Inspection and installation – Groth 3011L User Manual
Page 6
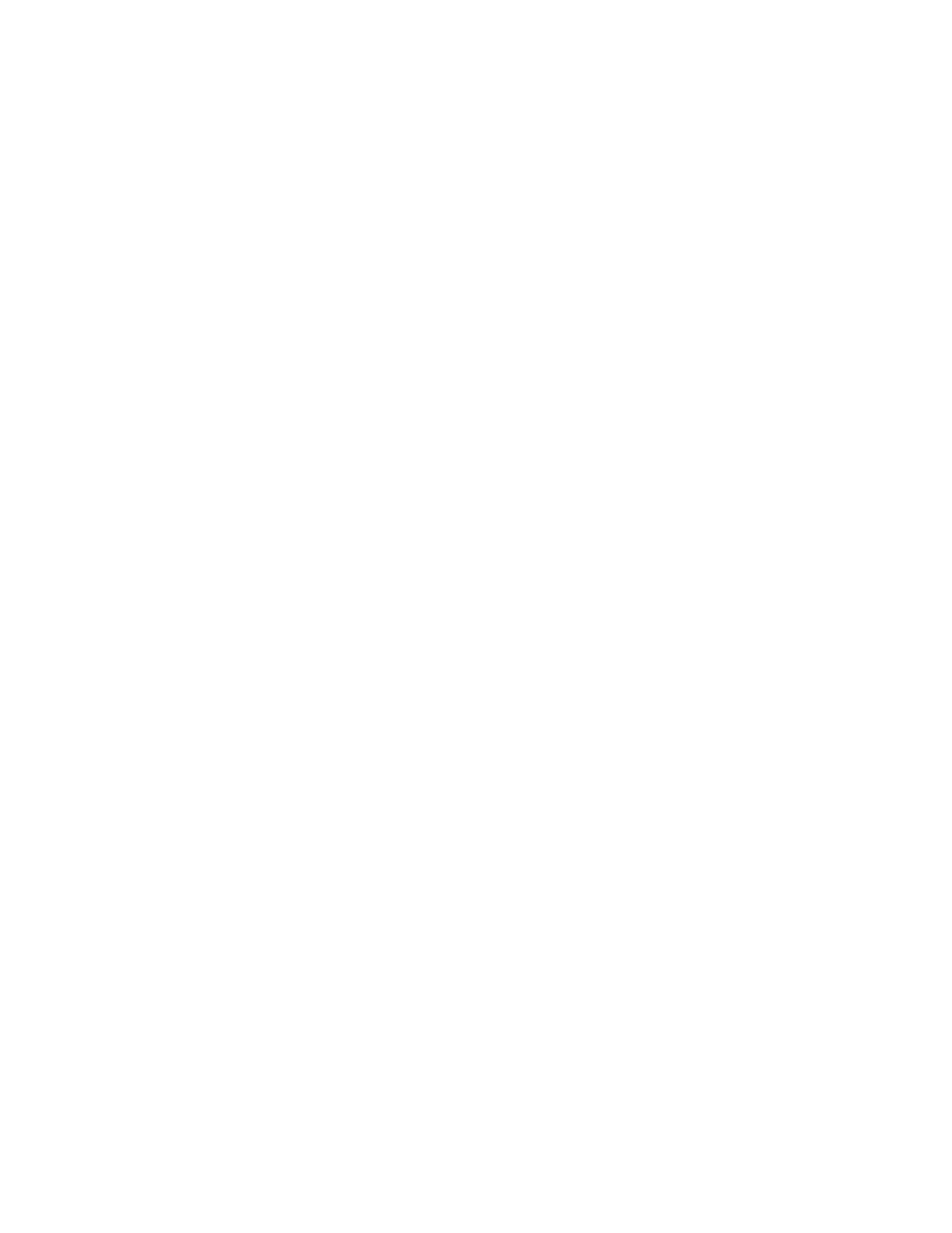
5
INSPECTION AND INSTALLATION
The regulator is packaged and supported to prevent damage or contamination in shipping. It should be similarly protected during
subsequent handling and storage. Always keep all ports plugged to prevent intrusion of foreign materials. Before installation,
visually inspect the unit. If there are indications of physical damage or internal contamination, the regulator must be disassembled,
cleaned and inspected before installation. If factory set, the spring adjustment cap and the orifice selector locking screw must be
secure. Report any shipping damage to your carrier.
If the regulator is stored in an uncontrolled environment, some condensation may accumulate in the actuator housing due to
temperature fluctuations. Invert the regulator and drain all condensation through the vents.
The available regulator inlet and outlet connections are 1/2" NPT (F), 1/2" 150# RF ANSI, Quick Disconnect Fittings, or 1" sanitary
fitting for the 1/2" size and 1" NPT (F) or 1" 150# RF ANSI flange for the 1" size. The regulator must be installed leveled. The
direction of the flow is marked on the body. It is to be installed in accordance with accepted piping practices. Full bore block
valves should be installed upstream and downstream of the regulator and in the sense line to allow it to be removed from the
system for maintenance.
Blanket Gas Regulator flow capacity is based on a known supply pressure at the regulator inlet port, and choked flow (discharge
piping pressure drop less than half of the supply pressure). Consult factory for capacity data if supply and/or discharge piping do
not meet these criteria.
The regulator is to be connected to the tank or vessel with a minimum 0.31" ID tubing sense line. This line must be kept open and
unobstructed to ensure that the regulator "senses" the actual tank pressure. Long sense lines may require a larger diameter and
care must be taken to assure that the line is self-draining. For some applications, a nitrogen purge may be required to ensure that
this line remains open. Consult the factory for recommendations for remote installations or vapors that may cause line
obstructions.