Yaskawa MP2600iec User Manual
Page 24
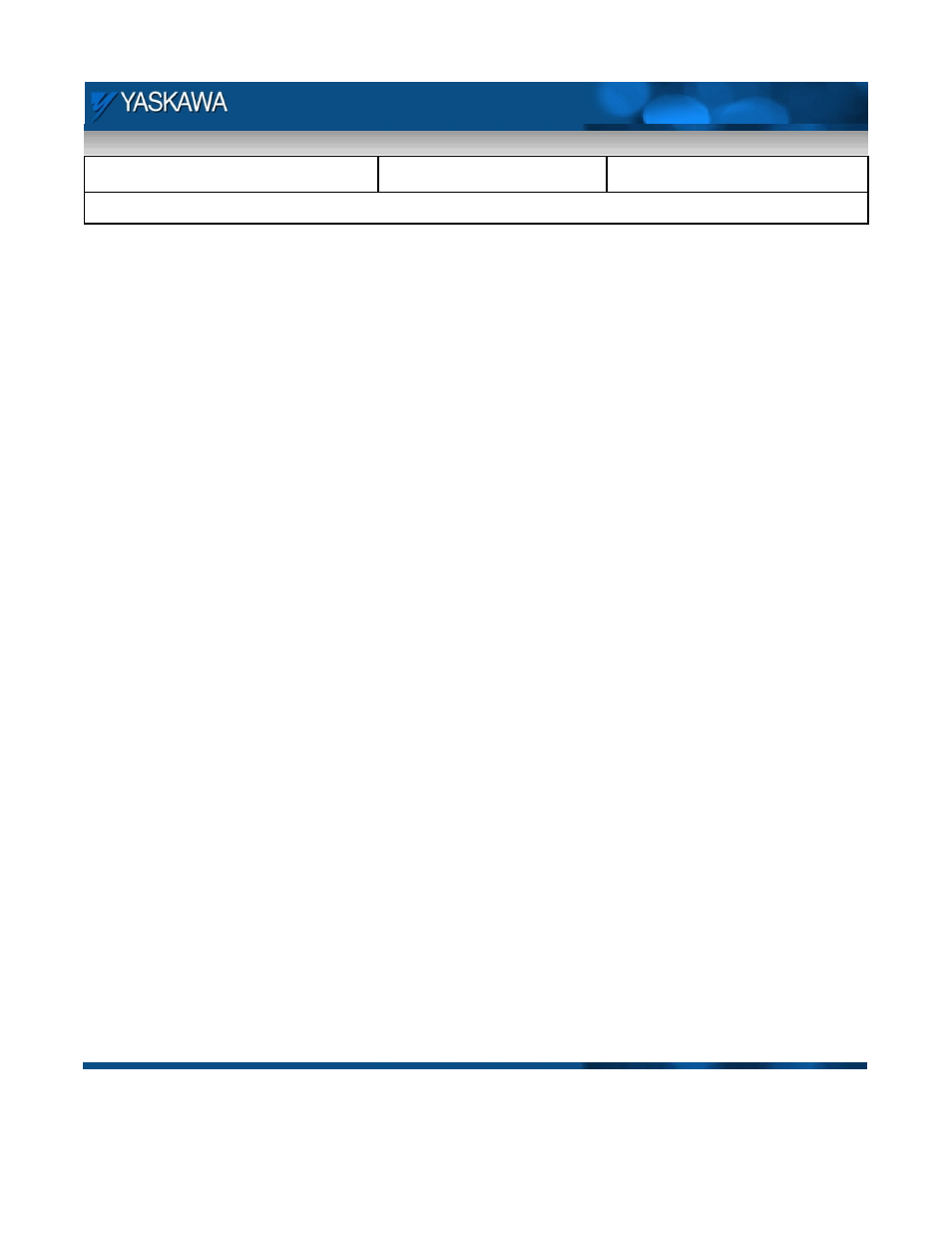
Subject: Demo Instruction
Product: MP2600iec
Doc#: TN.MP2600iecDemo.01
Title: MP2600 Demo Instructions
Doc#: TN.MP2600iecDemo.01 Copyright Yaskawa Electric America
©2011
May 24, 2011
Page 24 of 29
Camming:
Manually position the servo axis such that a distinguishing mark on the load disc coincides with a mark on the
demo that can be used as a zero point. Make sure that the two cam files: TWCam.csv and OWCam.csv are
loaded in the controller. They can be verified by logging into the controller’s web server and checking the
project archive.
The axes will have to be enabled for camming to start.
1) Flip DI6 on.
2) Select Camming from the main menu on the HMI.
3) Choose the cam profile. Make sure the light for the selected profile blips on for an instant. Press Next.
4) Choose the cam master.
5) If virtual master is chosen
a) Start master starts the virtual master motion. Make sure the lamp glows.
b) If the ready to engage lamp is on, Cam engage will engage the cam relation and servo will start
motion.
c) Cam shift will implement a shift in the profile.
d) Pressing Cam scale will implement a 200 % scale. If the scale button is pressed again the profile
is scaled back to 100 %.
e) Disengage the cam to break the virtual master servo axis relation.
f) Stop master will stop the virtual axis motion. Disengage the cam before master is stopped.
g) Repeat steps 3 – 5g for demonstrating the second cam profile.
6) If external encoder master is chosen,
a) Manually rotate the external encoder axis.
b) If the ready to engage lamp is on, Cam engage will engage the cam relation and servo will start
motion.
c) Cam shift will implement a shift in the profile.
d) Pressing Cam scale will implement a 200 % scale. If the scale button is pressed again the profile
is scaled back to 100 %.
e) Disengage the cam to break the virtual master servo axis relation.
f) Repeat steps 3 , 4 and 6 for demonstrating the second cam profile.
7) Flip DI6 off.