Torque bias, Chapter 2 – explanation of functions – Hitachi SJ300 Series User Manual
Page 15
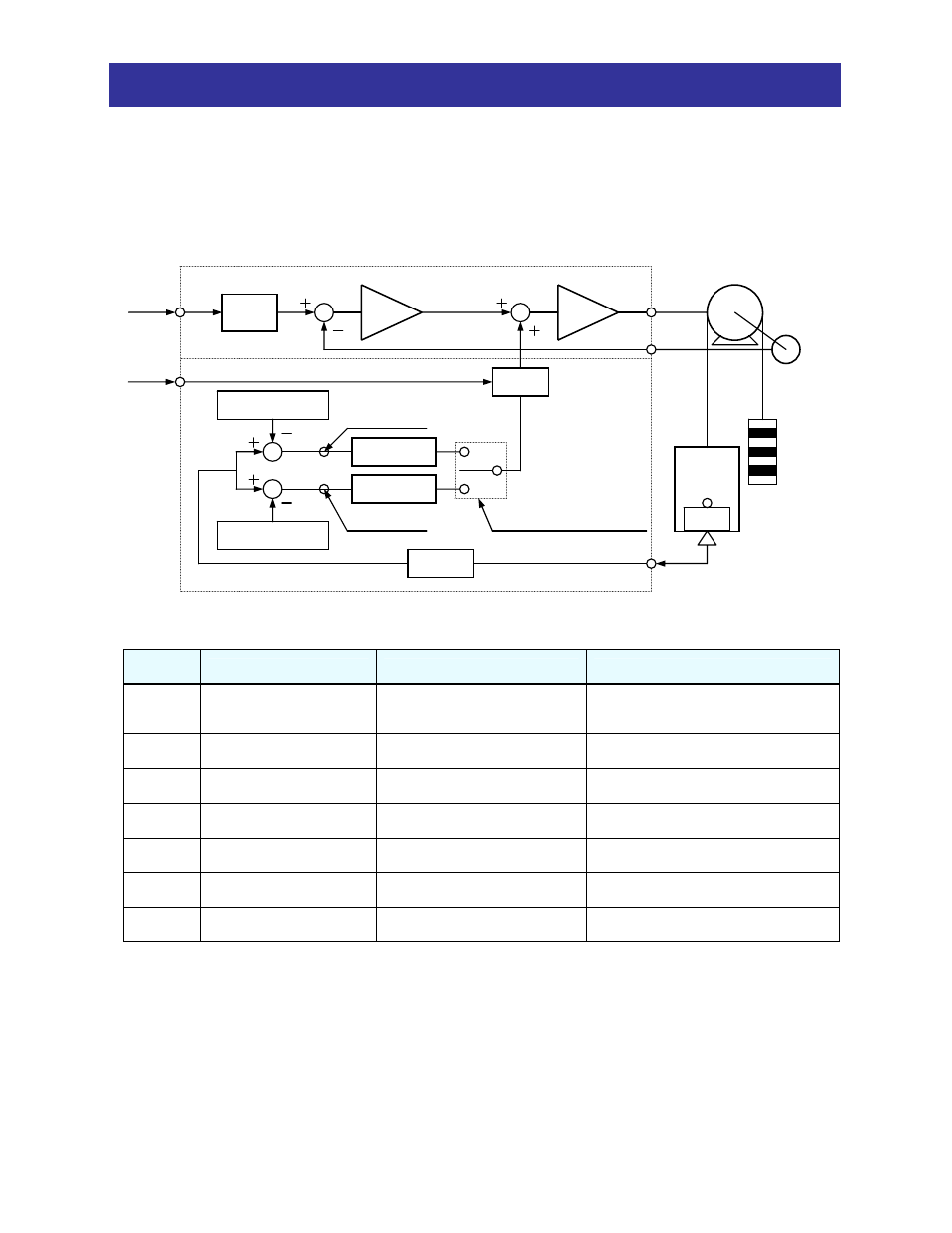
Chapter 2 – Explanation of Functions
2.4 Torque
bias
The inverter is able to accept an analog voltage signal from a load cell that represents car weight. This
signal is used to adjust the instantaneous starting torque to achieve smooth motion regardless of load.
Motor
LAD
ASR
ACR
Counterweight
HOLD
FW side gain
RV side gain
FW side balance
value110)
RV side balance value
Filter
Measure
Target f
Hold signal
O2
SSD
Changeover according to
the direction
Point A
Point B
Figure 4 – Torque bias circuit diagram
Cabin
Encoder
< Additional setting items>
Function
Code
Function Name
Setting Range
Remarks
A071
Selection of Torque Bias
Input
-
00: O Input
01: OI Input (Note 2)
02: O2 Input (Note 3)
P110
FW side balance value
0.0 - 10.0 (V)
Total weight output at balanced point
(FW direction side)
P111
RV side balance value
0.0 - 10.0 (V)
Total weight output at balanced point
(RV direction side)
P112
FW side gain
0.0 - 200.0 (%)
Torque value to be added in case of
max. weight (FW direction side)
P113
RV side gain
0.0 - 200.0 (%)
Torque value to be added in case of
max. weight (RV direction side)
P114
Time constant of the filter
5 - 500 (ms)
C001
- C008
Intelligent input
terminals 1 - 8
- 50:
SSD
Note 1: Do not configure the same analog input for torque bias input (A071), frequency source setting
(A001), and torque limit input (B040).
Note 2: When OI input is used for torque bias, the ranges of P110 and P111 are still 0 – 10 V, so it will be
necessary to translate the 4 – 20 mA signal value to 0 – 10 V for these parameter settings.
Note 3: When O2 is selected for torque bias, the range is 0 to +10 V. Negative values are ignored.
15