Figure 15 - a typical boundary-scan ic, Preliminary information, Jtag support – Mitel DISTRIBUTED HYPERCHANNEL MT90840 User Manual
Page 23
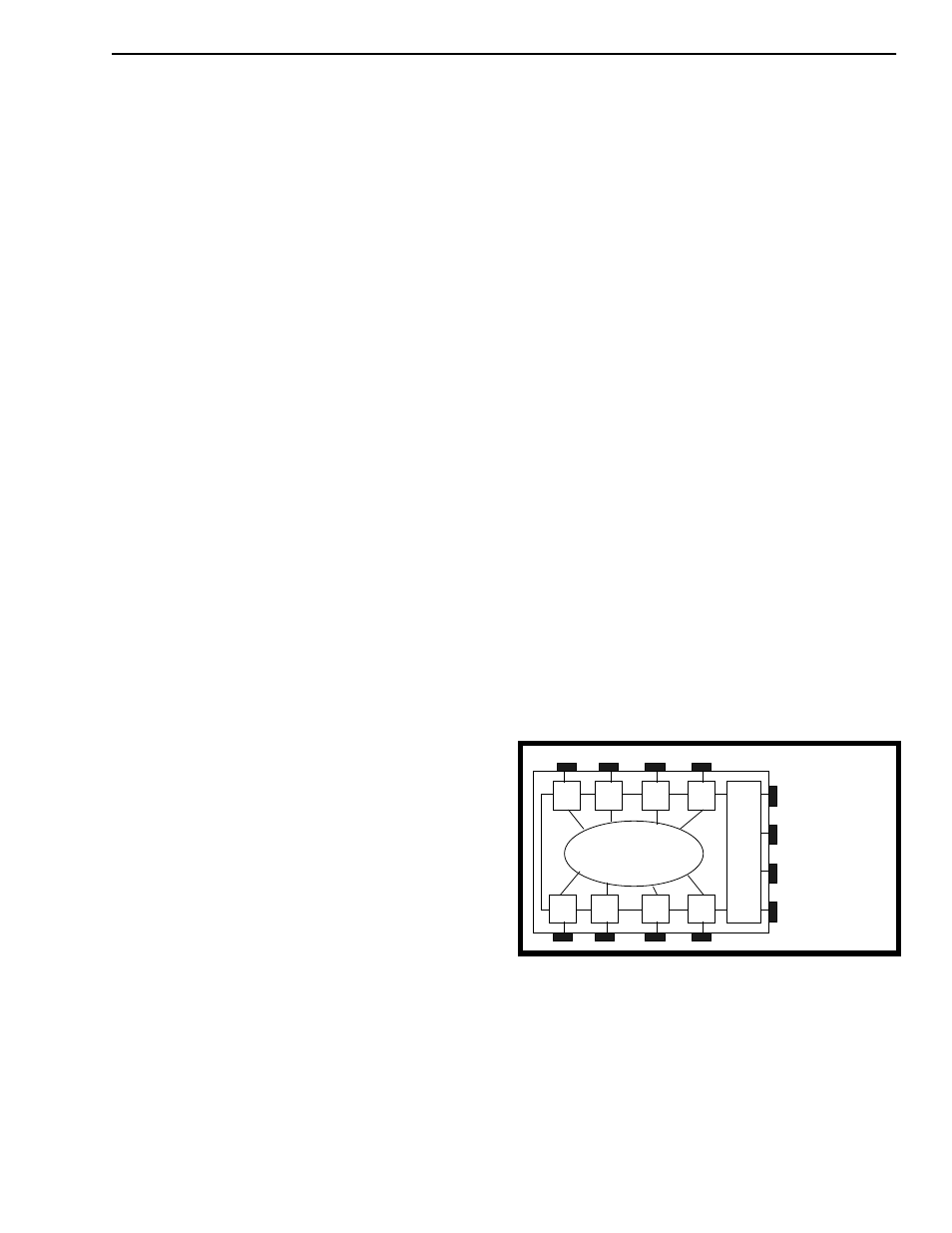
Preliminary Information
MT90840
2-253
DR1-0 and FDC in the IMS register) before
programming the RPCM.
b)
The GPM Register is written. The CPU sets the
Block-Programming Enable (BPE) bit to HIGH
and the Block-Programming Data (BPD7-4) bits
to the desired value. This action causes the
contents of the BPD7-4 bits to be loaded into the
four most significant bits of all addresses in
TPCM High, or RPCM High (as set by the
Control Register).
c)
The user waits 250
µ
sec (two frames) to allow
the TPCM High (2430 positions) or RPCM High
(512 positions) to be entirely loaded with the new
pattern.
d)
After 250
µ
sec, the user should check that the
BPE bit is LOW, indicating that the Block
Program completed successfully. If the BPE bit
does not return to LOW, the necessary TDM
clock input may not be available. The BPE bit
can be written LOW to force an end to the Block
Programming.
Procedures a, b, c, and d must be performed twice if
both TPCM and RPCM have to be initialized.
Block-programming requires stable F0 and PPFRi
framing to function properly. If the framing jumps
during block-programming, a section of memory may
be missed. RPCM block-programming is dependent
on the C4/8 serial port clock and F0 framing. TPCM
block programming is dependent on the PCKT clock,
and F0 framing (PCKR, PPFRi and F0 in TM2). DIN
should not be active during block programming.
If there is some doubt about the quality of the clocks
in a particular application, block-programming
options include:
-1- If a stable C4/8 serial port clock is not available,
or if a stable F0i frame is not available, use TM2 with
Internal Clocks (INTCLK=1) to perform
block-programming of RPCM.
-2- If stable PPFRi framing is not available in TM2,
disable the external gate driving PPFRi and use
free-running framing to perform block-programming
of TPCM (and/or Internal Clocks mode to
block-program RPCM).
The interrupt source bits can also be monitored
during block-programming. If PPCE, or RXPAA (in
TM2), or TXPAA (in TM1), is asserted during
block-programming, a framing error has occurred
and the block-programming should be repeated.
Timing Mode Initialization
On system power-up, the CPU should program the
MT90840 IMS, GPM, and TIM registers to establish
the data rates, the Timing Mode (1,2,3,4), and the
framing polarity of the device. The MT90840 will then
adjust its internal rate conversion and time
interchange circuits to accommodate the different
rates set at both data ports.
To perform the rate conversions between the serial
and the parallel ports, the MT90840 provides a
phase alignment circuit, monitored by the RXPAA
and TXPAA interrupt bits. In TM1 and in TM2 with
external clocks (INTCLK=0) the phase alignment
circuit works automatically to maintain the relative
phase of the serial and parallel ports. The DIN bit in
the GPM register works with this circuit by reducing
the window, forcing the phase alignment circuit to
center the relative phases.
After the parallel and serial port reference clocks
(PCKT/PCKR and C4/8R1/C4/8R2) are stable, the
DIN bit in the GPM Register can be set HIGH. The
DIN bit will auto-reset itself after 8 frames, returning
to LOW. (It can also be written LOW by the CPU.)
The DIN bit procedure is especially useful in TM2. In
TM1 the DIN bit also centers the phase relation, but
the movement of the transmit parallel port timing
during the 8 frames that DIN is asserted may cause
data or framing errors in connected devices. The
RPCM and TPCM should not be written to by the
CPU while DIN is asserted.
JTAG Support
Figure 15 - A Typical Boundary-Scan IC
The MT90840 boundary-scan circuitry functions in
accordance with IEEE Std 1149.1a (often referred to
as JTAG boundary-scan). The standard specifies a
design-for-testability technique called
Boundary-Scan Test (BST). A boundary-scan IC has
a shift-register stage or ‘Boundary-Scan Cell’ (BSC)
in between the core logic and the I/O buffers
adjacent to each I/O pin. The boundary-scan
cellscan control and observe what happens at each
CORE LOGIC
T
A
P
C
O
N
T
R
O
L
L
E
R
TEST DATA IN (TDI)
TEST DATA OUT (TDO)
TEST CLOCK (TCK)
TEST MODE
BOUNDARY -SCAN CELL(BSC)
BSC
BSC
BSC
BSC
BSC
BSC
BSC
BSC
SELECT (TMS)