Actuator assembly, Repair kits, Lubrication – Fisher D500243X012 User Manual
Page 16: Installing the drive shaft
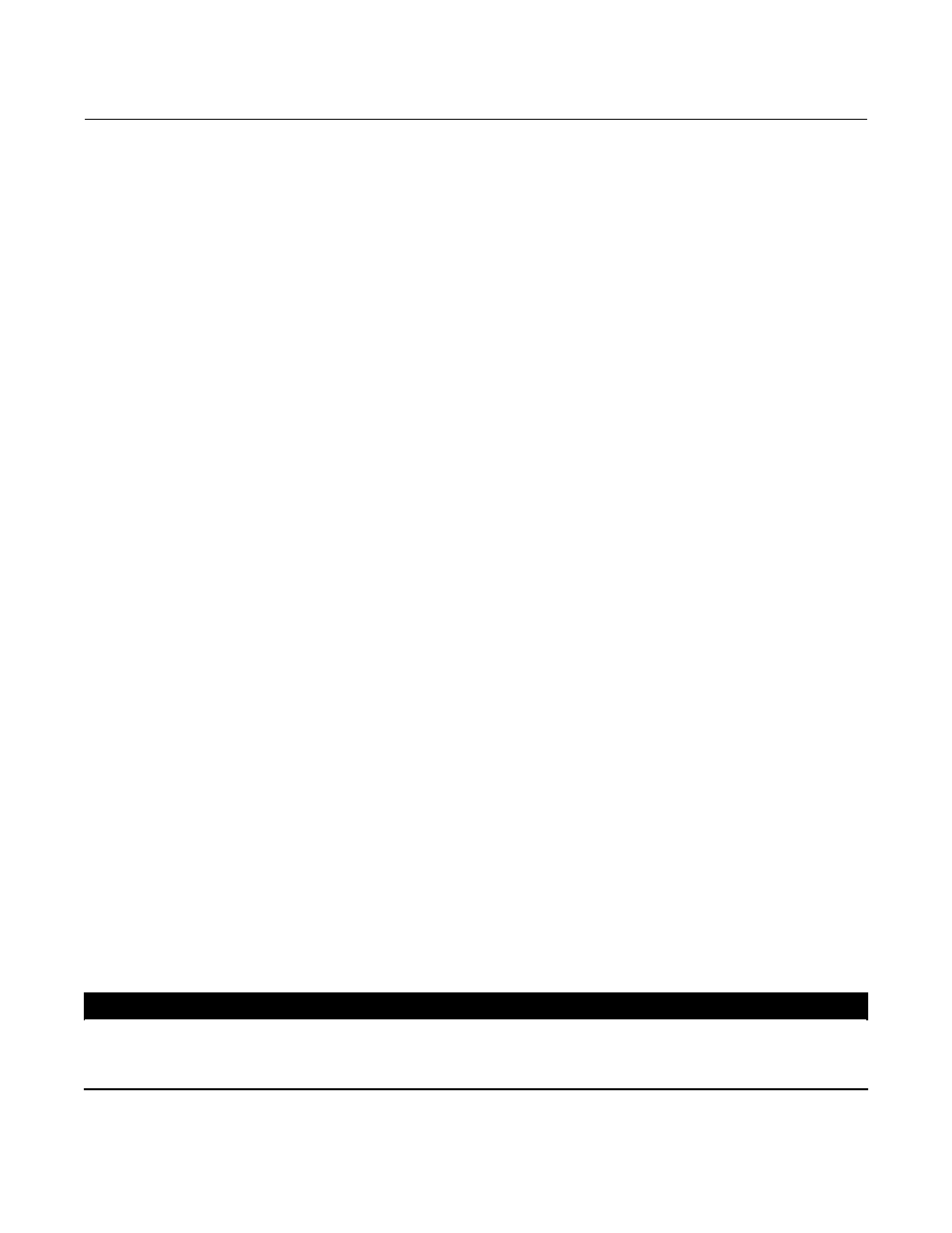
Instruction Manual
D500243X012
1035/El-O-Matic Actuator
August 2012
16
2. Remove the drive shaft (E Series key 3, P Series key 5, figures 11 and 12) through the bottom of the actuator.
3. For P Series actuators: remove the Piston Gear Rack. The gear rack in the P Series actuators is a separate part (key 6)
and is held in place with a socket head cap screw (key 22). Both gear racks can be removed and replaced by
removing them from the pistons.
4. Ensure that all actuator parts are clean and ready for assembly. Inspect the actuator body and component parts for
wear or scratches. If the inside wall of the body is scored the actuator will leak. Light traces of scoring, barely
detectable to the touch, are acceptable. Obtain replacement parts from your Emerson Process Management sales
office.
Actuator Assembly
Repair Kits
Repair kits are available for re-assembly. The large repair kit provides O-rings, guide bands, bushings, and bearings.
The small kit provides a set of soft parts only for the actuator. Repair kits are available for standard, low temperature,
and high temperature actuators. Refer to the Repair Kits table at the end of this manual.
Lubrication
Refer to the Specifications table for temperature ranges.
Standard and High Temperature Actuator: Lubricate the actuator moderately with a complex calcium sulphonate
grease suitable for the application's temperature range. Use the Parts Kit for the appropriate temperature application.
Low Temperature Actuator: Lubricate the actuator moderately with low temperature silicone grease. Use the Parts Kit
for standard and low temperature applications.
Lubricate the actuator moderately with an appropriate grease. Apply a light film of grease to all O-rings, gear racks,
bearings, bushings, and guide bands. In the following steps, lubricate all moving parts during re-assembly.
Installing the Drive Shaft
E Series actuators: Some constructions use a Dual Stop arrangement. The housing adjustment screw is used with a pin
located in the drive shaft, and a stroking adjustment cam mounted on the shaft for the stop. Ensure the cam is aligned
correctly with respect to the housing adjustment screw. Use figure 4 as a guide for alignment.
1. Replace the top and bottom shaft bearings (keys 20 and 12) in the actuator body.
2. Insert the adjustment screw, if applicable, and thread it into the body a few turns, and hand tighten the hex nut. The
adjustment screw should be loose enough to allow full travel of the cam and pistons.
3. Place the cam (see figure 4) on the small end of the drive shaft. Position the cam on the shaft so the pin is located in
the open section of the cam.
4. Install the O-rings and guide bushing on the drive shaft. The guide bushing may have to be cleaned of grease, rolled
tightly around the drive shaft and held in place while inserting into the actuator housing.
CAUTION
When inserting the drive shaft, be sure to keep the O-Rings from becoming trapped and damaged between the pinion and
the actuator body. To verify the condition of the O-Rings at the end of the installation, cycle the actuator 5 times and run a
soap bubble test on the seal on both the top and bottom of the drive shaft.