Troubleshooting – REMKO RKW INOX User Manual
Page 11
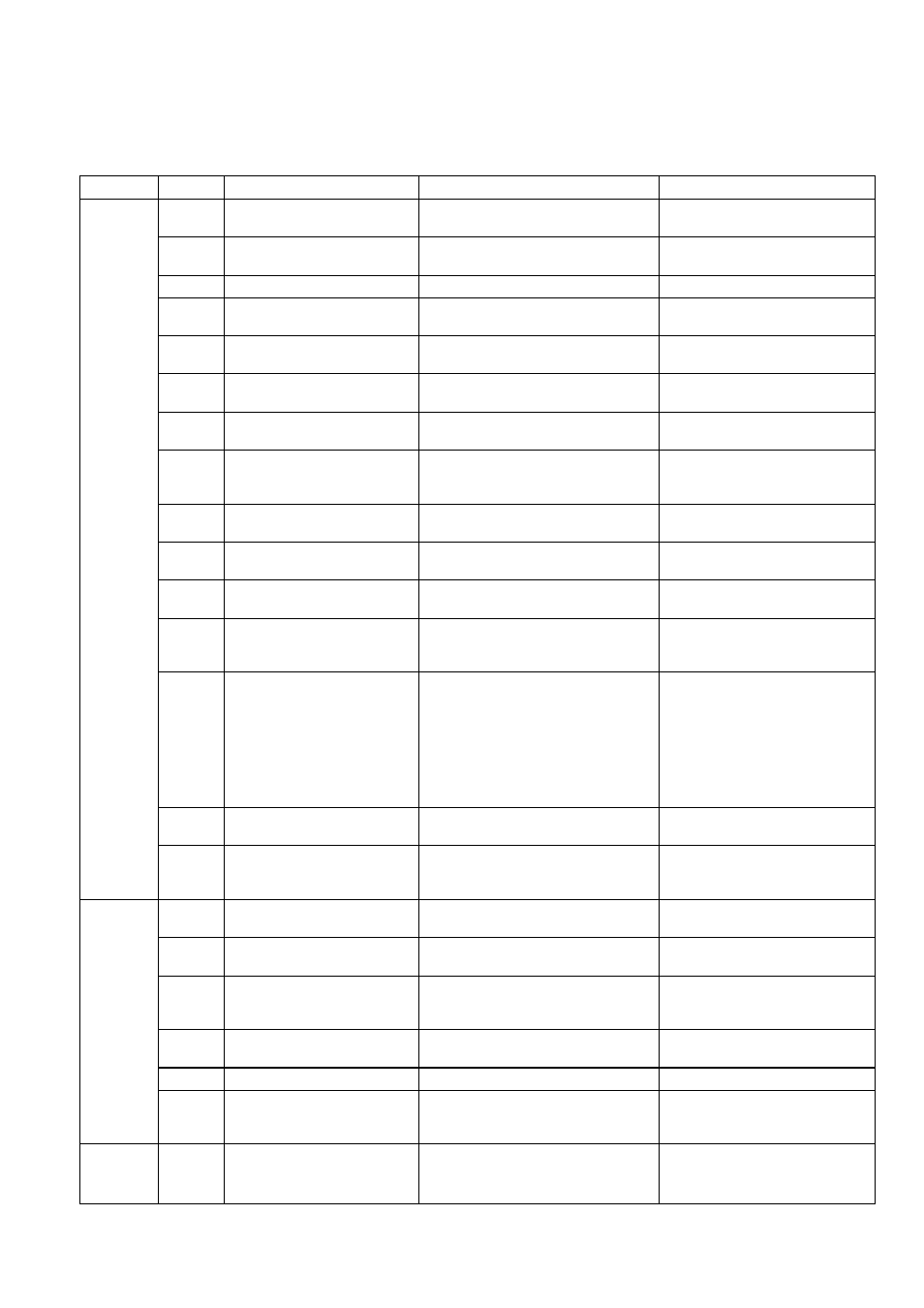
11
Troubleshooting
This unit has been designed based on state-of-the-art manufacturing methods and it has been tested repeatedly to
ensure that it is working properly. However, should problems occur, refer to the following list.
Problem
Alarm
Possible cause
Check
Remedy
The unit
does not
start or it
switches
itself off
automati-
cally.
Power failure
Are all other electrical components
working?
Check voltage and wait for the
unit to start again.
Power fuse / power supply de-
fective
Are all other electrical components
working?
Maintenance by authorised
personnel
Waiting period too short
Is the COMP LED blinking?
Schedule longer waiting periods
Regulation is not working
Is the LINE LED and to the
COOL LED lit up?
Connect current and select the
COOL operating mode
Incorrect discharge tempera-
ture or parameter setting
Check setting
Change setting
E01/E02
E21/E22
High-low pressure alarm
Are the fans rotating?
Is the pressure in the cold cycle OK?
Have checked by authorised
company
E00/E21
Remote control / Connection
to C2-DIN defective
Is the display working?
Is the connection OK?
Replace remote control or re-
establish connection between
CH-DIN and C2-DIN
E03/E23 Compressor overheating
Is the temperature of the compressor
above approx. 100 °C?
Maintain operating ranges, clean
fins
E04/E24
Liquefaction temperature too
high
Are the fins clean and have the oper-
ating ranges been maintained?
Clean fins, place unit in the
shade
E05/E25 Frost protection activated
Is the supply temperature 4°C or
lower?
Increase discharge temperature
E06/E07/
E26/E27/
E40
Sensors defective ST1 to ST6
It is the alarm activated when the
sensor is replaced?
Replace defective sensors
E41
Flow switch (differential pres-
sure monitor) activated
Are the following values OK:
◊
Volume of current (too large/small)
◊
No air in the monitoring pipes
◊
Circulation pump
◊
Does the monitor switch on and off
◊
Stop mechanisms are open
◊
Water pressure too high/low
Have checked by authorised
company
E42
Hardware defective
Does the regulation function
smoothly?
Have regulation replaced by
authorised company
Compressor contact defective
Is the COMP LED lit up and is there
current on the contact?
Have the contact or compressor
replaced by an authorised com-
pany
The unit is
either not
cooling at
all or only
a little bit
Heating capacity was in-
creased
Has there been a structural change? Maintain safety zones
Supply temperature too high
Is the supply temperature approx.
5 ... 10 °C?
Reduce discharge temperature
Air in the system
Have automatic ventilators been
mounted on the highest possible po-
sition?
Ventilate manually or integrate
ventilators
Liquefaction temperature too
hot
Are the fins clean and have the oper-
ating ranges been maintained?
Clean fins, place unit in the
shade, maintain operating ranges
Incorrect parameter settings
Check settings
Change settings
Sporadic operation because
cooling requirements are too
low
Has the system been designed for
smaller measurements?
Increase the quantity of water by
installing a storage module
Water
leaks out
of the unit
Leaks in pipes or defective in-
sulation
Are there leaks and have all lines
been insulated?
Seal and insulate
Incorrect electrical rotational
direction
Did the phase-sequence relay switch
through?
Change the rotational direction