Calibration, Calibration …… 1-5 – Measurement Computing PointScan 200 Series rev.1.0 User Manual
Page 11
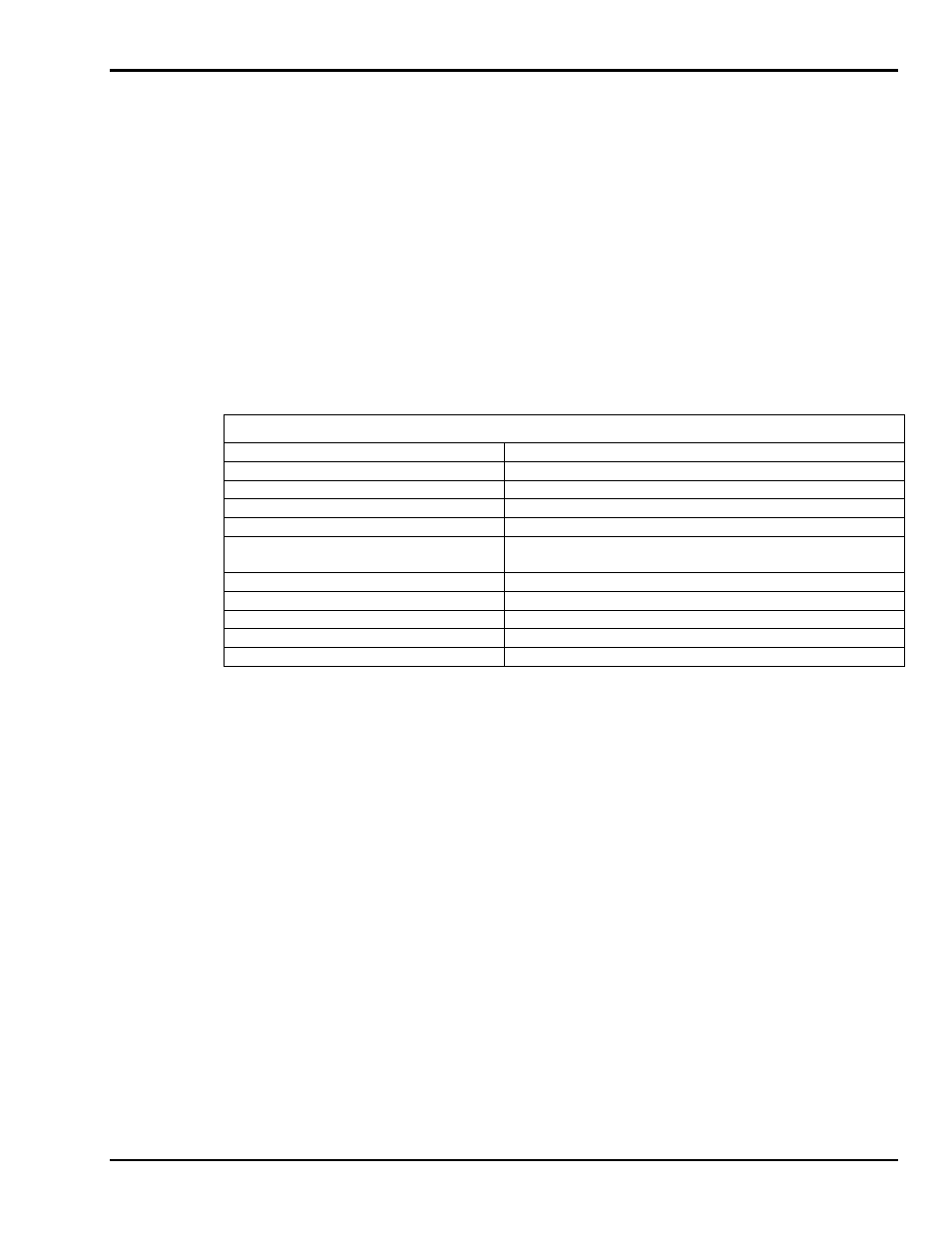
PointScan/200 User’s Manual
9-25-01
General Information 1-5
Calibration
All PointScan/200 Series analog I/O logic modules are factory calibrated over all supported ranges using a
regularly maintained set of standards. Factory calibration data is stored in permanent memory in the logic
module, and cannot be altered. User recalibration may be performed, but is necessary only if inaccuracy in
your field device is observed, or if any of the 100 ohm input shunts are replaced with low tolerance
resistors.
Each analog channel has span and offset calibration settings. Span is the "range" or "gain" of the channel.
Offset is the "zero" setting. Each reported analog I/O value is the product of the factory calibration value
times the user calibration value. The user calibration value is defined as:
(user span value * raw value) + user offset
The user span is a unity value (1) by default. The user offset is zero by default.
Note:
All factory and user calibrations are performed in software. There are no adjustment
potentiometers inside the logic modules.
User calibrations are performed using the Remote IO Toolkit utility. Refer to the Remote IO Toolkit on-
line help system for information on calibrating PointScan/200 Series analog I/O.
Communicating with PointScan/200
Protocols supported
Modbus, ASCII/RTU, and proprietary
Wiring configuration
RS485 two-wire partyline
RS485 isolation (module to module)
1200 Volts RMS 1 minute
Supported baud rates
2400, 4800, 9600, 14400, 19200, 38400, 57600 baud
Factory communications settings
9600 baud, no parity, 8 data bits
Cable recommendation
Shielded, twisted pair with drain wire desirable. Data rated
cable is recommended for greater distances.
Limitations: cable up to 1 km
24 AWG and 57,600 baud
cable up to 2 km
20 AWG and 38,400 baud
cable up to 3.5 km
18 AWG and 19,200 baud
Number of modules on one RS485 port
32 maximum
Number of addressable modules
128 with PointScan/441