Flowserve MN User Manual
Page 32
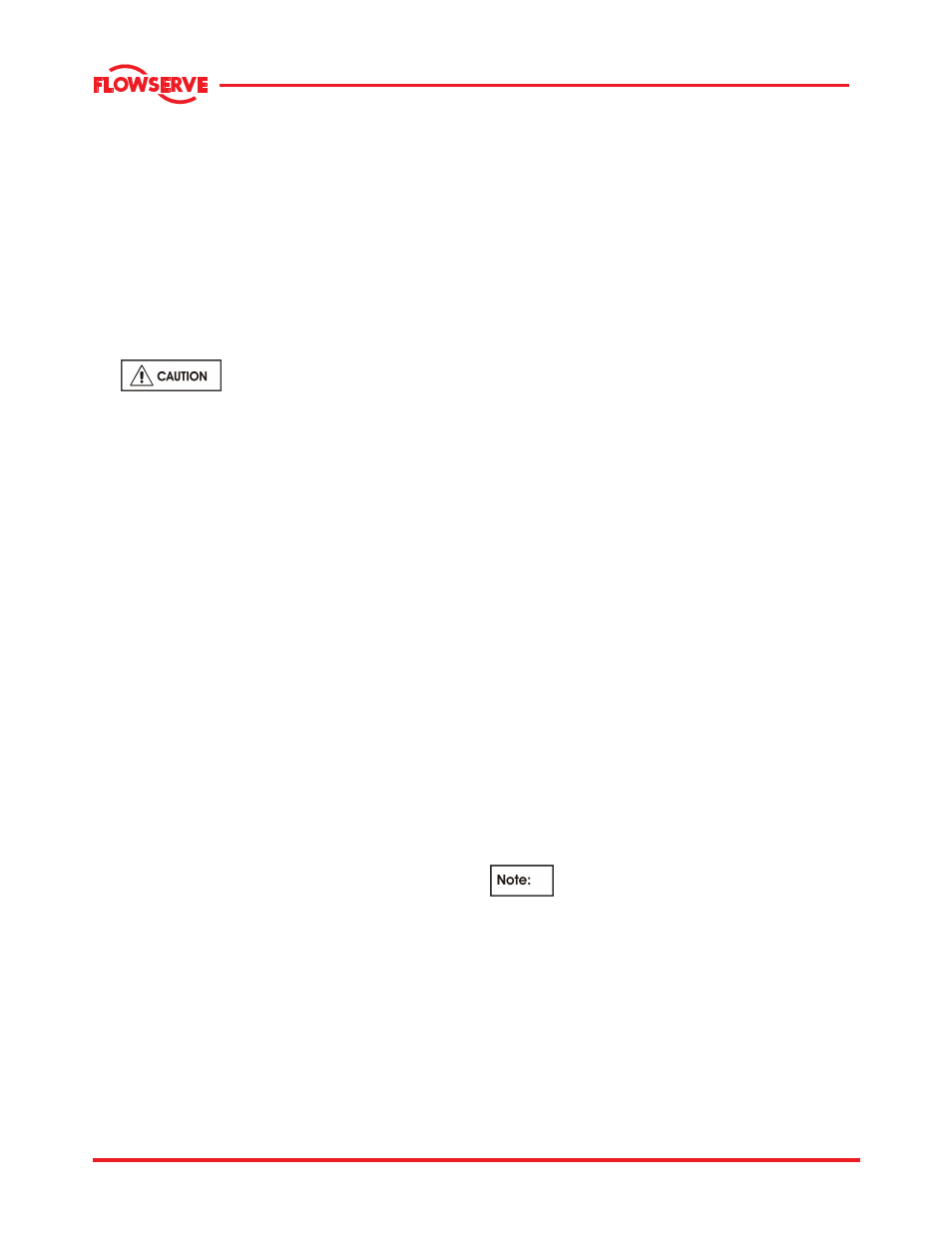
MN USER INSTRUCTIONS ENGLISH 71569189 11/04
Page 32 of 49
®
6.1.2 Periodic inspection (semi-annual)
Check the stuffing box for free movement of the
gland. Clean and oil the gland studs and nuts.
Closely observe the stuffing box for excessive
leakage which cannot be reduced by gland
adjustment, and replace the packing as necessary.
Check the pump running records for hourly usage to
determine if the bearings should be inspected and re-
lubricated. The maximum recommended time
between cleaning and lubrication change is one year,
regardless of usage. The severity of the environment
and conditions of service may dictate shorter
frequency.
a)
Check foundation bolts for
security of attachment and corrosion.
b) Check pump running records for hourly usage to
determine if bearing lubricant requires changing.
c) The coupling should be checked for correct
alignment and worn driving elements.
Refer to the manuals of any associated
equipment for periodic checks needed.
6.1.3 Complete overhauls
Frequency of a complete overhaul depends upon the
hours of pump operation, the severity of the
conditions of service, the materials used in the pump
construction, and the care the pump receives in
operation.
Do not open the pump for inspection unless there is
definite evidence that the capacity has fallen off
excessively or unless there is indication of trouble
inside the pump or in the bearings.
6.1.4 Complete cleaning during a major overhaul
If the bearings need cleaning, or if an overhaul period
offers the opportunity, the lubricant cavities and
bearings should be cleaned.
After the pump has been dismantled, use a brush
and wash out the housing with hot oil, 95 to
115
o
C (200 to 240
o
F), or non-toxic solvent. Flush
the housing with a light mineral oil to prevent rust and
to remove all traces of solvent.
Using a brush dipped in hot oil, 80 to 95
o
C (180 to
200
o
F ), remove any solid particles while gently
spinning the bearing. If badly oxidized grease is
present and refuses to come off with the above
procedure, the bearings should be immersed in a hot
non-toxic solvent and allowed to soak. Brush and
spin the bearings until the oxidized grease is
removed.
Difficult spots can sometimes be removed with a
mixture of alcohol and light mineral solvent. Flush
the bearings with clean, light oil to remove any
contaminated oil.
6.1.5 Maintenance of casings
The casing waterways must be kept clean and clear.
Whenever a unit has been dismantled, clean the
waterways of the casing. These pumps have two
casing gaskets that may be damaged when the pump
is opened. One gasket is between the stuffing box
head and the casing, and the other is between the
suction head and the casing.
New casing gaskets must be the same thickness and
material as the original to achieve the same
compressed thickness. Gaskets originally installed
were Aramid fiber with SBR rubber. When installing
a new gasket proceed as follows
:
a) Clean the flanges. Dirt and scale provide
leakage paths.
b) Lubricate the fastener threads and mounting
face. Threads should be well formed and free
running.
c) Trim the gasket edges squarely and neatly and
coat the gasket with a suitable release agent.
d) Place the gasket on the flat surface of the flange
and assemble the flange joints and run up all the
fasteners finger tight. Develop final torque using
"Recommended Torques for Threaded
Fasteners" at the end of this section, in about
three equal steps by cross-tightening evenly.
6.1.6 Maintenance of wearing rings
Generally, the rings should be renewed or
overhauled when the pump performance has
decreased appreciably due to excessive wearing ring
clearance. The original nominal design running
clearance was 0.51 to 0.76 mm (0.020 to 0.030 in.)
axially.
Pumps equipped with mechanical seals
may require rotor removal and resetting of the seal
after adjusting the wearing ring gap. Refer to
mechanical seal manufacturer's User Instructions.