4 setup – AEC OFE Blender User Manual
Page 17
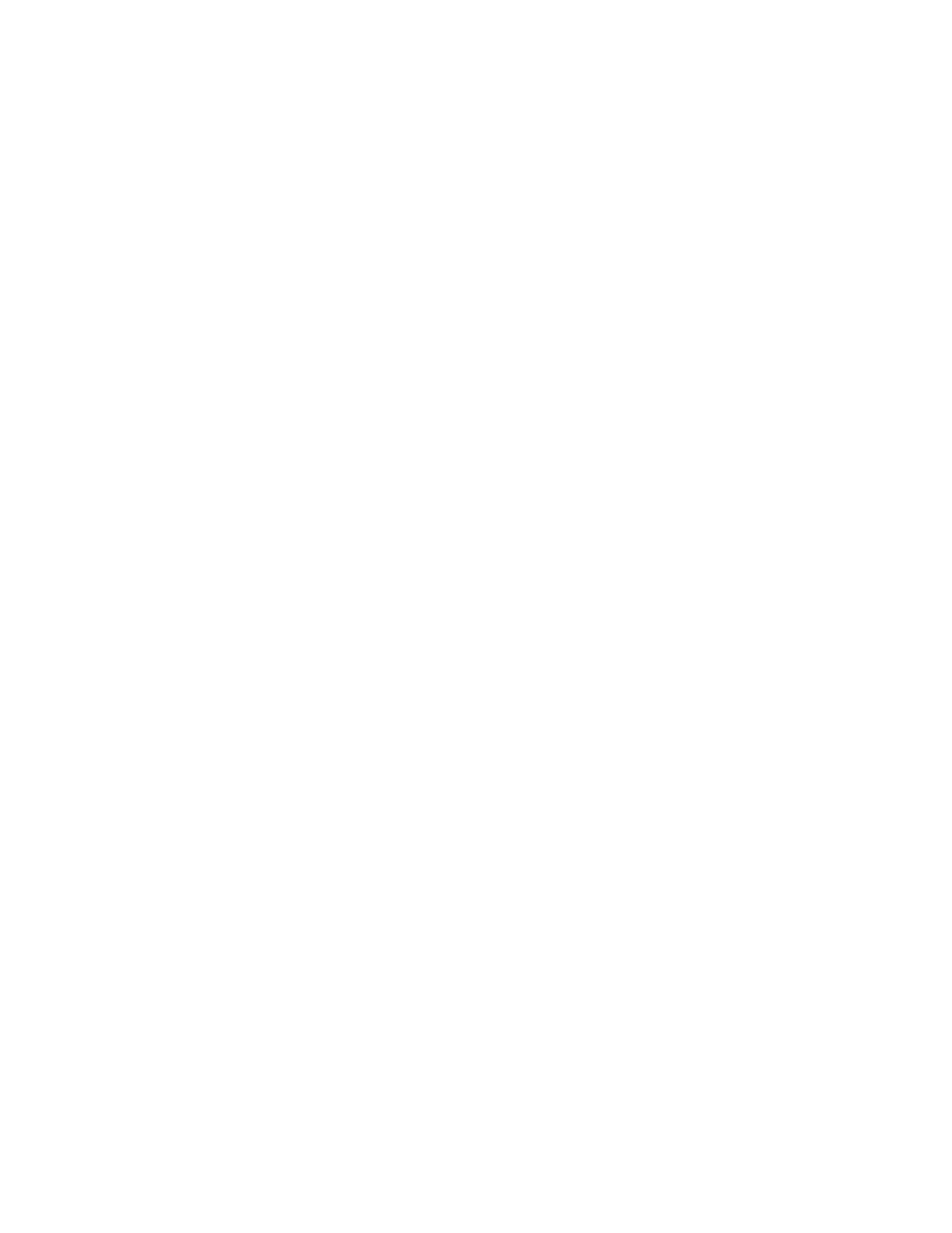
Loss-In-Weight Color Feeders
Chapter 3: Installation
16
Internal Components of the Control Panel
Note: See Section for complete electrical schematics.
This section describes the internal components of the Feeder control panel. It is not the intent
of this section to completely familiarize the reader with the details on industrial control panel
construction or standards, but simply to familiarize the reader with the major components
inside the control panel.
The customer must supply 120/1/50 or 60 (or 220/1/50 or 60) via wires L1 & L2 (N). Please
insure that the earth ground connection is properly connected to an established earth ground.
“Power on” is indicated by a lighted on/off switch.
Audible alarm horn alerts operator to feeder fault.
Input Signals to Programmable Controller
The feeder has two main input signals that it uses from the blending process: the extruder
proximity switch signal and the weigh hopper load cells. This, of course, does not include the
operator touchscreen input.
Load cells require +5 VDC to operate. This is known as the load cell’s excitation voltage.
Output Signals from Programmable Controller
The Feeder uses several output control signals to control the process. All of these are very
similar in nature, the first of which is the auger motor control.
The auger motor outputs are driven from a control output from the controller.
Each Feeder includes an auxiliary customer alarm output. This dry contact can be used to
switch a remote alarm signal.
The customer alarm output is provided to actuate or energize a variety of alarm horns,
buzzers, strobe lights, and beacons. These are normally provided by the customer, and care
will have to be exercised not to exceed the maximum current draw (3 amp maximum). The
contacts will close whenever the control detects a fault that will somehow inhibit the blending
system from properly blending the material.
Note: The customer alarm contact is open if the panel control power is
turned off. This contact is for use with a customer supplied alarm
device as described above. The alarm contact has a maximum load of
3 amps.
3-4 Setup
Installing Proximity Switches
Mount the proximity switch on the rear of the extruder gearbox, and install a bolt or other
similar metal pickup on the rear hub of the extruder screw. Adjust the proximity switch so
that it is reading the pickup. This is done by adjusting the gap between the proximity switch
and the pick-up and adjusting the sensitivity adjustment until the LED light on the proximity
switch lights up each time the pick-up passes. Wire the proximity switch into the feeder
control panel to the appropriate terminal (check the enclosed drawing).