Leslie Controls CONTROL VALVES DLOS-2 & DDLOS-2 (150/300) User Manual
Page 6
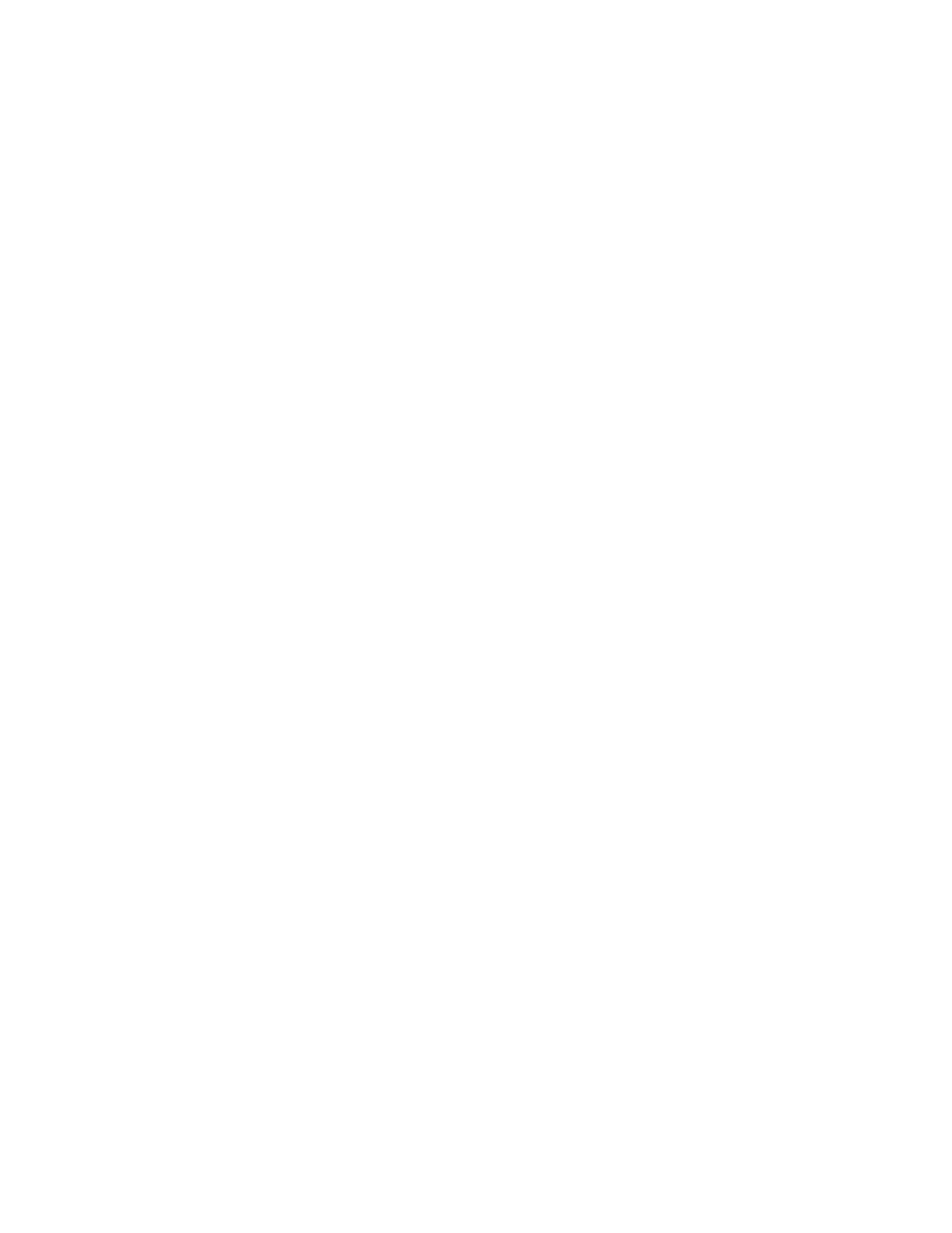
6
5.
Remove bonnet gasket (8), seat retainer (5),
seat ring (4) and seal (3). If necessary,
remove seat ring by forcing a wooden dowel
into seat bore and lifting.
CLEANING
1.
Clean all parts thoroughly. Polish valve
plug stem with crocus cloth. It should be
smooth and free of scratches in packing
area. Use approved, non-residue forming
solvent for cleaning. Wipe dry with clean
cloth.
2.
Inspect all parts and replace any excessively
worn or damaged part.
3.
Install a new packing set of braided Teflon
graphite or Teflon chevron rings as shown
on packing installation sketch Fig. 3, 4 or 5.
See previous section on renewing valve plug
stem packing.
4.
The packing bearings have a long wearing
life material which under normal usage
should not require replacement, however, if
damaged or worn the packing bearing (12)
and/or the bonnet (6) must be replaced.
(Lower bearing in bonnet is not supplied
separately.)
5.
The gasket (8) and seal (3) should be
replaced each time the valve body
subassembly is disassembled for cleaning.
All LESLIE control valves are made of the finest
material obtainable, time-tested and backed by
over seventy-five years of know-how.
Machining is done by expert craftsmen and each
valve is inspected and service tested before
shipment to you.
REASSEMBLY
VALVE
BODY
SUBASSEMBLY LAPPING VALVE PLUG
AND SEAT
1.
Insert raised face of seat ring (4) into seat
retainer cage (5) and place these into bore of
valve body bridge.
2.
Place new bonnet gasket (8) into body
recess.
3.
With light pressure and turning motion
assemble valve plug (2) to the bonnet (6)
being careful not to damage bearings or
packing set (17).
4.
Apply very thin film of superfine lapping
compound to the valve plug seating surface.
5.
Assemble bonnet (6) complete with valve
plug (2) to valve body (1) applying nuts (10)
only finger tight to studs or bolts (11). The
bonnet acts as a guide when grinding valve
plug.
6.
Use wrench on flats of valve plug stem for
turning valve plug (2). Do not bear down on
valve plug stem when lapping. Weight of
parts is sufficient to cause lapping action.
7.
As lapping progresses lift valve plug off seat
occasionally and rotate 45˚ to keep
compound evenly distributed. Remove all
traces of compound after lapping. Excessive
lapping should be avoided.
8.
Remove bonnet nuts (10), bonnet assembly,
and all body assembly parts. Then remove
all traces of lapping compound from both
valve plug (2) and seat ring (4). Check that
a fine continuous ring of contact has been
made on both seats. The contact ring should
be visible but without depth.
9.
Apply silicone grease to seat ring seal (3)
and insert seal into groove of seat ring (4).
10.
Insert raised face of seat ring (4) into seat
retainer cage (5) and place these into bore of
valve body bridge. Seat ring (4) sealing face
must be firmly seated in place.
11.
Place the bonnet gasket (8) in body recess
and add the bonnet assembly. Apply nuts
(10) to bolts or studs (11) and tighten evenly
for metal to metal joint.
12.
Place actuator back on bonnet. CAUTION:
For reverse acting actuators only, air
pressure must be supplied to the diaphragm
chamber sufficient to cause actuator stem to
lift its full travel so valve plug threads may
later be engaged.
13.
Place packing flange (13) with concaved
side of hole facing down thru window of