Flowserve VCT User Manual
Page 5
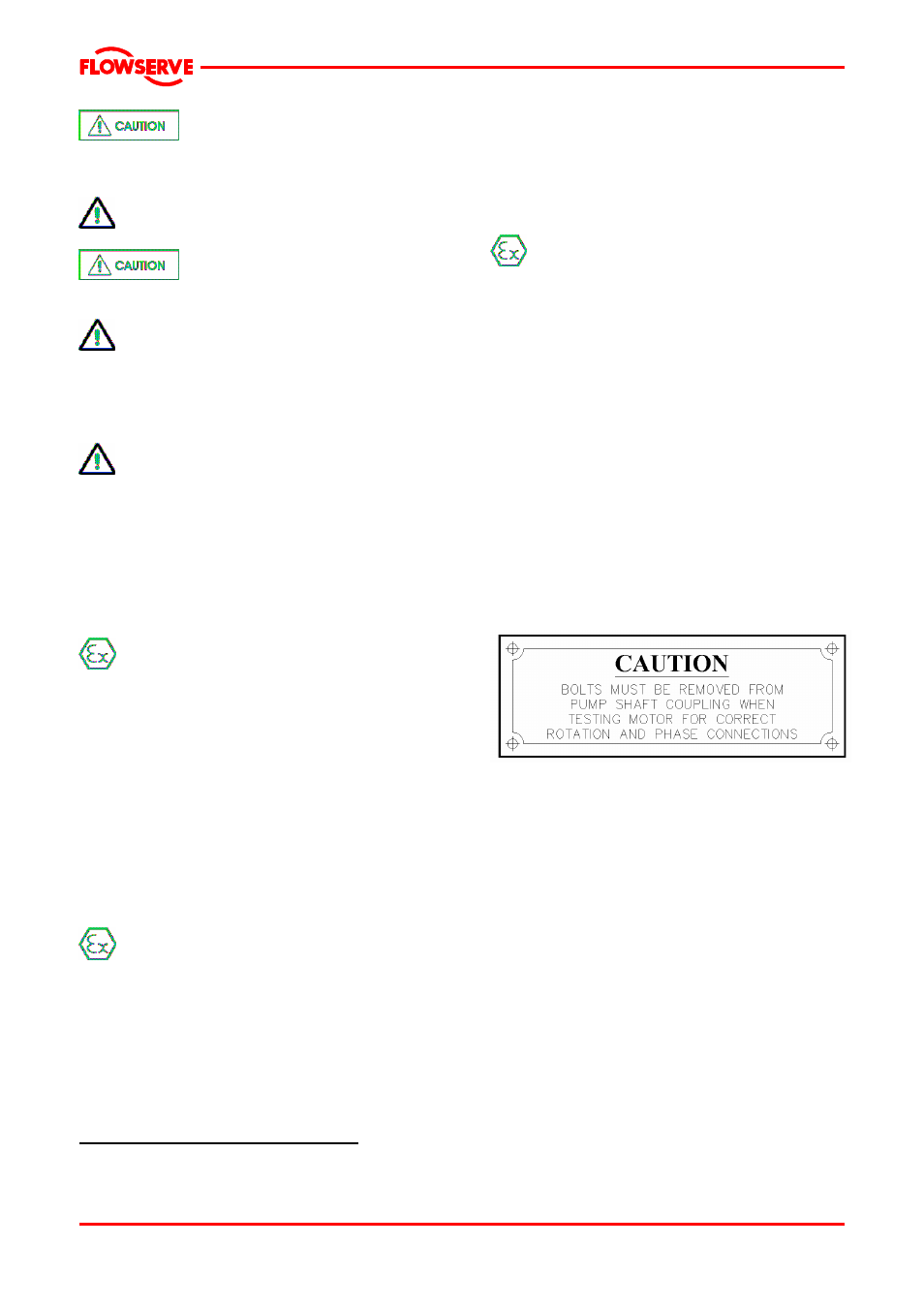
USER INSTRUCTIONS APM, APMA and APH MX0301 - 07/03
Page 5 of 32
®
LIFTING DEVICES
Mounted on individual parts are intended for lifting
the individual part only. Lifting slings must not put
excessive side thrust on the lifting device.
GUARDS MUST NOT BE REMOVED WHILE
THE PUMP IS OPERATIONAL
LIFTING ROTOR
Lifting rotor must be setting before start up the
pump, according nameplate. See point 5.5
FLUORO-ELASTOMERS (When fitted.)
When a pump has experienced temperatures over
250 ºC (482 ºF), partial decomposition of fluoro-
elastomers (eg Viton) will occur. In this condition
these are extremely dangerous and skin contact
must be avoided.
HANDLING COMPONENTS
Many precision parts have sharp corners and the
wearing
of
appropriate
safety
gloves
and
equipment is required when handling these
components. To lift heavy pieces above 25 kg (55
lb) use a crane appropriate for the mass and in
accordance with current local regulations.
1.6.4 Products used in potentially explosive
atmospheres
Measures are required to:
•
Avoid excess temperature
•
Prevent build up of explosive mixtures
•
Prevent the generation of sparks
•
Prevent leakages
•
Maintain the pump to avoid hazard
The following instructions for pumps and pump
units when installed in potentially explosive
atmospheres must be followed to help ensure
explosion protection. Both electrical and non-
electrical equipment must meet the requirements of
European Directive 94/9/EC.
1.6.4.1 Scope of compliance
Use equipment only in the zone for which it is
appropriate. Always check that the driver, drive
coupling assembly, seal and pump equipment are
suitably rated and/or certified for the classification of
the specific atmosphere in which they are to be
installed.
Where Flowserve has supplied only the bare shaft
pump, the Ex rating applies only to the pump. The
party responsible for assembling the pump set shall
select the coupling, driver and any additional
equipment, with the necessary CE Certificate/
Declaration of Conformity establishing it is suitable
for the area in which it is to be installed.
1.6.4.6 Preventing leakage
The pump must only be used to handle
liquids for which it has been approved to have the
correct corrosion resistance.
1.7 Nameplate and warning labels
1.7.1 Nameplate
Every pump has a name plate made in stainless
steel with information regarding operating condition
as capacity, total dynamic head, rotational speed,
specific gravity, rotor setting, power consumption
and serial number.
1.7.2 Warning labels
A stainless steel plate is attached to discharge
head requesting removing coupling bolts before
checking motor rotation and avoid damage to the
equipment.
1.8 Specific machine performance
For performance parameters see data sheet and
performance curve in this User Instructions.
1.9 Noise level
When pump noise level exceeds 85 dBA attention
must be given to prevailing Health and Safety
Legislation, to limit the exposure of plant operating
personnel to the noise. The usual approach is to
control exposure time to the noise.
Pump noise level is dependent on a number of
factors - the type of motor fitted, the operating
capacity,
pipework
design
and
acoustic
characteristics of the building.
2 TRANSPORT AND STORAGE