Gsp control technical information – Gullco SAM CM-02-250 User Manual
Page 10
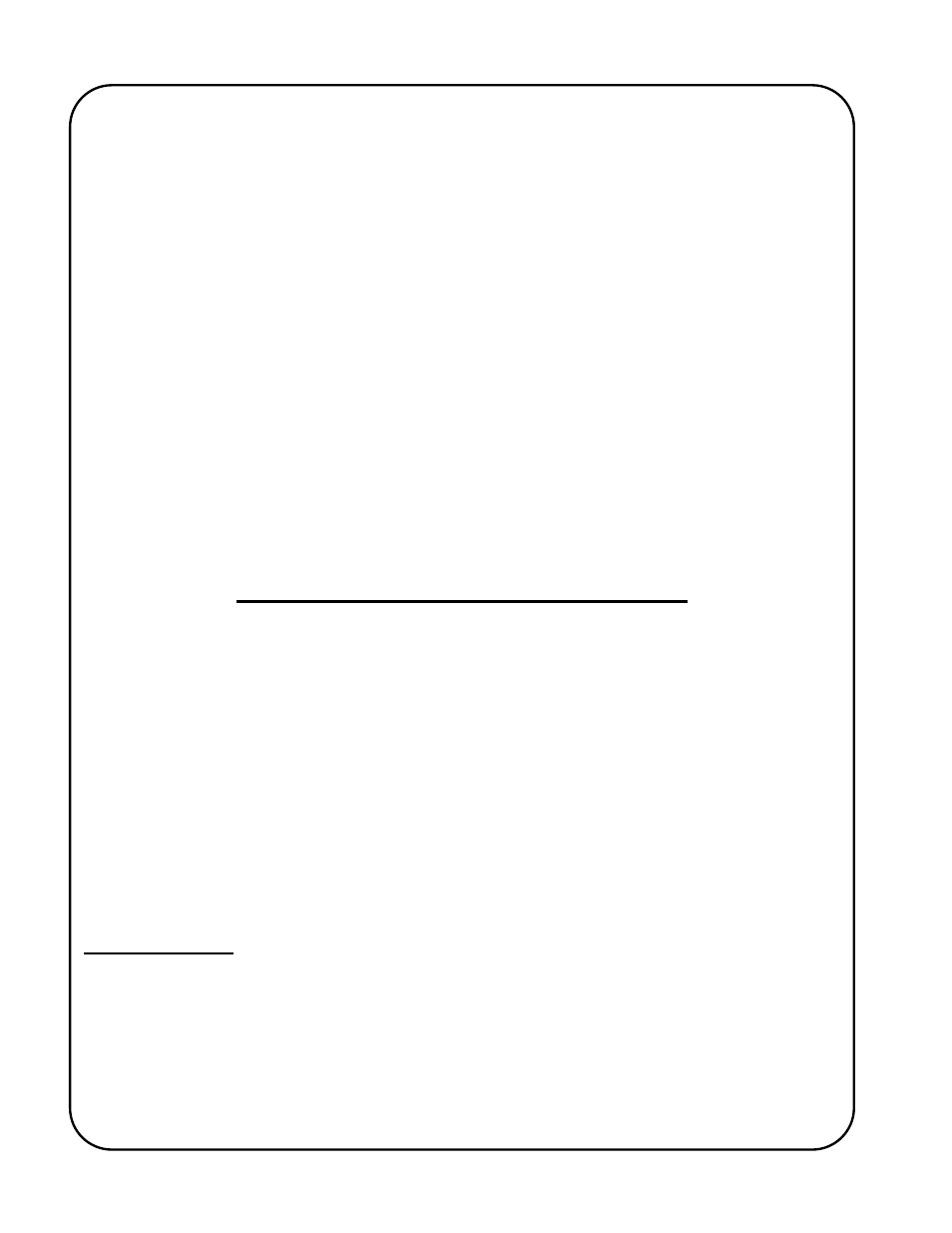
8
The Forward/Neutral/Reverse Switch – is used to select the travel direction desired in both Manual
Mode and Automatic Mode.
The Forward position is used to select increment, while the reverse position is
used to select decrement as the method of changing the values/settings of the program variables (refer to the
section “Programming The Automatic Cycle Parameters/Variables” later in this manual for further details of
this function).
The Speed Adjustment Knob - is used to increase (clockwise) or decrease (counter-clockwise) the
travel speed of the carriage, both in Manual Mode and Automatic Mode. The carriage will travel at
full speed during the no-weld part of a stitch cycle. The speed display will show the set speed when
the Run/Stop switch is in the Stop position and the Forward/Neutral/Reverse switch is in the Neutral
position.
The Program Variable Selector Switch – is a ten position rotary switch, used to set some of the
values and settings which apply to the Automatic Cycle. This selector switch is an extended rotary
switch.
Refer to the section “Programming The Automatic Cycle Parameters/Variables” later in this manual
for further details of this selector switch.
Please refer to the Technical Manual and its supplemental manual (GD-031) “Technical Information
For The Gullco “GSP” Micro-Processor Based, 24 Volt DC Motor Control” (the pages are numbered
with a prefix of “T-“), for additional, more comprehensive details than those provided in the following
overview.
GSP CONTROL TECHNICAL INFORMATION
The GSP-2010-10 microprocessor based motor control is a 24 vdc, full “H”-Bridge, pulse width
modulation control with regenerative braking. Inside the chassis of the SAM
®
carriage is a power
supply which converts the 42/115/230 VAC from the power source to a 30 to 38 vdc supply.
These controls can either operate with or without a closed loop tach feed back system attached to
the armature of the motor. A tach feed back is normally recommended as it allows the motor
control to constantly monitor and correct the speed of the motor providing accurate speed control
regardless of any variance in loading. Open loop (i.e. no tach feed back) may be acceptable for
manual motor operation in situations where; the motor sensor is awaiting replacement; the motor
sensor is susceptible to failure due to an exceptionally harsh environment; or where accurate
calibrated speed is not required and the loading of the motor is constant.
Various input and output ports are provided which are either optically coupled or transistor outputs.
The ports that are applicable to this version of the control are described in detail later in this
manual.
Important Notes:
The motor control must not be continually started and stopped by the removal and reapplying of
power to the control. Turning the power off to the control will not provide regenerative braking and
continued use will damage the control.
Allow ten (10) seconds after the removal of power before reapplying the power to the "GSP" control.
The “Current Limit” (motor overload protection) on this product is typically factory preset to 8 Amps
(unless specifically requested at time of order). If a specific application requires that this be