OMAX 60120 JetMachining Center User Manual
Features benefits
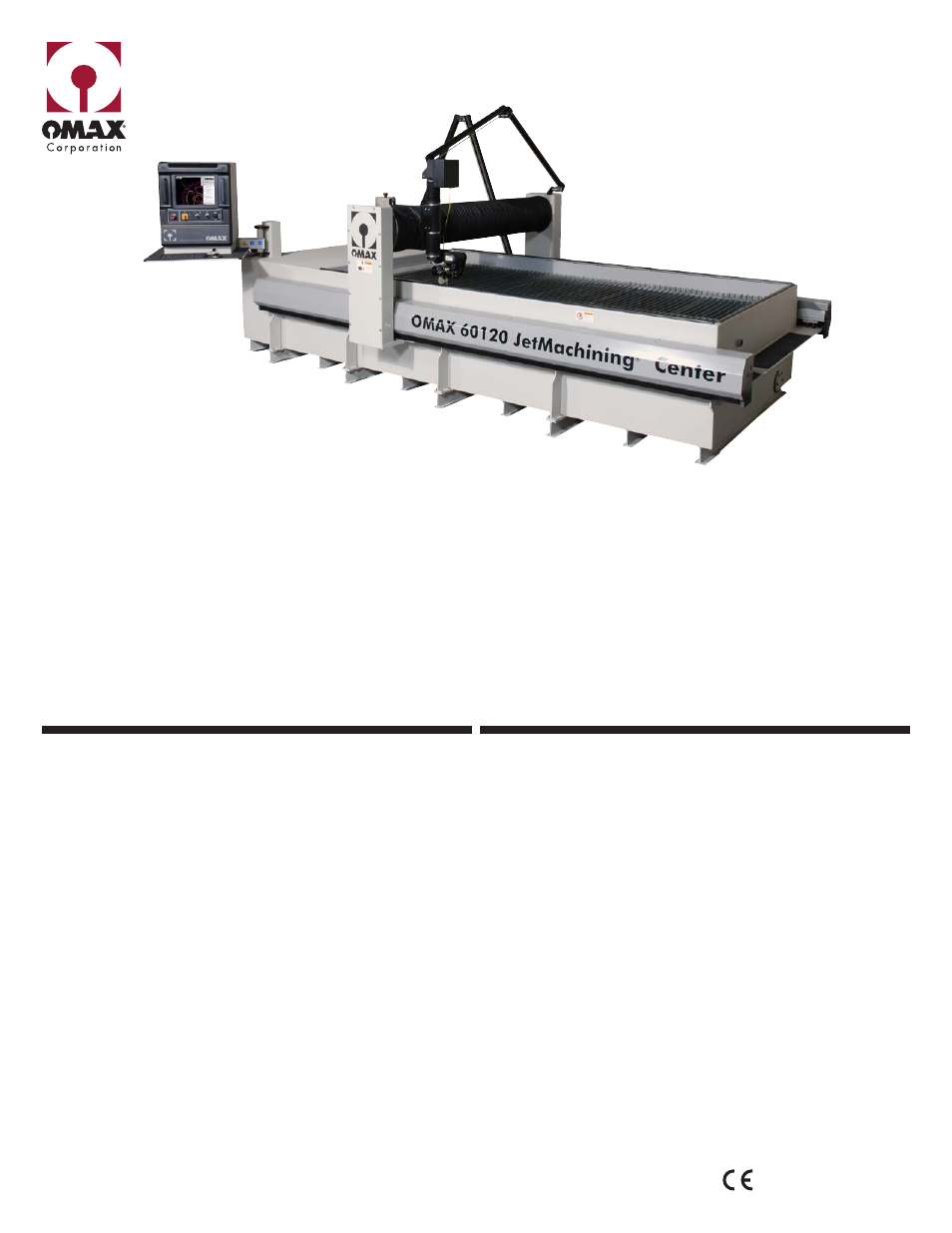
OMAX 60120 JetMachining Center
The small-footprint bridge-style OMAX 60120 JetMachining Center is fast and accurate, ideal for a wide range of machining
needs, with one of the lowest cost per part in the industry. The large table can cut stock up to 5’ x 10’, creating complex parts out
of almost any material. Challenging hard, reflective, and nonconductive materials can also be cut, making the 60120 a valuable
addition to existing shop capabilities. Accessories such as the Tilt-A-Jet
®
for taper-free edges, A-Jet
®
for 3D cutting, and the Rotary
Axis for 6-Axis machining increase versatility. The easy-to-use Intelli-MAX Software and the 60120 take you quickly from idea to
reality.
FEATURES
BENEFITS
•
Fastest cutting speeds and best precision compared to any abrasivejet in
the industry and is backed by our exclusive Intelli-MAX
®
Software with real
world cutting data
•
Programmable Motorized Z-Axis with a precision OMAX MAXJET
®
5i Nozzle
Assembly can boost cutting productivity and process efficiency
•
Tilt-A-Jet taper compensating abrasivejet cutting head
(available as an option)
•
Patent-pending Intelli-TRAX
®
traction drive inside the X-Axis beams fully
enclosed inside coated steel covers
•
Scissor-style hard plumbing for low maintenance and high reliability
•
Drive system sealed against water, dirt, and grit
•
Highly efficient, industry-proven Generation 4 EnduroMAX
®
Pumps available
up to 100 hp with operating efficiencies up to 90%
•
Rapid Water Level Control for quiet and clean submerged cutting
•
Bulk Abrasive Feed Assembly transports garnet from the assembly’s large
hopper into the Zero Downtime Hopper located at the Motorized Z-Axis
•
Optional Variable Speed Solids Removal System (VS-SRS) designed for
tough industrial use increases uptime through automated solids removal
•
Shipped as a completely pre-assembled and factory-tested system
•
Machines a wide range of materials and thicknesses, from metals to glass
•
Does not create heat-affected zones or mechanical stresses
•
No tool changes and minimal fixturing reduces setup by 50% or more
•
No additional water required for pump cooling
•
Small, efficient footprint for minimal floorspace utilization
•
Leaves behind a satin-smooth edge, reducing secondary operations
•
No noxious gases, liquid and oils used in, or caused by, the machining process
•
EnduroMAX pump technology delivers the highest nozzle horsepower in the
industry for faster and more efficient cutting
•
Completes most work below 80 dBA at one meter for submerged cutting
•
Environmentally “green” system with quiet and clean operation with low
electrical consumption
•
Highly robust and reliable pump design capable of over 1000 hours
between maintenance
PRECISION ABRASIVE WATERJET SYSTEMS
60120
Made in the USA
WWW.OMAX.COM