OMAX 2626 JetMachining Center User Manual
Omax 2626 jetmachining center, Features benefits
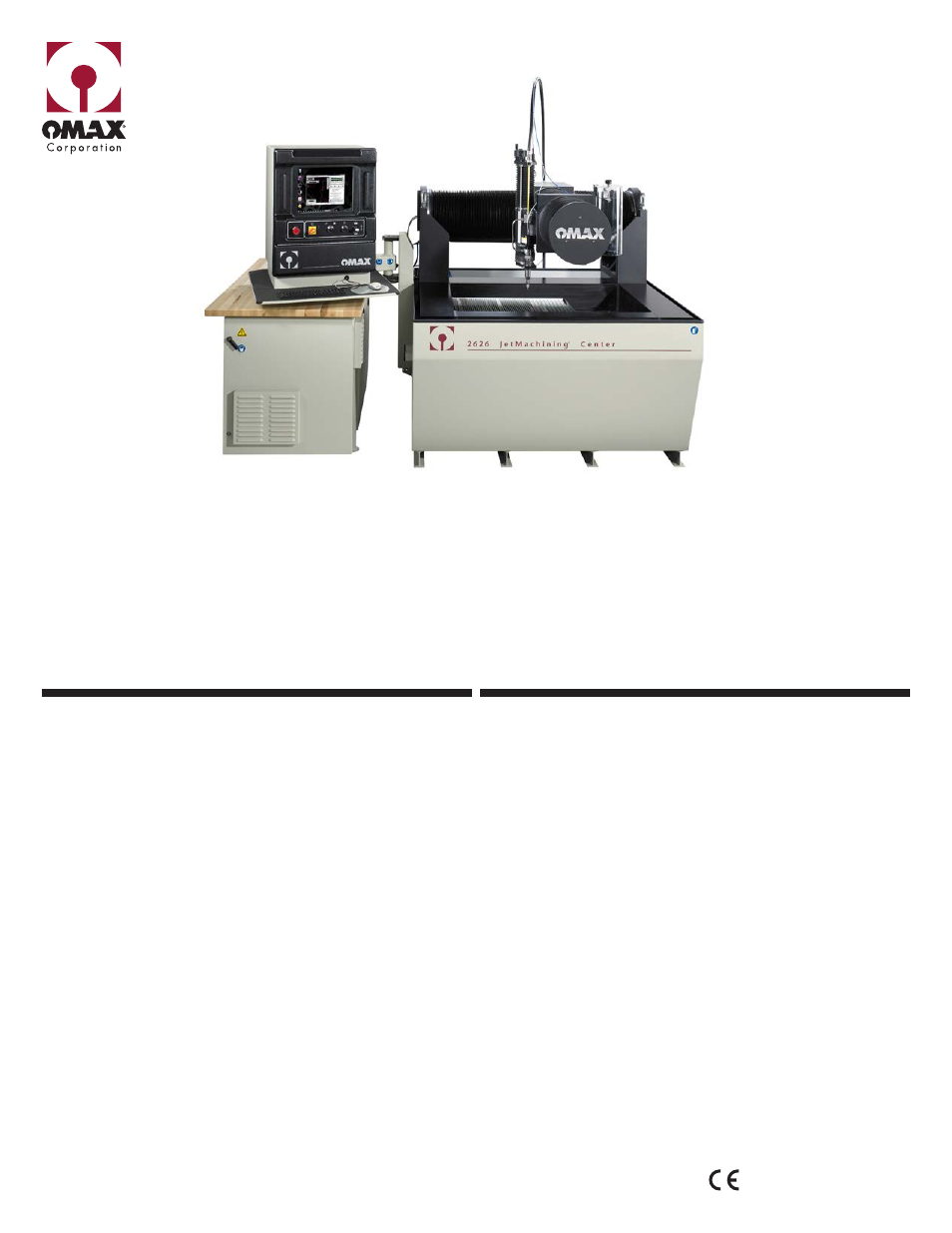
PRECISION ABRASIVE WATERJET SYSTEMS
2626
Made in the USA
WWW.OMAX.COM
OMAX 2626 JetMachining Center
The compact size and high accuracy of the 2626 JetMachining
®
Center makes it ideal for high precision waterjet machining, from
research and development to small part prototyping and production. The 2626 utilizes the fast, efficient, and powerful Intelli-MAX
Software Suite to achieve superior performance while cutting complex parts out of most materials. With the optional Tilt-A-Jet
®
and
7/15 Mini MAXJET nozzle, the 2626 is capable of precision miniature machining.
FEATURES
BENEFITS
•
Fastest cutting speeds and best precision compared to any abrasivejet in
the industry and is backed by our exclusive Intelli-MAX
®
Software with real
world cutting data
•
Programmable Motorized Z-Axis with a precision OMAX MAXJET
®
5i Nozzle
Assembly can boost cutting productivity and process efficiency
•
Tilt-A-Jet taper compensating abrasivejet cutting head
(available as an option)
•
Precision X-Y Axis rigidly mounted to the cutting table
•
Pre-loaded linear bearings and precision ball screws
•
Low maintenance, high reliability scissor-style hard plumbing as an option
•
Drive system sealed against water, dirt, and grit
•
High efficiency Generation 4 EnduroMAX
®
pump systems available in 30,
40, or 50 hp with operating efficiencies up to 90%
•
Robust and accurate design for tight tolerance cutting and reliable operation
•
Rapid Water Level Control for quiet and clean submerged cutting
•
Optional Variable Speed Solids Removal System (VS-SRS) designed for
tough industrial use increases uptime through automated solids removal
•
Easy operator access to the work area
•
Shipped as a completely pre-assembled and factory-tested system
•
Machines a wide range of materials and thicknesses, from metals to glass
•
Does not create heat-affected zones or mechanical stresses
•
No tool changes and minimal fixturing reduces setup by 50% or more
•
No additional water required for pump cooling
•
Small, efficient footprint for minimal floorspace utilization
•
Leaves behind a satin-smooth edge, reducing secondary operations
•
No noxious gases, liquid and oils used in, or caused by, the machining process
•
EnduroMAX pump technology delivers the highest nozzle horsepower in the
industry for faster and more efficient cutting
•
Completes most work below 80 dBA
•
Environmentally “green” system with quiet and clean operation with low
electrical consumption
•
Highly robust and reliable pump design capable of over 1000 hours
between maintenance