Hydronic piping, Temperature rise applications – Lochinvar 1 User Manual
Page 31
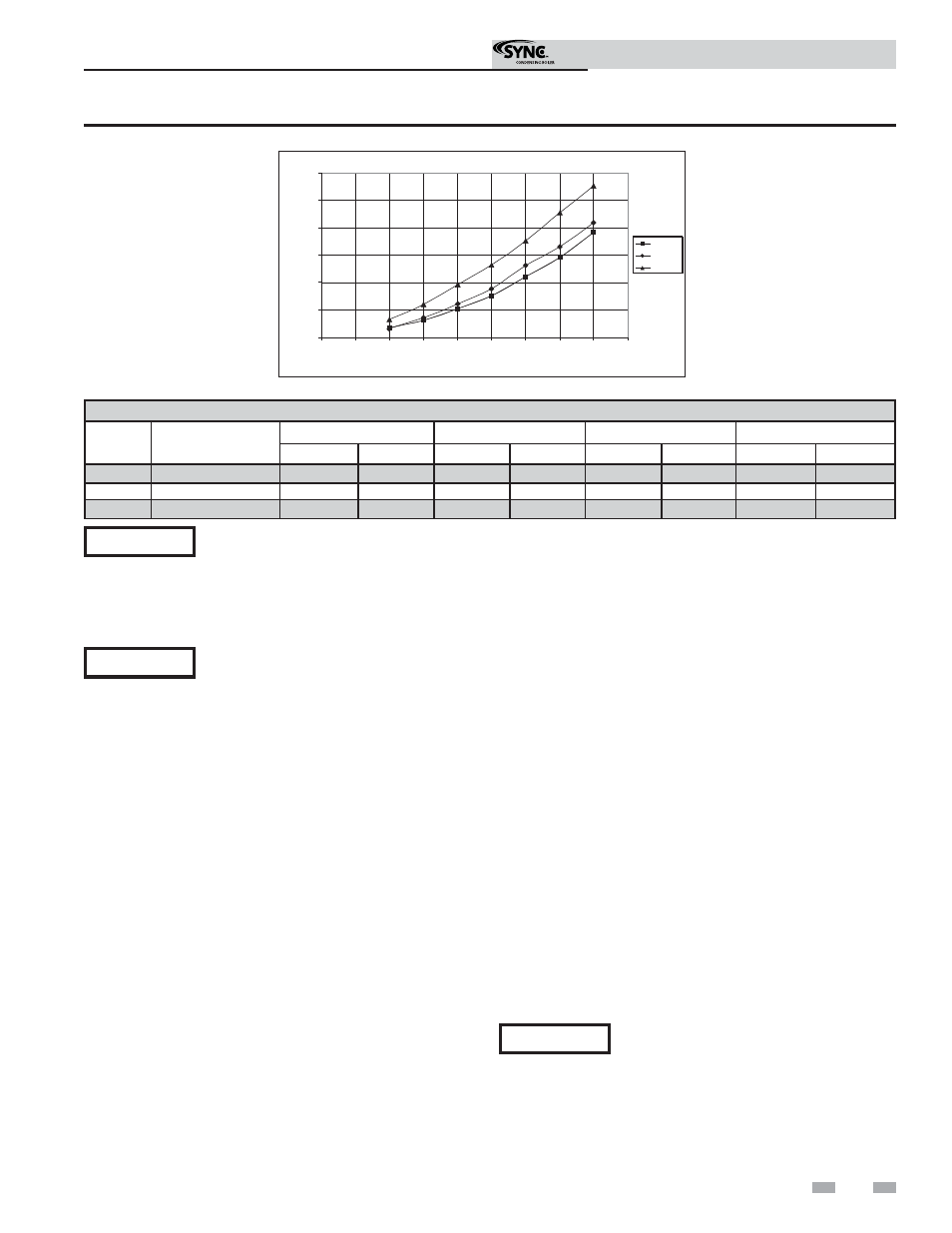
Installation & Operation Manual
It is required that near boiler piping systems
utilize Primary/Secondary configurations as
shown in FIG.’s 5-5 and 5-6 only. The use of
other near boiler piping configurations could
result in improper building and system flow
rates leading to inadvertent boiler high limit
shutdowns and poor system performance.
Near boiler piping components
1. Boiler
piping:
Boiler system piping MUST be sized per the pipe
requirements listed in Table 5A. Reducing the pipe size
can restrict the flow rate through the boiler, causing
inadvertent high limit shutdowns and poor system
performance.
2. Boiler circulating pump:
Field supplied. The boiler circulating pump MUST be
sized to meet the specified minimum flow requirements
listed in FIG. 5-4.
3. Hot Water Generator circulating pump:
Field supplied. The pump MUST be sized to meet
the specified minimum flow requirements listed in
FIG. 5-4. Consult the indirect boiler operating
guide to determine flow characteristics for the selected
product
used.
4. Boiler
isolation
valves:
Field supplied. Full port ball valves are required. Failure
to use full port ball valves could result in a restricted flow
rate through the boiler.
5. Check
valves:
Field supplied. Check valves are required for
installation as shown in FIG.’s 5-5 and 5-6. Failure to
install check valves could result in a reverse flow condition
during pump(s) off cycle.
6. Domestic indirect hot water isolation valves:
Field supplied. Full port ball valves are
required. Failure to use full port ball valves could
result in a restricted flow rate through the boiler.
7. Anti-scald mixing valve:
Field supplied. An anti-scald mixing valve is
recommended when storing domestic hot water above
115°F
(46°C).
8. Unions:
Field supplied. Recommended for unit serviceability.
9. Pressure
relief
valve:
Factory supplied. The pressure relief valve is sized to
ASME
specifications.
10. System temperature sensor:
Lochinvar supplies a system temperature sensor.
The sensor is to be installed in the heating loop
downstream from the boiler hot water piping and
heating loop junction. The sensor should be
located far enough downstream to sense system diluted
water
temperature.
NOTICE
Pump sizing and flow requirements are
based on 20 feet (6 m) of black iron piping, 4
- 90° elbows, and 2 - fully ported ball valves.
*When using copper with a 20° temperature
rise increase piping to 3".
NOTICE
5
Hydronic piping
(continued)
NOTICE
A system supply sensor (factory supplied)
MUST BE installed for proper boiler
operation.
TEMPERATURE RISE APPLICATIONS
Model
MINIMUM PIPE
SIZE
20°F 25°F
30°F
35°F
GPM
FT/HD
GPM
FT/HD
GPM
FT/HD
GPM
FT/HD
1000
2½"
55
31
40
20
38
18
32
13
1300
2½"
65*
30
52
20
45
16
37
11
1500
2½"
74*
33
60
23
51
18
42
12
0
10
20
30
40
50
60
0
10
20
30
40
50
60
70
80
90
SB1500
SB1300
SB1000
Pressure Drop vs Flow
Flow Rate (GPM) - Single Heat Exchanger Only
P
ressur
e Dr
op (F
eet of Head)
Single Hea
t Ex
changer Only
Figure 5-4 Pressure Drop vs. Flow
Table 5A Sizing Information for Temperature Rise Applications_20°F, 25°F, 30°F and 35°F
11. Y-Strainer:
Field supplied. A Y-strainer or equivalent multipurpose
strainer is recommended at the inlet of the heat exchanger
to remove system particles from older hydronic systems and
protect newer systems.
31