Spindle orientation – Yaskawa G5 Spindle Orientation User Manual
Page 5
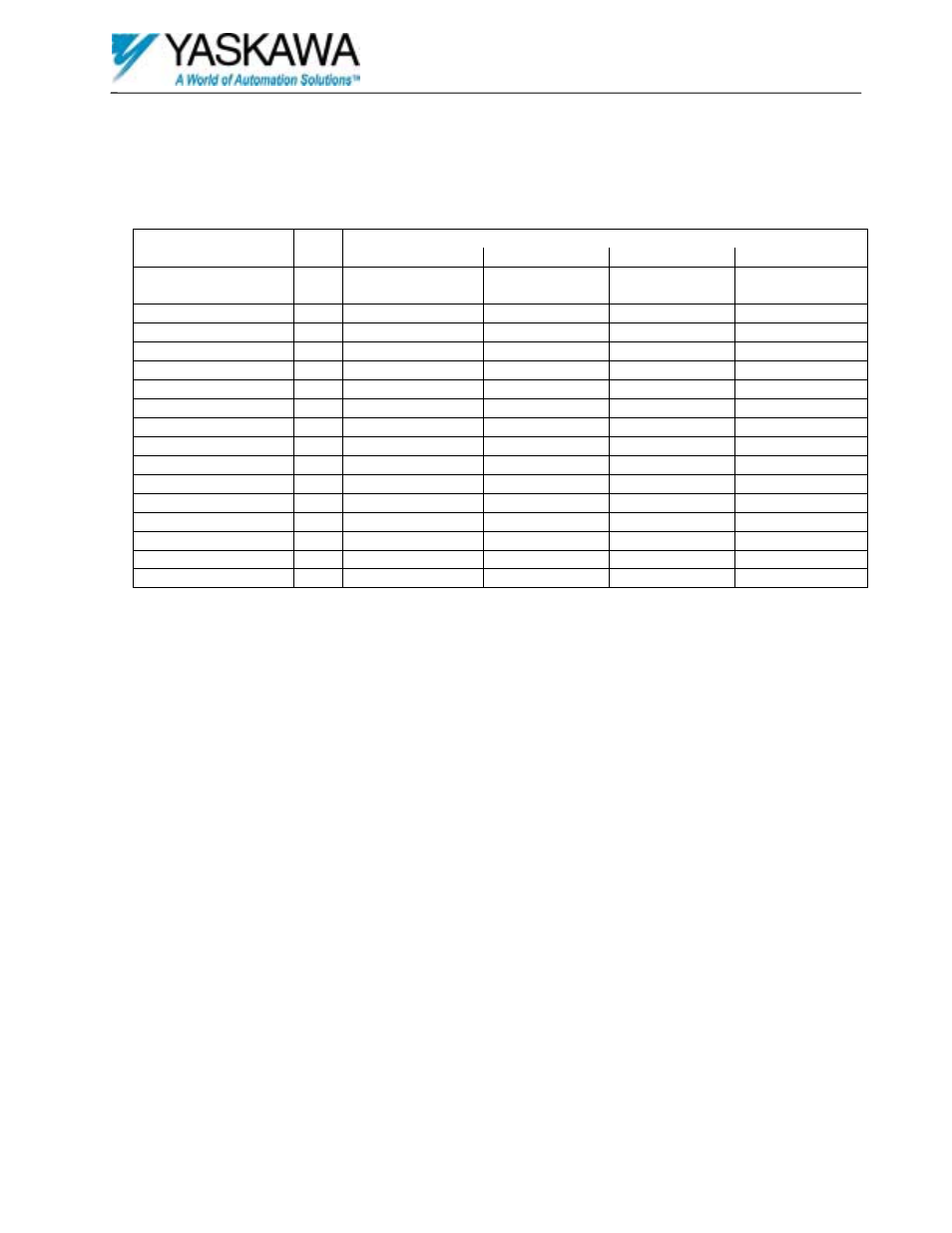
Spindle Orientation
Date: 07/01/04, Rev: 04-07
Page 5 of 14
TM.G5SW.021
at the home position. After the sequence-reset has reset the sequence step to 0 the next orient input will increment it
to 1 pointing to offset value stored at P2-01 as the first step.
2 – Selected Offset – The offset value to be used can be selected via multifunction inputs. The following selection table
will illustrate how steps can be selected.
Selection Table
Multifunction Inputs
Parameter
Number
Step 84: Select MSB 4
85: Select Bit 3
86: Select Bit 2
87: Select LSB 1
P1-03: Marker
Offset
0 Off
Off
Off
Off
P2-01: Offset 1
1
Off
Off
Off
On
P2-02: Offset 2
2
Off
Off
On
Off
P2-03: Offset 3
3
Off
Off
On On
P2-04: Offset 4
4
Off
On
Off Off
P2-05: Offset 5
5
Off
On
Off
On
P2-06: Offset 6
6
Off
On On Off
P2-07: Offset 7
7
Off
On On On
P2-08: Offset 8
8
On
Off Off Off
P2-09: Offset 9
9
On
Off Off On
P2-10: Offset 10
10
On
Off
On
Off
P3-01: Offset 11
11
On
Off
On On
P3-02: Offset 12
12
On On Off Off
P3-03: Offset 13
13
On On Off
On
P3-04: Offset 14
14
On On On Off
P3-05: Offset 15
15
On On On On
To select step 6 requires multifunction inputs 85: Select 3 and 86: Select 2 to be energized. Multifunction inputs
84:Select MSB 4 and 87: Select LSB 1 must be off or de-energized. The sequence steps are bit mapped to the
multifunction inputs. If the 4 inputs are read as a 4 bit binary number its decimal equivalent is the sequence step.
The selection can be made anytime prior to energizing the orient input. Changing the selection while the orient input
is energized will have no affect until the next orient input.
3 – Serial Offset – The offset value will be read from U1-59: Serial Offset. U1-59: Serial Offset can be written to via
serial communications. The serial offset can be written to anytime prior to energizing the orient input. Changing the
serial offset while the orient input is energized will have no affect until the next orient input. U1-58: Sequence Step
will be set to 99 when this method is used and the serial offset is greater than 0.
The value of the offset entered into an offset parameter is controlled by P3-06: Count or Degree. P1- 03: Marker Offset
is not affected by this parameter and always remains as a count value. P3-06: Count or Degree has the following
selections.
0 – Count – The value entered into the offset parameters are in quadrature encoder counts. (PPR x 4) The number of
counts entered will be used as the offset. This can result in more than one revolution during an orient since 32767
counts can be entered.
1 – Degree – The value entered into the offset parameters are in degrees ranging from 0 to 360 degrees. If the value
entered is greater than 360 it will be reduced to then equivalent position within one revolution. (380 = 20)
All offset counts are measured in the counter-clockwise direction facing the position encoder shaft. All offset degrees
are measured in the clock-wise direction. Because of this increasing the offset count will result in the orient position
moving counter-clockwise and increasing offset degrees will result in the orient position moving clockwise. Either
selection provides for absolute orientation regardless of running direction. If the position encoder’s PPR is 1024, the
marker offset places the home position at 12 o’clock and the offset value is 1024 counts the position encoder will orient
at 1024 counts counter-clockwise past the home position. This is the 9 o’clock position. If the home position is set to
12 o’clock and the offset value is 270 degrees the orient position will be at the 9 o’clock position. Both these statements
are true regardless of running direction.