Inspection and installation – Groth 2000A User Manual
Page 5
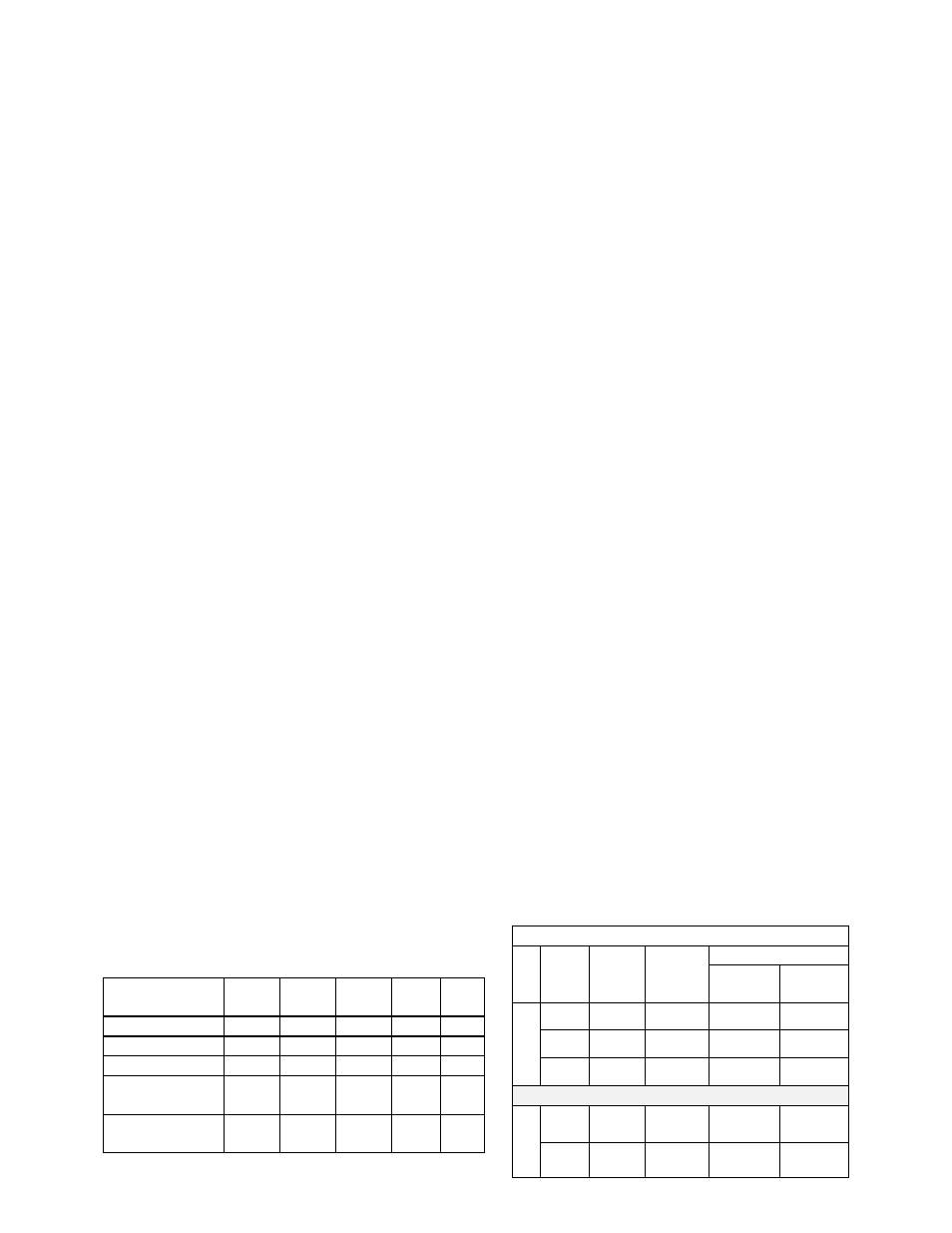
5
INSPECTION AND INSTALLATION
The ERV is packed and supported to prevent damage or contamination during shipping. It should be similarly
protected during subsequent handling and storage. Before installation inspect the unit visually. If there are
indications of physical damage or internal contamination, the valve must be disassembled, cleaned and inspected
before installation.
Inspect the valve for any sign of damage that may have occurred in shipment and report this to the carrier. The seat
protector (rubber strip placed over the valve seat) shall be removed before placing the valve into service.
Handles/Eye Nuts are provided on the upper weight plates for handling the pallet assembly. The body has three
lifting eyes that are used to lift and position the body. To avoid damage to the lower flange surface, set the valve on a
soft clean gasket material until it is ready to be installed. It should be stored in a clean environment until it is to be
mounted on the tank.
The 2000A Series Emergency Relief Valve is a device that must be handled carefully to ensure seat tightness. The
body is manufactured from thin steel plate material and can be damaged by over-tightening the studs or mounting on
a tank nozzle that is not flat. The valve is also equipped with a grounding strap that should be grounded properly to
prevent static electric discharge.
The standard bodies are furnished with flat flanges; the valve should be mounted on a flat faced 150# ANSI or API
650 flange. It is recommended to use a full faced gasket to avoid deflecting the body flange. The connecting flanges
must be flat within 0.015" and clean, free of scratches, corrosion and tool marks.
All valves should be installed using the three body lifting lugs. Mount the valve with the pallet assembly in the
horizontal plane.
1. Begin by inspecting the gasket; make sure that the material is suitable for the service. Gasket dimensions are
listed in Table 2 below:
2. Lubricate all studs and nuts with an appropriate thread lubricant. If stainless steel fasteners are used, select an
anti-seize lubricant such as moly-disulfide.
3. Align the gasket with the bolt circle.
4. Set the valve body carefully on the nozzle; keep the gasket between the flanges. Install the studs and tighten
nuts hand tight.
5. Torque all fasteners to half the recommended value (see Table 3) in a staggered, alternating pattern or follow
appropriate plant maintenance guidelines and standards.
*Note: Torque values are based on a gasket factor m=3.5,
gasket factor y=2000 psi, maximum pressure = 2 psi.
6. Make sure that the flanges are not distorted and that the gasket is evenly compressed.
7. Make up the final torque and check that no further nut rotation occurs.
8. For Model 2000A and Model 2050A, the cover assembly may be independently lifted into position by using the
handles/eye nuts supplied for the weight plates. Align the pallet assembly peripheral guides with the body bore
and carefully lower the cover assembly until it seats against the body.
Table 3: Recommended Torque Values*
Size
Qty
Holes
Bolt
(in)
(UNC)
Torque (ft-lbs)
Raised
Face
Flange
Face
150 ANSI
16” 16 1.000 52
104
20” 20 1.125 63
110
24” 20 1.250 86
148
API650
20” 20 0.625 35
53
24” 20 0.625 43
61
Table 2: Body Flange Gasket Dimensions
Type Flange
O.D.
(in)
I.D.
(in)
B.C.
(in)
Hole
(in)
Qty.
FF 16" – 150 #
23.50
15.25
21.25
1.13
16
FF 20" – 150 #
27.50
19.25
25.00
1.25
20
FF 24" – 150 #
32.00
23.25
29.50
1.38
20
FF 20” – API
650
26.00 19.25 23.50 .75 16
FF 24” – API
650
30.00 23.25 27.50 .75 20