Flowserve MN User Manual
Page 15
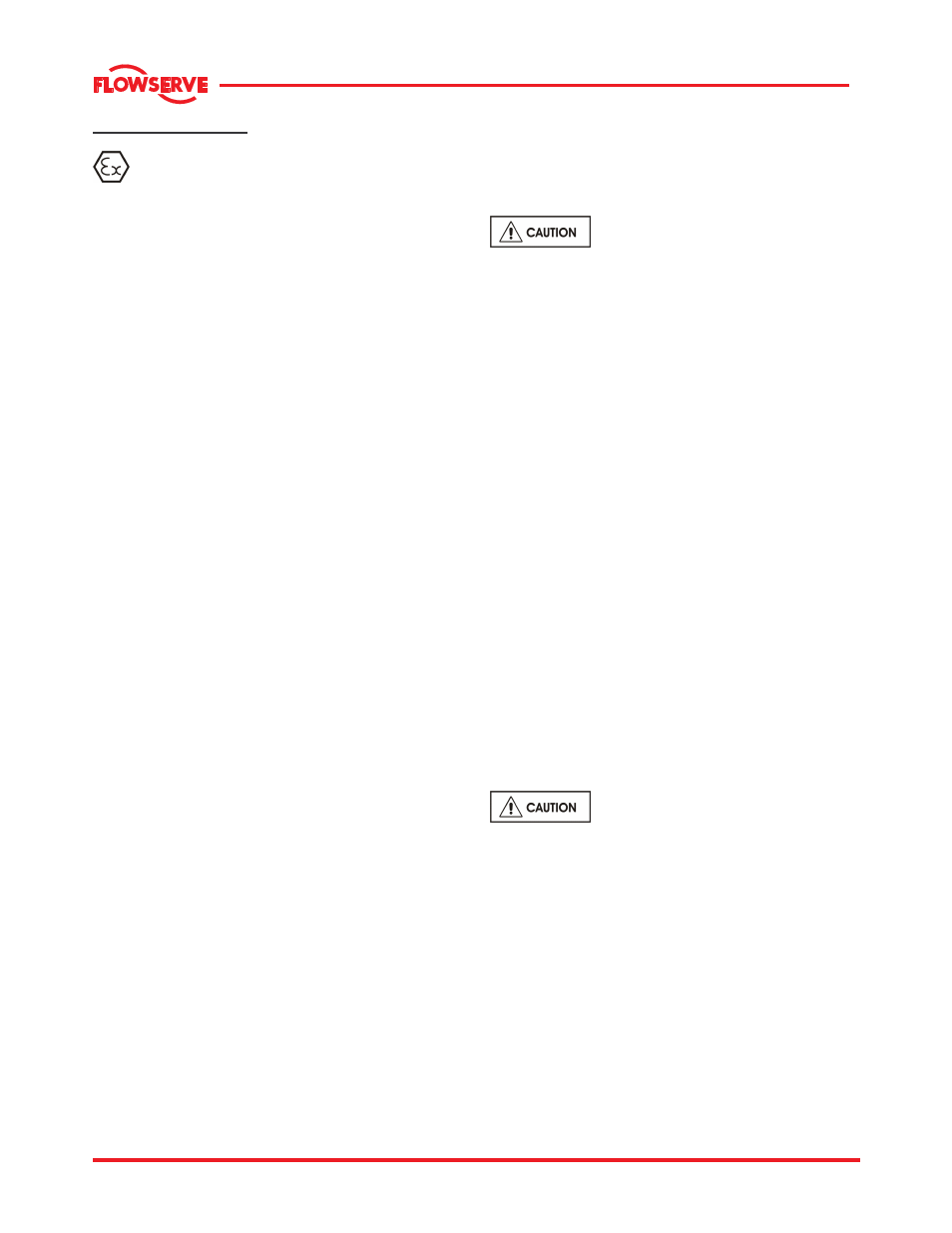
MN USER INSTRUCTIONS ENGLISH 71569189 11/04
Page 15 of 49
®
4 INSTALLATION
Equipment operated in hazardous locations
must comply with the relevant explosion protection
regulations. See section 1.6.4,
Products used in
potentially explosive atmospheres.
Inspection prior to installation:
Six months prior to
the scheduled installation date, a Flowserve Pump
Division representative is to be employed to conduct
an inspection of the equipment and the facility. If any
deterioration of equipment is noticed, the Flowserve
Pump Division representative may require a partial or
complete dismantling of the equipment including
restoration and replacement of some components.
4.1 Location
The pump should be placed so as to allow room for
access, ventilation, maintenance and inspection with
ample headroom for lifting and should be as close as
practicable to the supply of liquid to be pumped.
4.1.1 General installation check-list
The following checks should be made before starting
actual installation.
a) Make sure that the motor nameplate ratings and
the power supply system match correctly.
b) Check the sump depth and suction pipe length
match up.
c) Check the liquid level in the sump.
d) Check the installation equipment to be sure that it
will safely handle the pump weight and size.
e) Check all pump connections (bolts, nuts etc) for
any shipping and handling related problems.
f) Check for any evidence of lubricant leakage at
the bearings.
g) Check that the shaft rotates freely.
4.1.2 Cleaning prior to installation
Remove the rust inhibitor, flange protectors, plastic
covers, desiccant, and inspect the inside of the
pump. Repack the stuffing box and ensure that the
stuffing box drain is clear. Flush the bearings using a
hot, light oil at 82
o
to 93
o
C (180
o
to 200
o
F) while the
shaft is slowly rotated. Re-lubricate the bearings as
explained in Section 5.0
4.1.3 Manufacturer’s service
It is recommended that the services of Flowserve
Company Service Representative be employed for
installing and starting the pump as proper installation
is vital for designed functioning, performance and
reliability of the equipment.
4.1.4 Site preparation
Care should be taken to prevent an out of service
pump from freezing during cold weather. Draining
the pump is recommended when there is any
possibility of freezing.
Observe extreme caution when
priming, venting and draining hazardous liquids.
Wear protective clothing in the presence of
hazardous, caustic, volatile, flammable and hot
liquids. Do not breathe toxic vapors. Do not
swallow. Do not allow sparking, flames or hot
surfaces in the vicinity of the equipment.
4.1.5 General tools required for installation
a) Mobile crane capable of hoisting and lowering the
pump and/or motor.
b) Sets of chains, tongs and cable slings for
attaching it to the pump and motor lifting eyes.
c) General purpose hand tools, pipe wrenches, end
wrenches, socket set, screwdrivers, Allen
wrenches, wire brush, scraper and fine emery
cloth.
d) Thread sealing compound designed for stainless
steel and light machinery oil.
4.2 Part assemblies
Motors may be supplied separately for some of the
larger models of MN pumps. It is the responsibility of
the installer to ensure that the motor is assembled to
the pump and lined up as detailed in section 4.5. It is
also the responsibility of the installer to take note of
the pump and driver weights for proper handling
before assembly is attempted.
4.3 Foundation
There are many methods of installing
pump units to their foundations. The correct method
depends on the size of the pump unit, its location and
limitations on its noise/vibrations. Non-compliance
with the provision of correct foundation and
installation may lead to failure of the pump and, as
such, would be outside the terms of the warranty.
The foundation may consist of material that will afford
permanent, rigid support to the discharge head and
will absorb expected stresses that may be
encountered in service.
Concrete foundations should have anchor bolts
installed in sleeves that are twice the diameter of the
bolt to allow alignment and has holes in the mounting
plate as illustrated in the detail below.