan failure is
indicated by an overflow of the fan speed counter
rather than f
L
. The overflow flag cannot be viewed sep-
arately in the Status Byte but is ORed with bit 0, the fan
fail bit.
Applications Information
Mode Register
Resistance in series with the remote-sensing junction
causes conversion errors on the order of 0.5°C per ohm.
The MAX6660 Mode register gives the ability to elimi-
nate the effects of external series resistance of up to
several hundred ohms on the remote temperature mea-
surement and to adjust the temperature measuring
ADC to suit different types of remote-diode sensor. For
systems using external switches or long cables to con-
nect to the remote sensor, a parasitic resistance can-
cellation mode can be entered by setting Mode register
bit 7 = 1. This mode requires a longer conversion time
and so can only be used for fan conversion rates of
1Hz or slower. Bits 6, 1, and 0 are Reserved. Use bits
5–2 to adjust the ADC gain to achieve accurate temper-
ature measurements with diodes not included in the
recommended list or to individually calibrate the
MAX6660 for use in specific control systems. These
bits adjust gain to set the temperature reading at
+25°C, using two’s complement format reading. Bit 5 is
the sign (1 = increase, 0 = decrease), bit 4 = 2°C shift,
bit 3 = 1°C shift, bit 2 = 1/2°C shift.
General Programming Techniques
The full-scale range of the fan regulation loop is
designed to accommodate fans operating between the
1000rpm to 8000rpm range of different fans. An on-
chip 8415Hz oscillator is used to generate the 33Hz to
66Hz reference frequency. Choose the prescalar such
that the fan full-speed frequency divided by the
prescalar falls in the 33Hz to 66Hz range. The full-scale
reference frequency is further divided by the value in
the FSC register to the desired fan frequency [read:
speed].
1) Determine the fan’s maximum tachometer frequency:
Where poles = number of tachometer poles (pulses
per revolution). Most fans are two poles; therefore,
two pulses per revolution.
2) Set the programmable FCD to a value P so that the
above frequency falls in the 33Hz to 66Hz range.
3) Determine the value required for the Fan FS register:
Example: Fan A has a 2500rpm rating:
2500rpm / 60s gives an output of 41.7Hz
41.7Hz x 2 pulses = 83.4Hz
The 83.4Hz value is out of the 33Hz to 66Hz decre-
ment/increment range.
4) Set bits in the FC register to divide the signal down
within the 33Hz to 66Hz range. Bits 1, 0 = 10
(divide by 2: P = 2):
83.4 / 2 = 41.7Hz
5) Set the FS register to yield approximately 42Hz:
42 = 8415 / FS (value)
FS (value) = 200
FS register = 11001000
6) In current-sense feedback, a current pulse is gener-
ated whenever there is a step increase in fan cur-
rent. The frequency of pulses is then not only
determined by the fan rpms and the number of
poles, but also by the update rate at which the fan
driver forces an increase in voltage across the fan.
The maximum current pulse frequency is then given
by:
f
C
= f
✕
P / (P-1)
Where f = {RPM/60}
✕
poles and P is the value in FCD.
The value required for the fan FS register is:
FS = 8415 / {f / (P-1)}
The fan speed limit in FCTL should be set to:
f
L
= 8415 / (N
✕
f
C
)
A value of P = 1 cannot be used in current-sense mode.
Fan Selection
For closed-loop operation and fan monitoring, the
MAX6660 requires fans with tachometer outputs. A
tachometer output is typically specified as an option on
many fan models from a variety of manufacturers. Verify
FS
f
P
=
8415
f
RPM
x poles
=
60