8 running or operation – Flowserve MN User Manual
Page 28
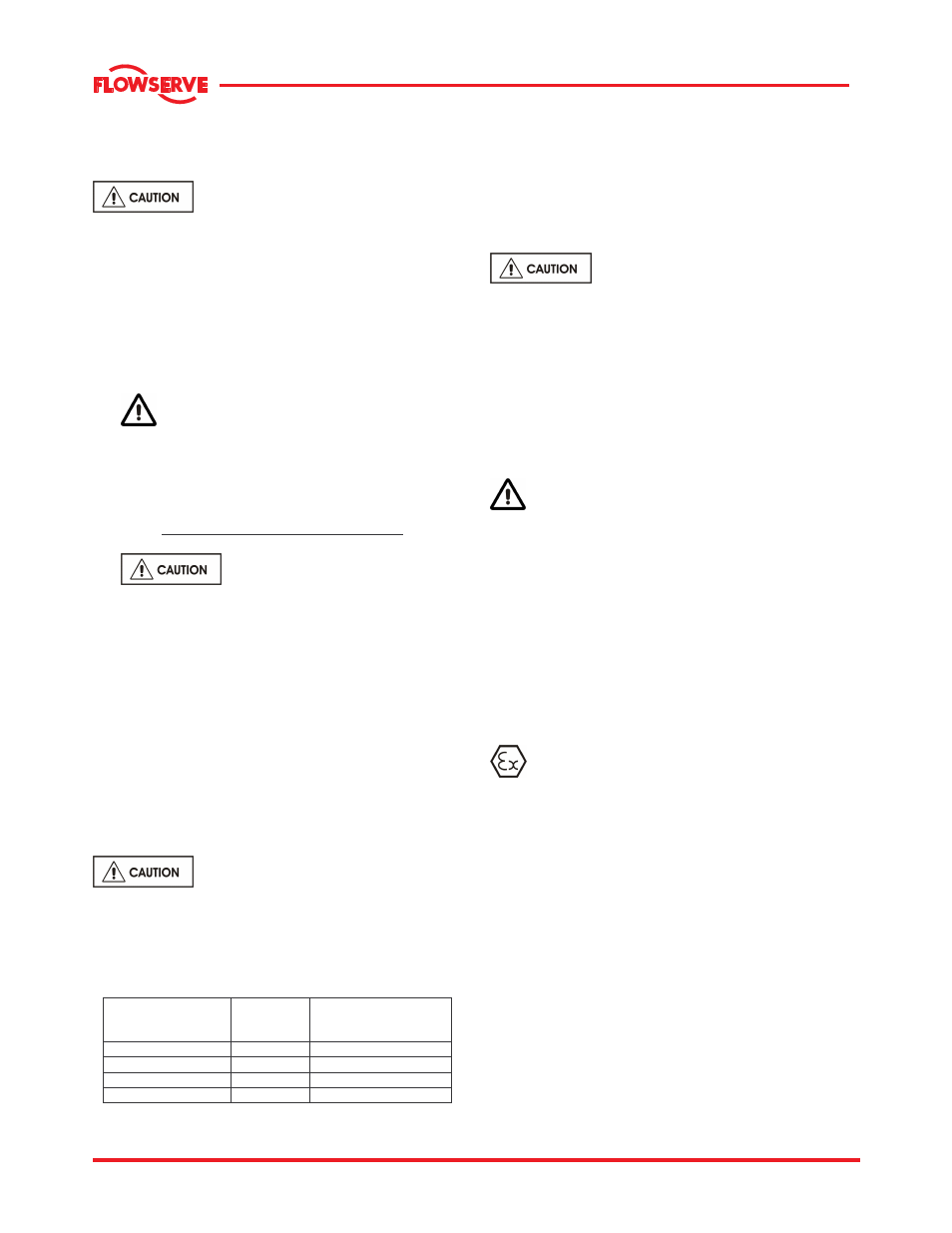
MN USER INSTRUCTIONS ENGLISH 71569189 11/04
Page 28 of 49
®
5.7.2 Pump startup
The procedure for starting the unit will vary
somewhat with each installation, however the
following steps generally apply.
Ensure flushing and/or cooling/
heating liquid supplies are turned ON before starting
the pump.
a) Turn the pump over by hand to verify that the
pump rotor turns freely. If it is bound, do not
operate the pump until the cause of the trouble is
located.
b) Make sure the suction valve is open.
c) CLOSE the outlet valve.
d) Prime the pump.
e)
Ensure all vent connections are closed
before starting.
f) Check the motor connections.
g) Start the driver per the manufacturer's instruction.
h) Open the discharge valve slowly as pressure is
built up on the discharge side of the pump. If the
valve does not open within three minutes,
shutdown the unit and determine the cause.
i)
If NO pressure, or LOW pressure,
STOP the pump. Refer to section 7,
Faults;
causes and remedies
, for fault diagnosis.
j) Adjust the gland nuts on the packing;
k) When in service, monitor oil level, bearing
temperature, suction, discharge, and stuffing box
pressure, stuffing box operation, noise, and
vibration for several hours.
5.7.3 Normal vibration levels, alarm and trip
For guidance and general data, the subject pump
types with rigid supports are classified based on
power ratings as provided within the International
Standards and recommended maximum levels below
are based on those standards.
Alarm and trip values for installed
pumps should be based on the actual measurements
(N) taken on the pump in a fully commissioned (new)
condition. Measuring vibration at regular intervals
and recording will help to track any deterioration in
pump or operating conditions.
Motor rating kW
(hp)
Vibration
velocity-
unfiltered
mm/sec (in./sec)
r.m.s
0.75-to 7.5 (1-10)
N
6.6 (0.22)
7.5 to 75 (10-100)
N
6.6 (0.22)-8.0(0.32)
75-298 (100-400)
N
8.0 (0.32)-8.6(0.34)
298-750 (400-1000)
N
8.6 (0.34)
Alarm = N X 1.25. TRIP = N X 2.0
5.7.4 Motor start/stop frequency
Even though motors are normally suitable for at least
two consecutive starts, it is recommended to restart
only after coasting to rest between starts (minimum
of 15 minutes gap is recommended) with the motor
initially at ambient temperature. If more frequent
starting is necessary, refer to driver manufacturer’s
User Instructions.
The number of motor start and stops
in any given time affects motor life.
If the motor is expected to experience multi
starts in any given time, please refer to the driver’s
user instructions before the pump is put into
operation.
5.8 Running or operation
5.8.1 Venting the pump
Vent the pump to enable all trapped air to
escape taking due care with hot or hazardous liquids.
Under normal operating conditions, after the pump
has been fully primed and vented, it should be
unnecessary to re-vent the pump. See related
information in Section 5.6.
5.8.2 Pumps fitted with packed gland
If the pump has a packed gland there must be some
leakage from the gland. Gland nuts should initially be
finger-tight only. Leakage should take place soon
after the stuffing box is pressurized.
The gland must be adjusted evenly to give
visible leakage and concentric alignment of the gland
ring to avoid excess temperature. If no leakage takes
place the packing will begin to overheat. If
overheating takes place the pump should be stopped
and allowed to cool before being re-started. When
the pump is re-started, check to ensure leakage is
taking place at the packed gland.
If hot liquids are being pumped it may be necessary
to slacken the gland nuts to achieve leakage.
The pump should be run for 30 minutes with steady
leakage and the gland nuts tightened by 10 degrees
at a time until leakage is reduced to an acceptable
level. As a thumb rule, a minimum of 30
drops/minute for every inch of sleeve diameter will
keep the gland in safe zone. Seating of the packing
may take another 30 minutes.