Chapter 21, Milling cutters – Smithy Midas 1220 XL User Manual
Page 90
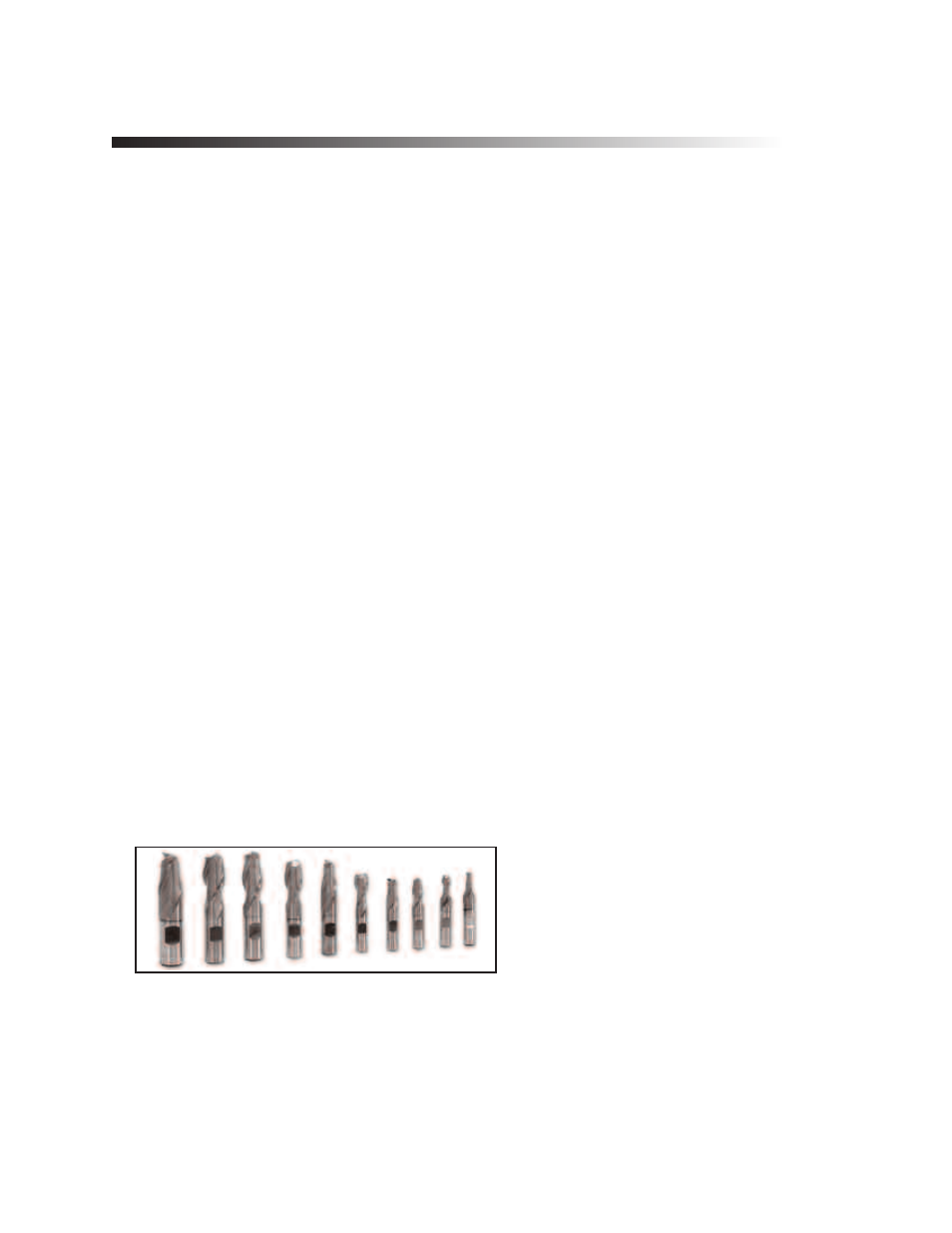
Chapter 21
Milling Cutters
Choose milling cutters for the type of cut, the number of parts, and the material. Rake
angles depend on both cutter and work material. Clearance angles range from 3° to 6°
for hard or tough materials to 6° to 12° for soft materials.
To determine the number of teeth you want, consider the following:
• There should not be so many teeth that they reduce the free flow of chips.
• The chip space should be smooth so chips don't clog.
• Don't engage more than two teeth at a time in the cut.
End Mill Cutters
End mill cutters cut on their ends and sides. They are either solid (cut from a single piece
of material) or shell (separate cutter body and shank). They have two, three, four, or
more teeth and may do right or left-handed cutting. Their flute twist or helix may also be
right or left-handed. Solid end mills have straight or tapered shanks; shell end mill
adapters have tapered shanks.
End mills machine horizontal, vertical, angular, or irregular surfaces in making slots,
keyways, pockets, shoulders, and flat surfaces.
•
Two flute, or center-cutting, end mills (Figure 21.1) have two teeth that cut to the
center of the mill. They may feed into the work like a drill (called plunge milling), then go
lengthwise to form a slot. Teeth may be on one end (single-ended) or both ends
(double-ended).
Figure 21.1 Two-flute end mills have two
teeth that cut the center of the mill.
•
Multiple flute end mills have three, four, six, or eight flutes and may be single or
double-ended. Multiple-flute mills are center cutting or non-center cutting. Don't use
non-center cutting end mills for plunge milling.
•
Geometry forming end mills form particular geometries. They include ball end mills,
roughing end mills, dovetail end mills, T-slot cutters, key seat cutters, and shell end mills.
21-1
For Assistance: Call Toll Free 1-800-476-4849