Flowserve MN User Manual
Page 29
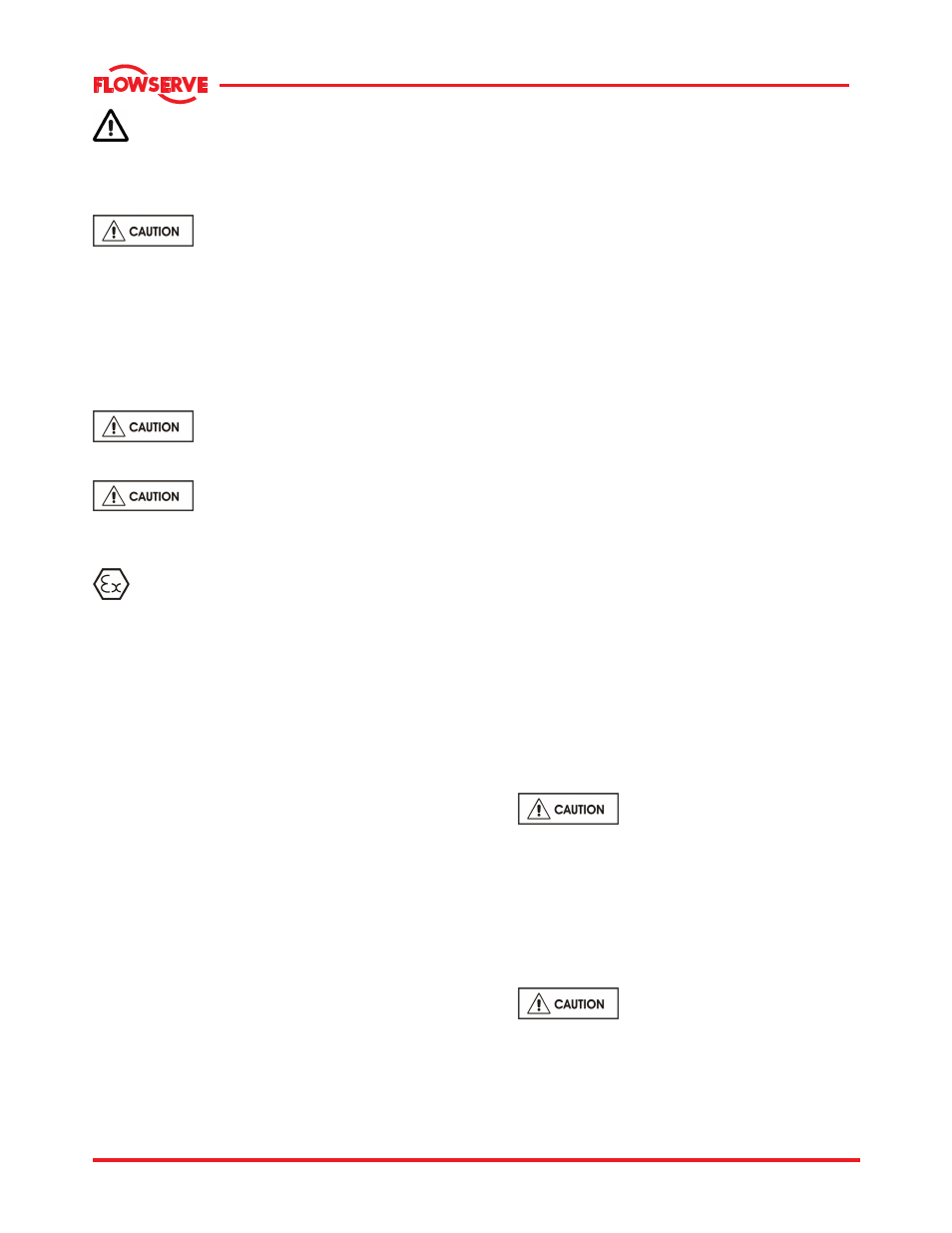
MN USER INSTRUCTIONS ENGLISH 71569189 11/04
Page 29 of 49
®
Care must be taken when adjusting the gland
on an operating pump. Safety gloves are essential.
Loose clothing must not be worn to avoid being
caught up by the pump shaft. Shaft guards must be
replaced after the gland adjustment is complete.
Never run gland packing dry, even for
a short time.
5.8.3 Pumps fitted with mechanical seal
Mechanical seals require no adjustment. Any slight
initial leakage will stop when the seal is run in.
Before pumping dirty liquids it is advisable, if
possible, to run in the pump mechanical seal using
clean liquid to safeguard the seal face.
External flush or quench should be
started before the pump is run and allowed to flow for
a period after the pump has stopped.
Never run a mechanical seal dry,
even for a short time.
5.8.4 Pump and motor bearings temperature
If the pumps are working in a potentially
explosive atmosphere, temperature or vibration
monitoring at the bearings is recommended.
If bearing temperatures are to be monitored it is
essential that a benchmark temperature is recorded
at the commissioning stage and after the bearing
temperature has stabilized.
•
Record the bearing temperature (t) and the
ambient temperature (ta)
•
Estimate the likely maximum ambient
temperature (tb)
•
Set the alarm at (t+tb-ta+5)
°
C [(t+tb-ta+10)
°
F]
and the trip at 100
°
C (212
°
F) for oil lubrication
and 105
°
C (220
°
F) for grease lubrication
It is important, particularly with grease lubrication, to
keep a check on bearing temperatures. After start up
the temperature rise should be gradual, reaching a
maximum after approximately 1.5 to 2 hours. This
temperature rise should then remain constant or
marginally reduce with time.
5.8.5 Reduced Capacity operation
Generally, Flowserve non-clog pumps are designed
for continuous operation above 65% of the peak
efficiency capacity at maximum RPM and impeller
diameter. They are suitable for occasional or
intermittent operation at capacities outside these
limits, however, pump operation may be noisy and
component life may be reduced.
These limitations are placed because the impellers
have wide discharges and at other capacities high
magnitudes of radial reactions are encountered and
flow re-circulation may occur. This is an inherent
design characteristic for a pump of this type.
In many cases, particularly in sewage pumping
applications, reduced capacities are met by a
reduction in pump speed and no throttling is used.
Under these circumstances, these part capacity
applications are not nearly so critical because of
lower pump speed and relatively lower pump
operating heads. Refer application requirements with
pump operation at other capacities to your nearest
Flowserve representative.
5.8.6 Suction lift
Sometimes the suction conditions imposed upon a
centrifugal pump are extremely unfavorable and lead
to a complete breakdown of the pump operation.
The suction lift must be kept within the suction
limitations for which the pump was sold. If the
original operating conditions must be changed for
any reason, consult your nearest Flowserve Sales
Representative.
Care should also be exercised to keep the suction
piping air tight and sealed against leakage.
5.9 Stopping and shutdown
a)
Close the outlet valve, but ensure
that the pump runs in this condition for no more
than a few seconds.
b) Shut down the driver according to driver
manufacturer’s instruction.
c) For pumps operating under positive suction
head, after stopping the pump, continue injecting
water into the stuffing box to avoid the entrance
of contaminants into the stuffing box sealing
area, if required
d)
Do not tighten the gland to stop
liquid leaking out or air leaking into the stuffing
box
e) If wearing rings are provided with a flushing
provision, turn off liquid to the rings several
minutes after the pump is stopped.