Flowserve MN User Manual
Page 39
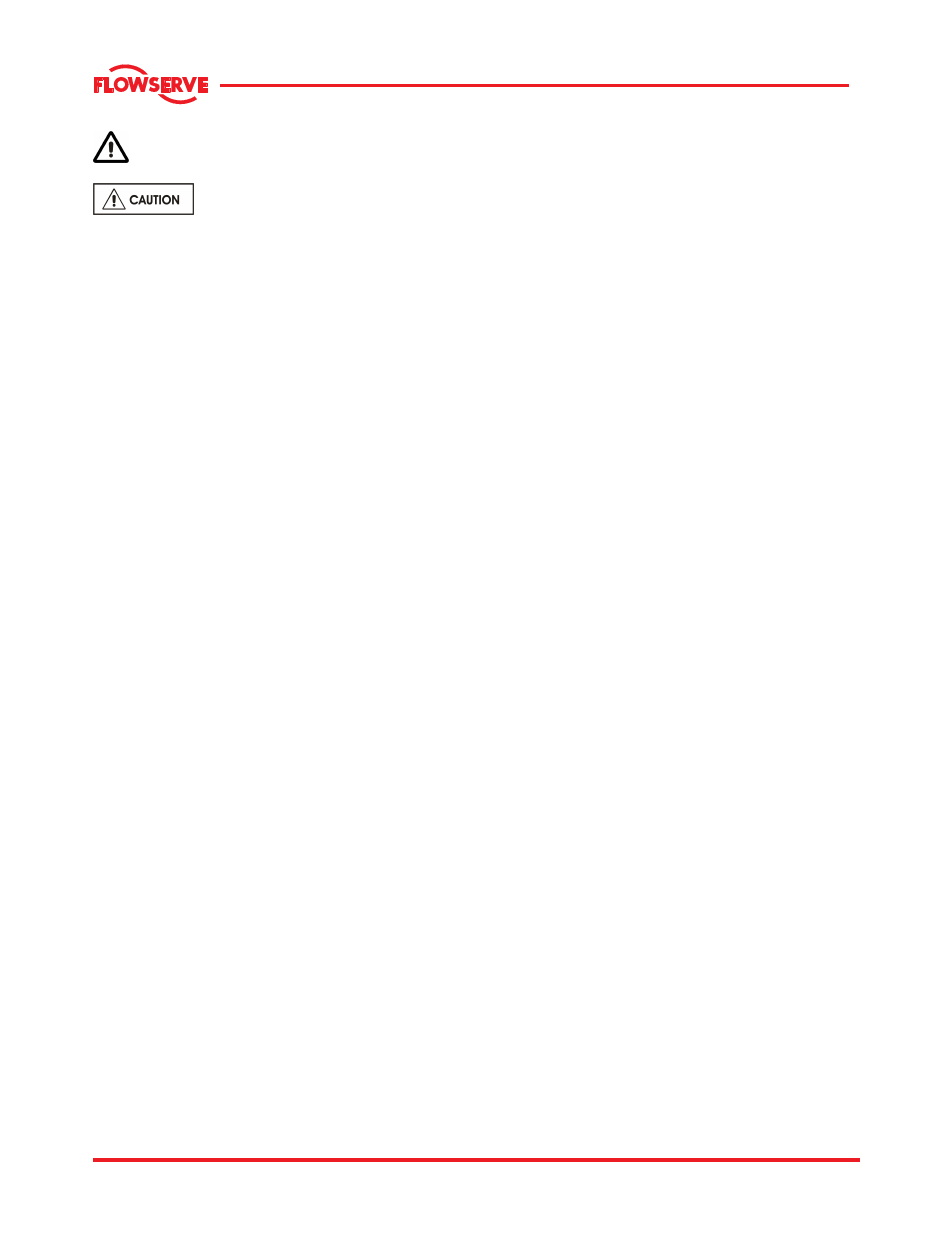
MN USER INSTRUCTIONS ENGLISH 71569189 11/04
Page 39 of 49
®
6.7 Disassembly
Refer to section 1.6,
Safety
, before dismantling
the pump.
Before dismantling the pump for
overhaul, ensure genuine Flowserve replacement
parts are available.
Refer to sectional drawings for part numbers and
identification.
6.7.1 Preliminary to dismantling
a) Isolate motor and lock off electrical supply in
accordance with local regulations.
b) Isolate suction and discharge valves.
c) Remove coupling guards and disconnect the
coupling halves.
d) Drain pump casing. Remove any auxiliary piping
if applicable.
e) For convenience at re-assembly, lay out all parts
in the order in which they are removed.
f) Protect all machined faces against metal-to-metal
contact and corrosion.
g) Proceed as follows referencing the pump
Sectional Drawing provided in Section 8.
6.7.2 Pump dismantling procedure
a) Disconnect the coupling halves and the bearing
frame support [53]. Unbolt and rotate the motor
to allow removal of the pump rotor assembly
[2+11+99+6 assemblies].
b) Unbolt the stuffing box head [11] from the casing
[1].
c) Draw out the rotating assembly complete with the
stuffing box head[11],bearing housing [99],
impeller [9], shaft [6] and all attached parts and
sub assemblies. Exercise care in slinging and
handling the unit.
d) Remove the impeller nut set screw and the
impeller nut [24]. The setscrew was mounted
using Loctite 271 or equivalent and may require
heating to 200
o
C (400
o
F) for removal. A
standard square bar will fit the square hole
provided in the impeller nut.
e) Pull the impeller [2] and the impeller key. Leave
the impeller-wearing ring as is on the impeller.
f) Remove the packing gland [17]. If the pump is
equipped with a mechanical seal unbolt the seal
from the gland.
g) Unbolt and remove the bearing frame [99] from
stuffing box head [11]. The packing [13] and seal
cage halves [29] may be removed at this time.
Remove the mechanical seal if so equipped.
h) Remove the shaft sleeve [14] only if necessary;
see Maintenance of Shaft and Shaft Sleeve.
i) Remove pump coupling half. Do not hammer to
remove.
j) Remove the upper and lower outside seal rings
[40, 40A].
k) Remove the upper and lower bearing housing
covers [35, 37] with their respective seals. If a
bent shaft is suspected, the shaft should be
checked for runout at this time. The maximum
permissible runout is 0.050 mm (0.002 in.)
TIR at
the bearing, coupling, sleeve, and impeller turns.
l) Disengage the thrust bearing lock washer tab
from its locknut [22]. Unscrew the thrust-bearing
locknut [22] and remove the lock washer [22A]
and bearing washer [22B].
m) Remove the shaft [6] toward the impeller end.
The thrust bearing will be pushed off of the shaft
by this movement.
n) Carefully examine all individual parts, important
joints, and all wearing surfaces as the pump and
rotor are dismantled. As a general rule,
regardless of the performance of the unit,
bearings and parts appreciably worn should be
renewed if it is not intended to examine the pump
again until the next overhaul period.
6.7.3 Bearing installation and removal
Anti-friction bearing cones (inner race) are usually
pressed or shrunk onto the shaft. The cups (outer
races) are usually pressed or shrunk into the bearing
housing. When mounting bearings it is important that
the proper fit is maintained.
When a pulling device is used to remove bearings
from the shaft, the pulling jaws or fingers should be
located on the bearing cone. When other parts do
not interfere, the bearing cone may be supported by
a split ring and the shaft pressed out using an arbor
press. The bearing cups can similarly be pulled out
of the housing.
There are two methods for mounting a bearing on the
pump shaft:
a) Heating the bearing to expand the cone and
shrinking it on the shaft.
b) Pressing the bearing onto the shaft.
The method (a) is preferred over the method (b).
Heat the bearing in an oil bath or electric oven to a
uniform temperature of 120
o
C (250
o
F). When
heated, quickly mount it on the shaft. If the alternate
method is used, apply force by means of an arbor
press; see detail below.