Lincoln Electric Welder User Manual
Page 26
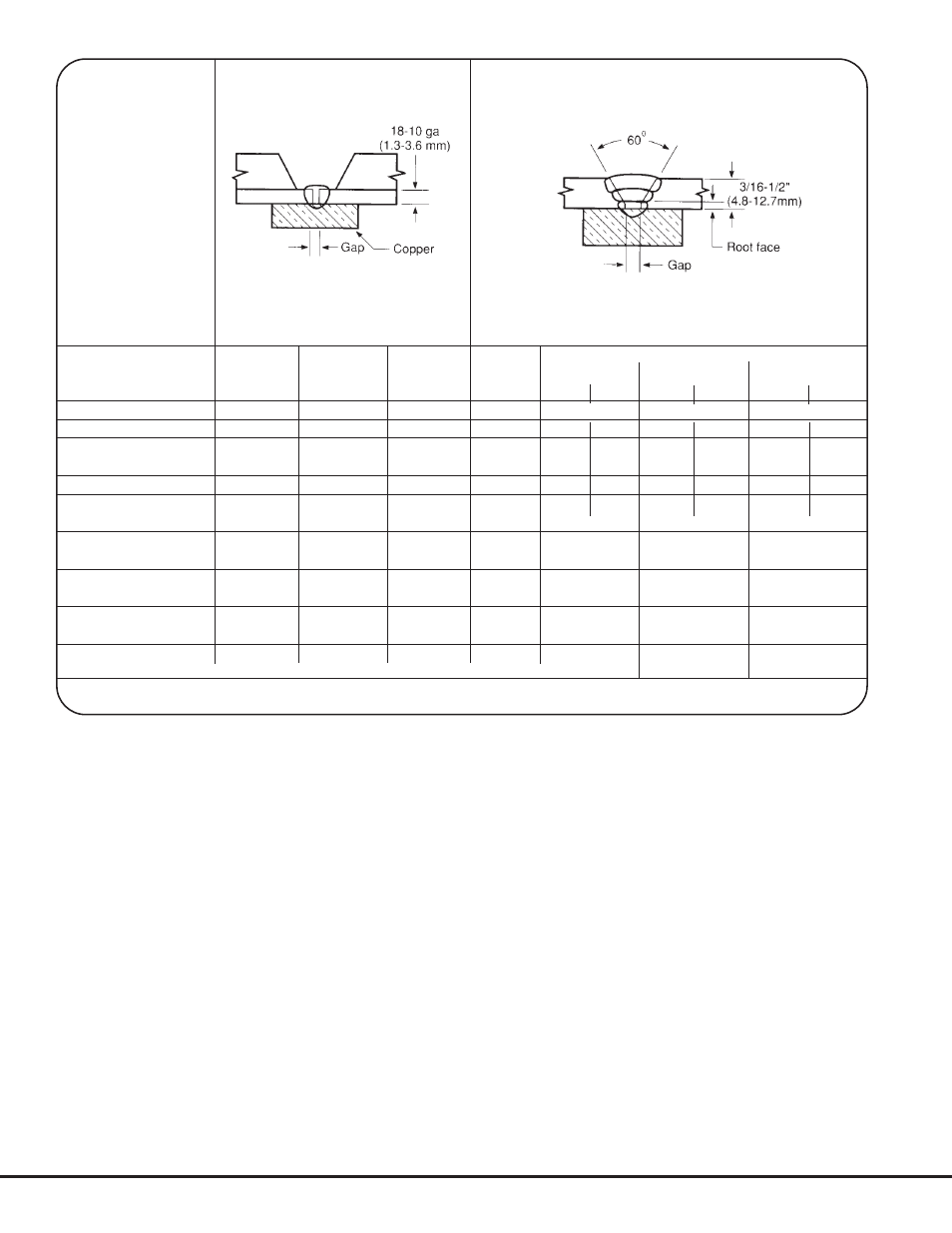
24
multipass welds.
Submerged arc welding creates a
large volume of molten metal that
remains fluid for appreciable time. It
is essential that this molten metal be
supported and contained until it has
solidified. The two most common
means of weld backing are
nonfusible backing and fusible
backing.
Copper backing is the most
frequently used nonfusible backing in
the welding of stainless steel. When
copper is used as a chill bar, care
must be taken to prevent copper
grain boundary penetration. Recom -
mended groove dimensions are
shown in Figure 13. Ceramic
backing tapes are also sometimes
used.
With a fusible metallic backing, the
weld penetrates into and fuses with
the stainless backing, which either
temporarily or permanently becomes
an integral part of the assembly.
Most submerged arc welding is done
in the flat position. This results in the
best bead contour and ease of
operation. Occasionally, welding is
done on circumferential seams.
Figure 14 illustrates the effect of
various inclinations.
Submerged arc fluxes are available
as proprietary materials for welding
stainless steel. Composition of
materials fall into two categories –
fused type and bonded type. The
fused type is glasslike and is
produced by melting the ingredients
at high temperatures followed by
crushing to granulate the flux. The
bonded or agglomerated type is
produced by mixing the ingredients
with a suitable binder and baking
the mixture. Lincoln manufactures
only bonded fluxes.
Alloying elements can be added to
the weld deposit through some
bonded fluxes. These include
chromium, nickel, molybdenum and
niobium (columbium). If alloying
Welding Position: Flat
Weld Quality Level: Code
Steel Weldability: Good
Plate Thickness in.
0.050 (18 ga)
0.078 (14 ga)
0.140 (10 ga)
3/16
1/4
3/8
1/2
Plate Thickness
mm.
1.3
2.0
3.6
4.8
6.4
9.5
12.7
Pass
1
1
1
1
1
2
1
2-3
1
2-5
Electrode Class
E3XX-16
E3XX-16
E3XX-16
E3XX-16
E3XX-16
E3XX-16
E3XX-16
Electrode
Size in.
5/64
3/32
1/8
5/32
5/32
3/16
5/32
3/16
5/32
3/16
Electrode Size
mm.
2.0
2.4
3.2
4.0
4.0
4.8
4.0
4.8
4.0
4.8
Current (amp) DC (+)
40*
60
85
125
125
160
125
160
125
160
Arc Speed (in./min.)
14 -16
11.5 - 12.5
8.5 - 9.5
6.7 - 7.3
5.7-6.3 7.6-8.4
5.7-6.3
5.7-6.3
5.7-6.3
5.7-6.3
Arc Speed
mm/sec
5.9 - 6.8
4.9 - 5.3
3.6 -4.0
2.8 - 3.1
2.4-2.7 3.2-3.6
2.4-2.7
2.4-2.7
2.4-2.7
2.4-2.7
Electrode Req’d (lb./ft.)
0.020
0.038
0.080
0.150
0.340
0.650
1.06
Electrode Req’d
kg/m
0.030
0.057
0.119
0.223
0.506
0.968
1.579
Total Time (hr./ft. of weld)
0.0133
0.0167
0.0222
0.0286
0.0583
0.100
0.167
Total Time
hrs./m of weld
0.0436
0.0548
0.0728
0.0938
0.1913
0.3281
0.5479
Gap (in.)
0
1/32
1/32
1/16
3/32
3/32
3/32
Gap
mm
0
0.8
0.8
1.6
2.4
2.4
2.4
Root Face (in.)
0
0
0
1/16
1/16
1/16
1/16
Root Face
mm
0
0
0
1.6
1.6
1.6
1.6
*Use DC (–)
Note: AC can be used with 10% increase in current. E3XX-15 electrode can be used with a 10% decrease in current.
FIGURE 6 — Suggested procedures for SMAW of butt joints in austenitic stainless steel from 18 (1.3 mm) gauge
to 1/2 inch (12.7 mm) thickness in the flat position.