Flowserve MNV User Manual
Page 19
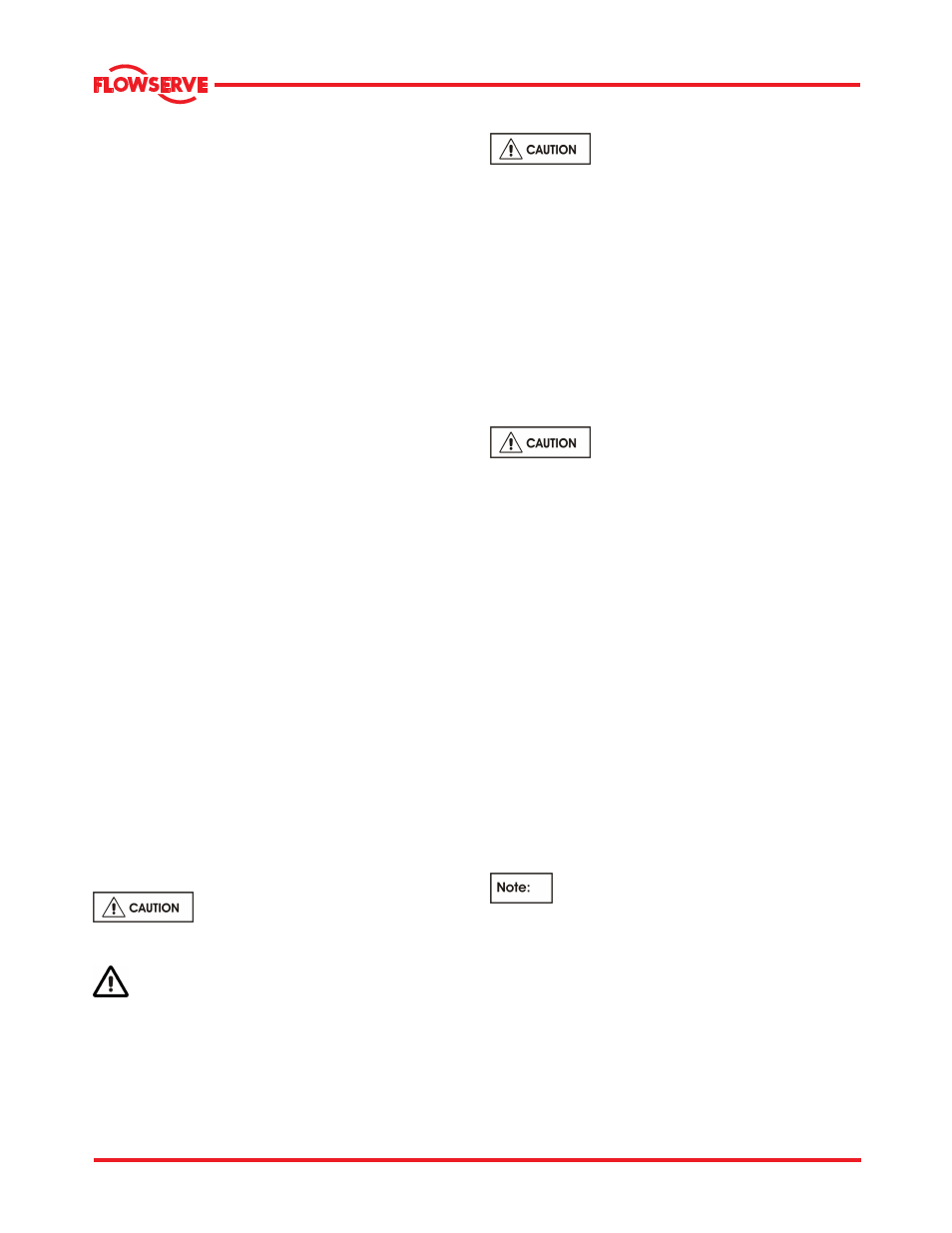
MNV & MNZ USER INSTRUCTIONS ENGLISH 71569188 11/04
Page 19 of 47
®
4.5.4 Alignment criteria
Accurate alignment of pump and drive shafts is
essential for successful operation. Misalignment
values as near to zero tolerance as possible are
required for trouble free operation and long
equipment life.
Universal joints are used to compensate for slight
changes in alignment that occur during normal
operation. It is not used to correct for initial
misalignment in excess of the values herein.
Although most couplings can withstand greater
misalignment, such can cause excessive vibration
and premature equipment failure. Driver and driven
coupling faces must be parallel to each other within
one degree.
An offset not exceeding 3.2 mm (0.125 in.) to 4.8 mm
(0.187 in.) per foot is recommended. Although
universal joint type shafting will withstand much
greater misalignment, such can cause excessive
vibration as well as premature failure of the
equipment. Note that a small misalignment is required
to lubricate the universal joint bearings that use needle
bearings.
Steady Bearing centerlines are to be concentric with
the center line of the shaft to within one degree.
Pumps with thick flanged non-spacer couplings can
be aligned by using a straight-edge across the
outside diameters of the coupling hubs and
measuring the gap between the machined faces
using feeler gauges, measuring wedge or calipers.
When the electric motor has sleeve bearings it is
necessary to ensure that the motor is aligned to run
on its magnetic centerline.
Refer to the motor manual for details.
A button (screwed into one of the shaft ends) is
normally fitted between the motor and pump shaft
ends to fix the axial position.
If the motor does not run in its
magnetic centre the resultant additional axial force
may overload the pump thrust bearing.
Complete piping as below and see section 4.8,
Final shaft alignment,
section 5,
Commissioning,
start-up, operation, and shutdown
before connecting
driver and checking actual rotation.
4.6 Piping
Protective covers are fitted to the pipe
connections to prevent foreign bodies entering during
transportation and installation. Ensure that these
covers are removed from the pump before
connecting any pipes.
4.6.1 Pipework velocities
In order to minimize friction losses and hydraulic
noise in the pipe work, it is a good practice to choose
pipe work that is one or two sizes larger than the
pump suction and discharge. Typically main pipe
work velocities should not exceed 2 m/s (6 ft/sec)
suction and 3 m/s (9 ft/sec) on the discharge
.
Take into account the available NPSH that must be
higher than the required NPSH of the pump.
Never use the pump as a support for
piping.
4.6.1.1 Piping strains
Pipe strains are a common cause of misalignment,
hot bearings, worn couplings, and vibration.
Satisfactory operation cannot be maintained when
the piping imposes a force on the pump. Misaligned
piping flanges can spring and pull a pump out of
position when their bolts are drawn up.
Flanges must have flat faces and be brought
squarely together before the bolts are tightened.
To avoid breaking the flanges when tightening the
bolting, mating pipe flanges should also have flat
faces and full face gaskets should be used.
Suction and discharge pipes, and associated
equipment, should be supported and anchored near,
but independent of the pump so that no strain will be
transmitted to the pump casing.
Pipe couplings that are not axially rigid are
sometimes used in the discharge and/or suction
piping to avoid transmitting any piping strains caused
by system pressure, thermal expansion or pipe
misalignment. Such pipe couplings allow transmittal
to the pump, a force equal to the area of the
expansion joint times the pressure in the piping.
These forces can have a significant magnitude and it
is impractical to design the pump casing, base plate,
support, etc., to withstand them.