Operation, Adjustments – Fisher D500243X012 User Manual
Page 6
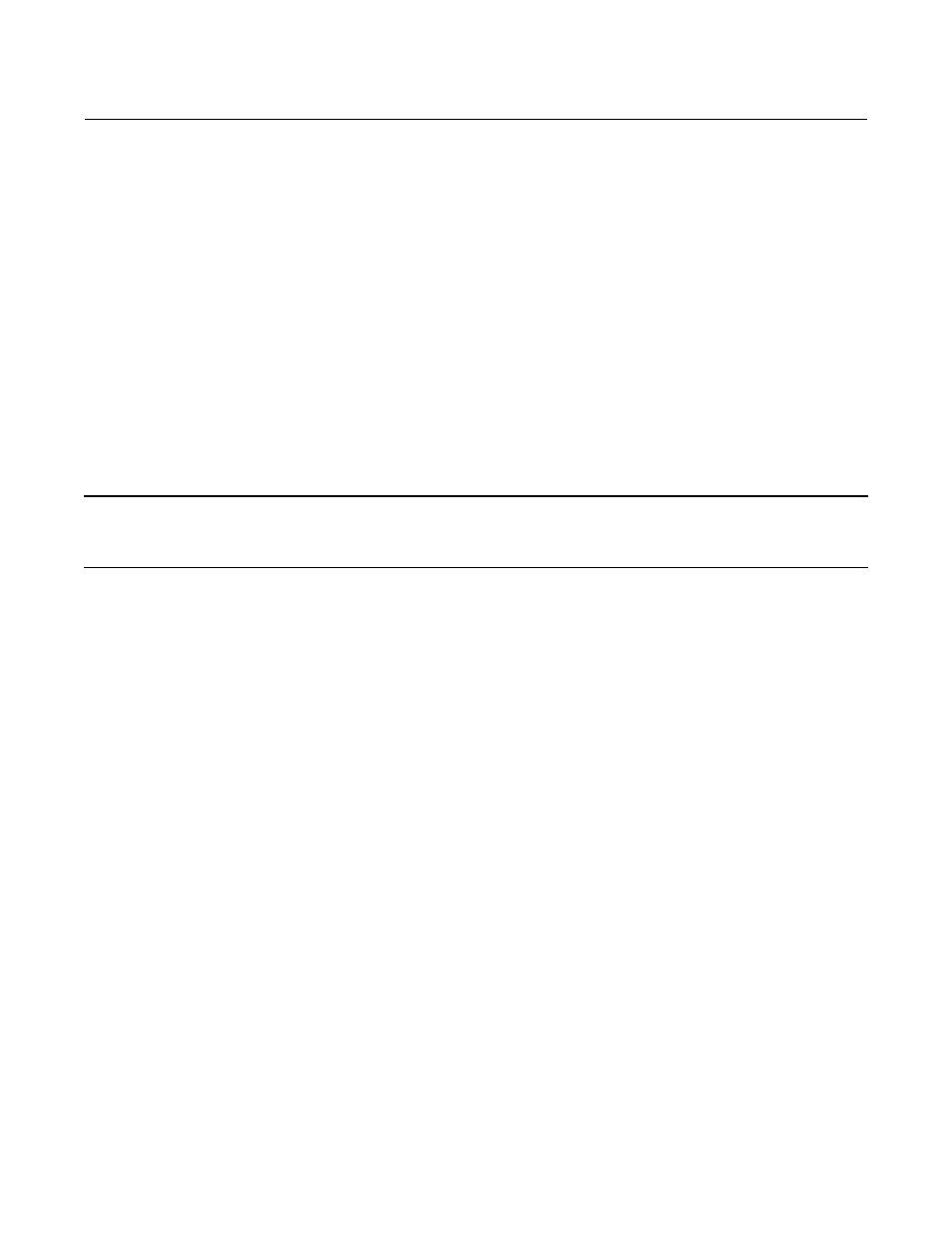
Instruction Manual
D500243X012
1035/El-O-Matic Actuator
August 2012
6
Operation
Units supplied from the factory as an assembly are adjusted per specifications supplied to the factory on the original
order.
Unless the valve/actuator assembly has been damaged during shipment, or the actuator removed for maintenance,
the assembly should be factory adjusted and ready for service.
Actuator Orientation: The 1035 actuator is normally installed with its major axis parallel to the pipeline (see code A,
figure 3). However, the actuator can also be oriented 90 degrees to the pipeline. See figure 3 for standard and optional
orientations. (Note: Code B is not available in the E Series.)
The P or E Series actuator drive shaft turns a full 90 degrees and the stroke is adjustable for the valve closed position.
When necessary, refer to the actuator adjustment steps in this manual.
Note
The A41 High Performance Butterfly valve should not be turned by the power actuator more than 90 degrees of rotation.
Pre-adjust actuator stops to limit travel to 90 degrees or less until adjustment steps are completed.
A double acting actuator can be changed in the field to a spring return unit, or vice-versa (requires different end caps).
Code A actuators can be converted to a code D unit by turning the pistons 180 degrees from the position shown for
code A (See figure 3 for piston and shaft orientation).
Adjustments
E Series actuators provide end cap adjustment screws to limit outward travel of the piston. The inward movement of
the piston is limited by the housing stop (see figure 4).
P Series actuators have a Limit Stop Plate option (LSP) which is used with standard actuator constructions. The LSP is
not used when a Fisher 1080 is used. The LSP, or the 1080, limits travel in either direction for any construction. Refer to
figure 4.
To adjust the travel stops, refer to the valve instruction manual for open and closed positions of the valve. Upon
assembly, ensure that the power actuator does not drive the valve past 90 degrees of rotation. Valve component parts
can be damaged if high actuator air pressure is applied past 90 degrees. Travel limits must be set in the actuator, not in
the valve. It is recommended that the valve be out of the pipeline when adjusting travel limits.