Start-up - direct gas, Check the supply gas pressure, Important – Greenheck DG / DGX with Direct Spark (470652) User Manual
Page 16: Set the burner air pressure differential, Burner and baffles, Measuring the pressure drop, Direct gas nameplate
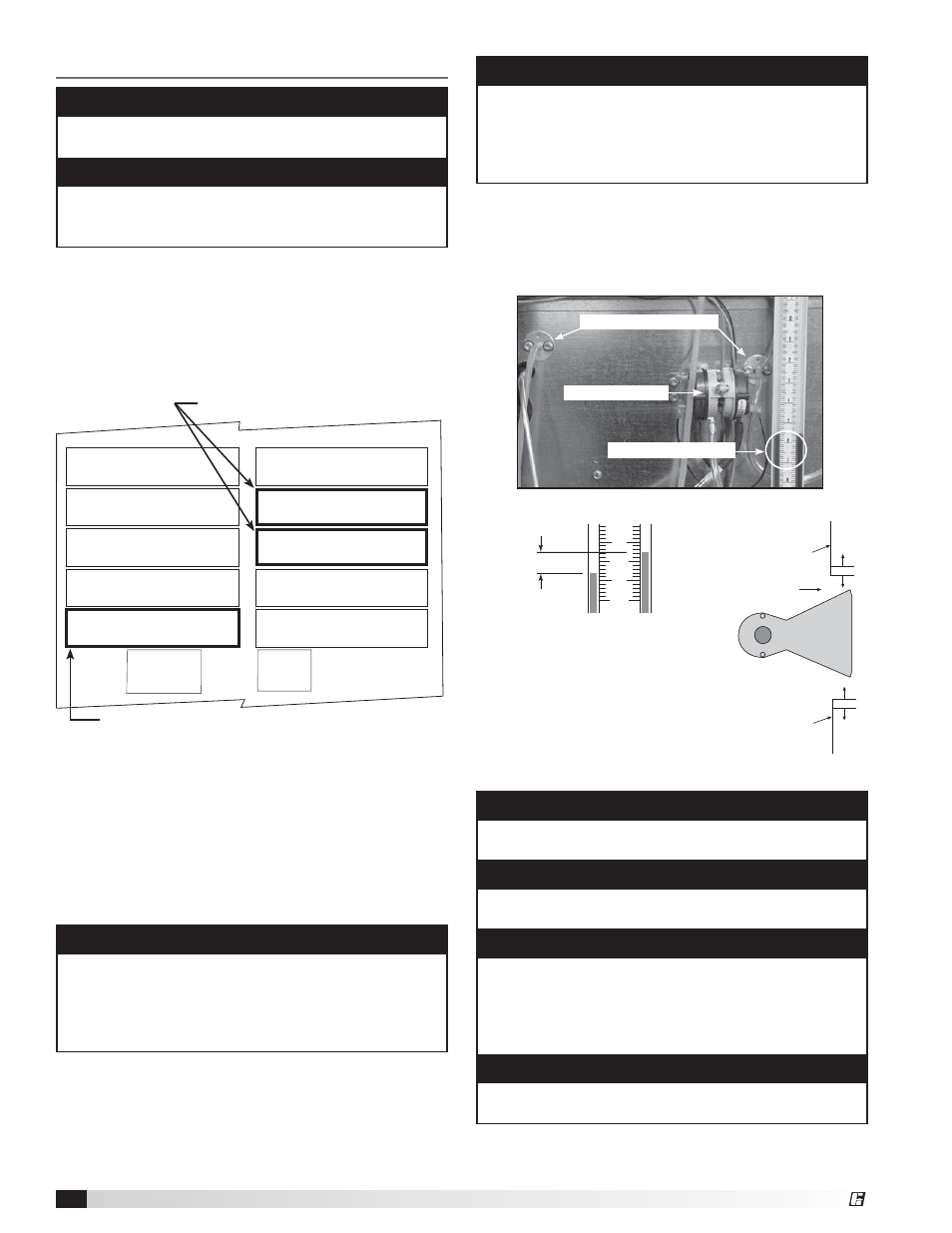
Direct Spark Ignition Make-Up Air
16
®
1. Check the Supply Gas Pressure
Check the supply gas pressure and compare it with
the unit’s nameplate pressure requirements. Adjust
the supply regulator as needed until the supply gas
pressure is within the specified range (see below). The
nameplate is located on the outside of the unit on the
control panel side.
Start-Up - Direct Gas
IMPORTANT
For proper unit function and safety, follow the start-up
procedure in the exact order that it is presented.
IMPORTANT
This start-up should begin after all of the installation
procedures and the blower start-up have been
completed.
IMPORTANT
The purpose of the high and low gas pressure
switches is to automatically shut down the burner
if the inlet gas pressure is too low for the burner to
safely light, or if the manifold pressure is too high for
the burner to operate properly.
3. Set the Burner Air Pressure Differential
With all access panels in place, the fan running
and discharging 70ºF (21ºC) air, connect a U-Tube
manometer to the outer sensing probes (see below) and
measure the static pressure across the burner.
IMPORTANT
Proper air velocity over the burner is critical on direct
fired gas units. If the air velocity is not within the unit
specifications, the unit will not operate efficiently,
may have sporadic shutdowns, and may produce
excessive carbon monoxide (CO) or other gases.
NOTE
The pressure drop was set at the factory and may not
need adjustment.
NOTE
When required pressure is obtained, be sure to
reconnect the outer sensing probes.
IMPORTANT
This process may need to be repeated until the proper
pressure is achieved. This adjustment will change the
air quantity delivered by the unit and therefore the air
quantity delivered should be rechecked. Refer to the
Blower Start-Up section.
NOTE
To increase the static pressure decrease the opening.
To decrease the static pressure increase the opening.
2. Check the Optional High and Low Gas
Pressure Switches
The high pressure setting is typically 8 in. wg (2 kPa)
and the low pressure is setting is typically 3 in. wg (0.7
kPa). The switches are set at the factory and should not
need adjustment. Adjust the setting only if needed. See
the Gas Train Layout diagram in the Reference section
for the high and low pressure switch location.
The proper static pressure should
be between 0.625 and 0.675 inches
wg (155.68 and 168.64 Pa). If
needed, evenly adjust the baffles
above and below the burner,
keeping the burner centered in the
opening until the required pressure
is obtained.
Adjustable
Top Baffle
Airflow
Burner
Adjustable
Bottom Baffle
Burner and Baffles
7
6
0.625 - 0.675 in. wc
Measuring the Pressure Drop
Outer Sensing Probes
U-Tube Manometer
Pressure Switch
Direct Gas Nameplate
“ W.C.
“ W.C.
“ W.C.
F
PSI
“ W.C.
“ W.C.
MAX BTU/HR
BTU/H MAX
NORMAL MANIFOLD
PRESSURE
PRESSION DÕADMISSION
NORMALE
MIN GAS
PRESSURE
PRESSION DE GAZ
MIN BURNER
PRESSURE DROP
PERTE MIN DE PRESSION
DANS LE BRULEUR
TYPE OF GAS
NATURE DU GAZ
MIN BTU/HR
BTU/H MIN
MIN GAS PRESSURE
FOR MAX OUTPUT
PRESSION DE GAZ MIN
POUR PUISSANCE MAX
MAX BURNER
PRESSURE DROP
PERTE MAX DE PRESSION
DANS LE BRULEUR
MAX GAS
PRESSURE
PRESSION DE GAZ
MAX
DESIGN ΔT
ΔT NORMALE
EQUIPPED FOR
CONCU POUR
SCFM
“ W.C.
EXTERNAL STATIC PRESSURE
PRESSION STATIQUE EXTERIEURE
AGAINST
CONTE
Minimum and maximum gas
pressures for maximum output
Type of gas