Leslie Controls CONTROL VALVES DLOS-2 & DDLOS-2 (150/300) User Manual
Page 2
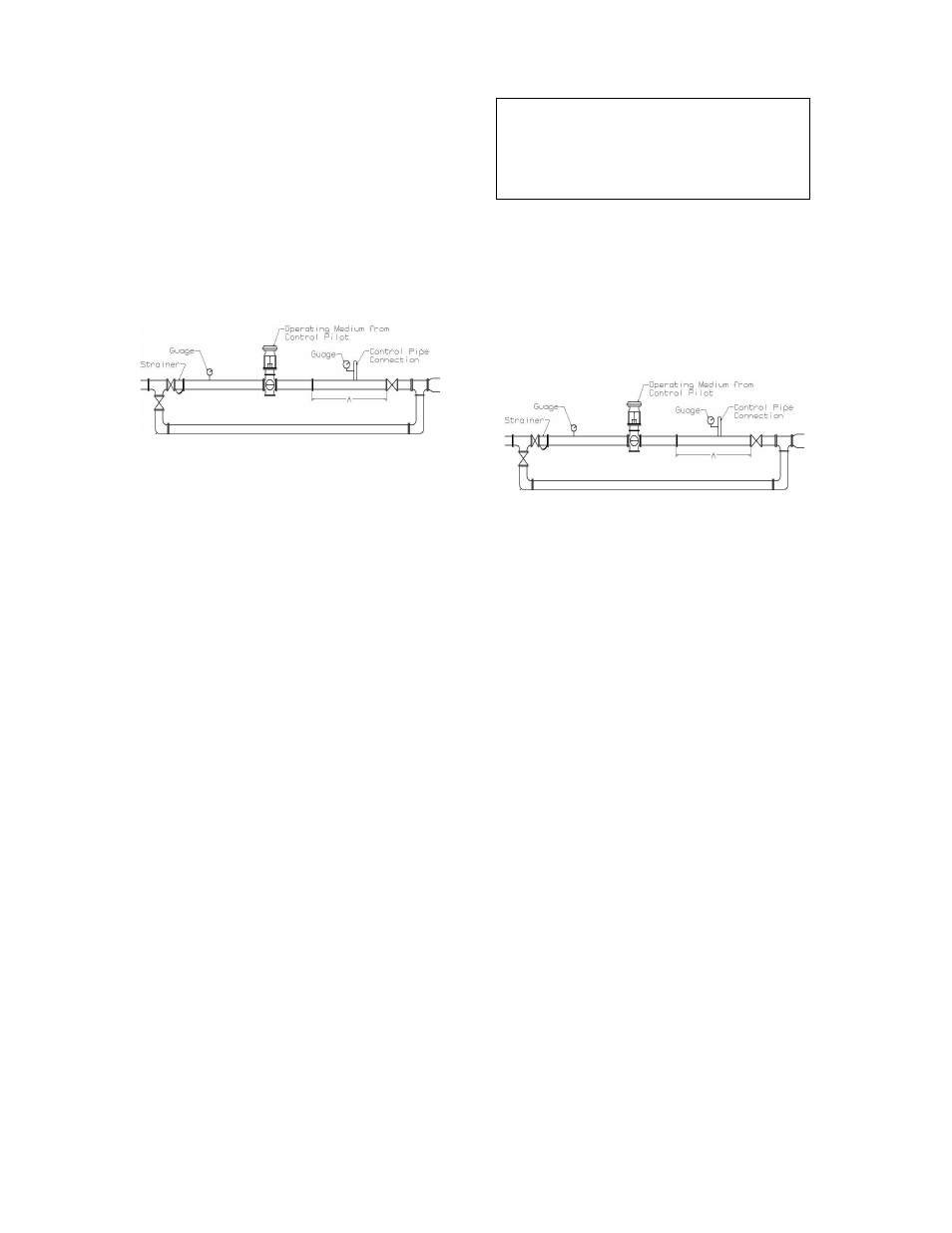
2
SECTION I – INSTALLATION
1.
VALVE POSITION
Install control valve in the highest horizontal line
of piping in an accessible location and with
arrow on side of valve body in direction of fluid
flow. Control valve may be placed in any
position, but upright is preferable for ease of
maintenance.
Figure 1 - Typical Installation Expand as
required for fluid flow
2.
PROBLEM PREVENTING
PROCEDURES
•
Provide removal space above, below and
around control valve for easy removal of
parts during maintenance. See Dwg.
10/9.4.1 or 10/9.4.3 for dimensions.
•
Blow or flush out pipelines thoroughly
before installing control valve.
•
Protect control valve and following
equipment with a SELF-CLEANING
STRAINER.
•
Install stop valves and gauges in inlet and
outlet lines to provide means for checking
adjustment and operation of equipment.
•
Provide proper inlet and outlet drainage in
steam service to prevent water hammer or
possible erosion in equipment.
•
Adhere to good piping practice. Install a
bypass around the control valve.
3.
Connect operating medium tubing from
control pilot, instrument or loading device to
diaphragm chamber connection of control
valve or to valve positioner, if one is in use.
Maximum allowable operating pressure for
diaphragm actuators is 60 psig.
4.
Recommended Piping for Control of
Compressible Fluids at Values of 25% or
Less of Inlet Pressure.
Expand outlet pipe to twice control valve inlet
pipe size. Use tapered expander.
•
Connect control pipe for control pilot ahead
of outlet stop valve and at least 2’ to 3’
downstream from end of expander.
•
Make control pipe connection at least 18” to
2’ from outlet stop valve, any elbow or other
flow direction changing fitting.
Figure 2 - Typical Control Valve Station for
Control of Compressible Fluids at 25% or
Less of Inlet Pressure. Expand further as
required for fluid flow.
NOTE: Where sensing impulse is taken 2’ to 3’
downstream from control valve (expander),
dimension “A” minimum of 6’ to 10’ will
provide lowest noise and velocity factors,
accurate pressure sensing and reasonable
bypass length.
SECTION II – OPERATION
1.
Close inlet and outlet stop valves.
2.
Check that control valve responds properly
through rated travel in relation to changes in
operating pressure on the diaphragm. Rated
travel is shown by position of travel
indicator on valve stem relative to travel
indicator scale on yoke.
3.
Manually operate control valves fitted with
manual operating devices through rated
travel to check freedom of movement.
Return manual operating device to its
standby position.
4.
Place control valve in operation in
accordance with instructions furnished with
control pilot or operating device.
CAUTION!
The piping system must be adequately
designed and supported to prevent
extraordinary loads to the pressure