Southbend SOUTH BEND LATHE CO.. SB1024 User Manual
Page 63
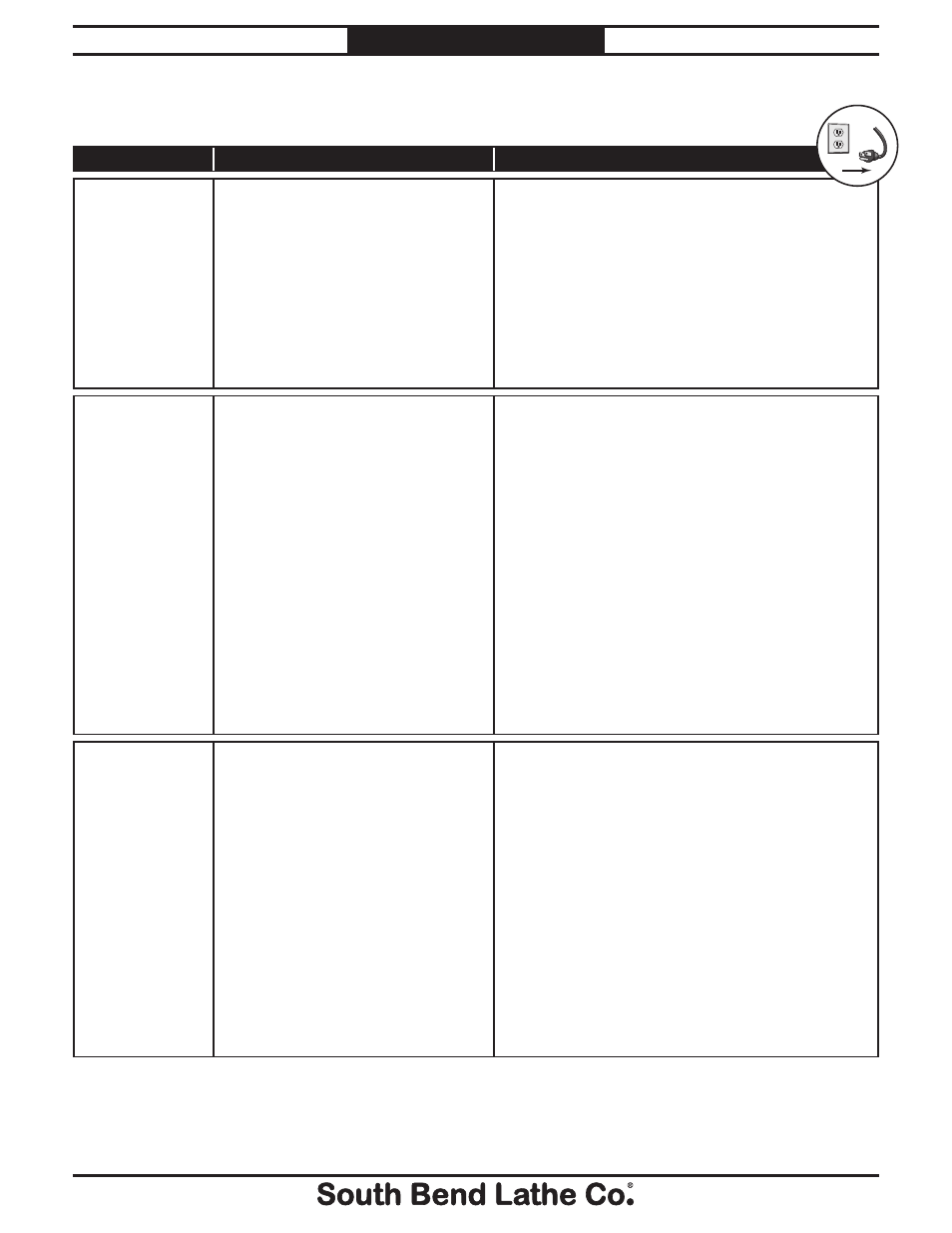
For Machines Mfg. Since 8/09
SB1024/SB1025/SB1026
-61-
TR O U B L E S H O OTI N G
If you need replacement parts, or if you are unsure how to do any of the solutions given here, feel free
to call us at (360) 734-1540.
Symptom
Possible Cause
Possible Solution
Machine does not
start or a breaker
trips.
1.
Emergency stop button is pushed in
or is at fault.
1.
Rotate the button clockwise until it pops out;
replace if necessary.
2.
Plug/receptacle is at fault or wired
incorrectly.
2.
Test for good contacts; correct the wiring.
3.
Power supply is switch OFF or is
at fault.
3.
Ensure hot lines have correct voltage on all legs and
main power supply is switched ON.
4.
Motor connection wired incorrectly.
4.
Correct motor wiring connections (Pages 66 & 69).
5.
ON button or spindle direction
switch at fault.
5.
Replace faulty ON button or spindle direction
switch.
6.
Motor windings or motor is at fault.
6.
Replace motor.
Machine stalls or is
overloaded.
1.
Machine is undersized for the task.
1.
Use smaller sharp tooling; reduce the feed rate;
reduce the spindle speed; use coolant.
2.
Workpiece alignment is poor.
2.
Eliminate workpiece binding; use vise or clamps as
required for proper workpiece alignment control.
3.
Dull or incorrect cutting tool.
3.
Use sharp and correct cutting tool for the operation.
4.
Spindle speed is incorrect for the
operation.
4.
Select appropriate spindle speed (Page 37).
5.
Motor connection wired incorrectly.
5.
Correct motor wiring connections (Pages 66 & 69).
6.
Plug/receptacle is at fault or wired
incorrectly; incorrect voltage
coming from power source.
6.
Test for good contact; correct wiring problems;
ensure hot lines have correct voltage on all legs.
7.
Pulley(s) slipping on shaft.
7.
Replace loose pulley/shaft.
8.
Motor bearings at fault.
8.
Test by rotating shaft; rotation grinding/loose shaft
requires bearing replacement.
9.
Motor has overheated.
9.
Clean off motor, let cool, and reduce workload.
10.
Motor is at fault.
10.
Replace motor.
Machine has
vibration or noisy
operation.
1.
Tool holder or cutter is at fault.
1.
Replace out-of-round tool holder; replace/re-sharpen
cutter; use appropriate feed rate spindle speed.
2.
Workpiece alignment is poor.
2.
Eliminate workpiece binding; use vise or clamps as
required for proper workpiece alignment control.
3.
Motor or component is loose.
3.
Inspect replace stripped or damaged bolts/nuts and
re-tighten with thread locking fluid.
4.
Pulley is loose.
4.
Re-align/replace shaft, pulley, set screw, and key as
required.
5.
Machine is incorrectly mounted to
floor or sits uneven.
5.
Re-tighten/replace mounting bolts in floor; relocate/
shim machine.
6.
Motor fan is rubbing on fan cover.
6.
Replace dented fan cover or fan.
7.
Pulley(s) slipping on shaft.
7.
Replace loose pulley/shaft.
8.
Motor bearings at fault.
8.
Test by rotating shaft; rotation grinding/loose shaft
requires bearing replacement.
9.
Gearbox is at fault.
9.
Rebuild gearbox for bad gear(s)/bearing(s).
!