Flowserve MNV User Manual
Page 11
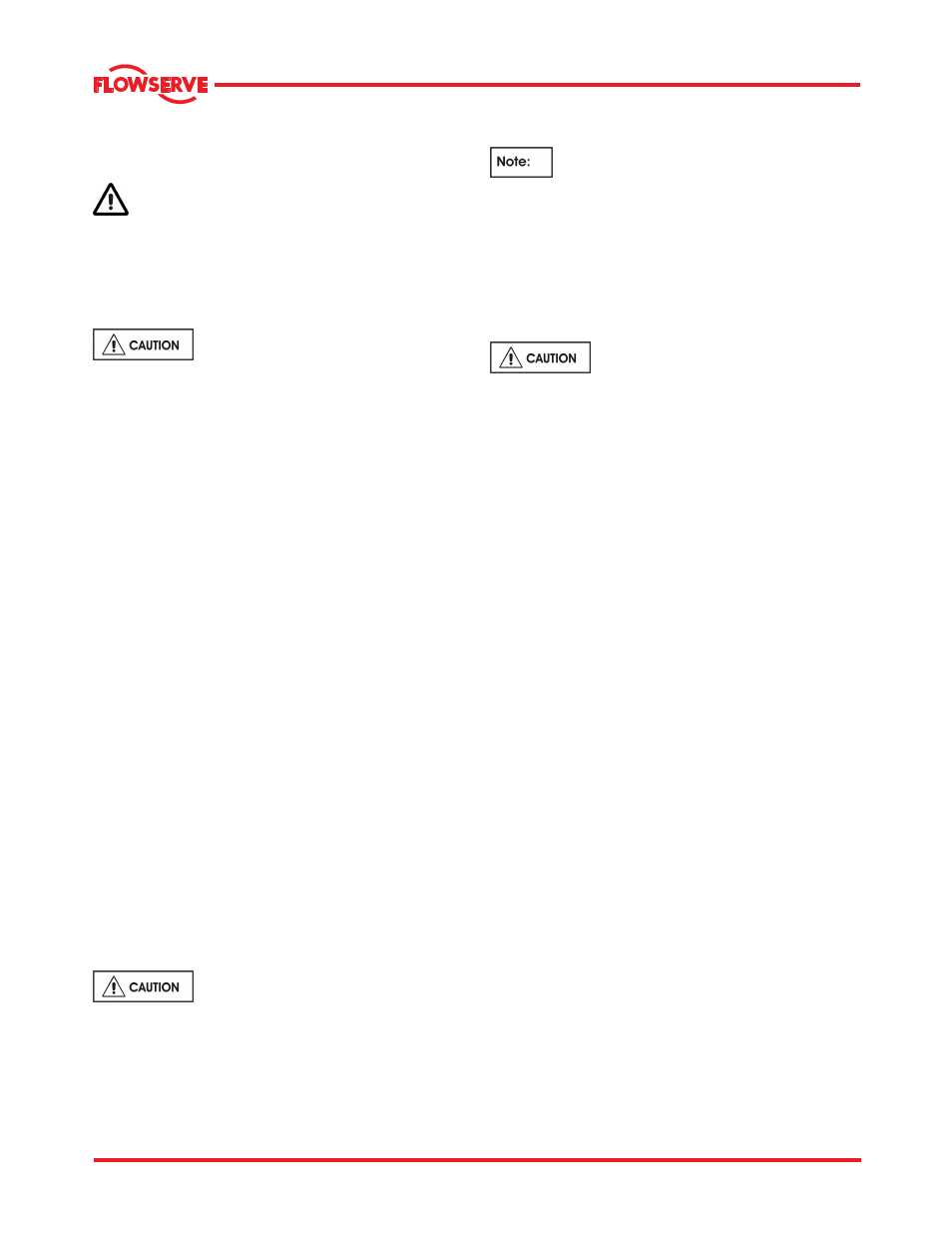
MNV & MNZ USER INSTRUCTIONS ENGLISH 71569188 11/04
Page 11 of 47
®
2.3.2 Lifting of driver
Use driver lifting lugs/ or follow driver manufacturer’s
User Instructions.
A crane must be used for all pump sets in
excess of 25 kg (55 lb). Fully trained personnel must
carry out lifting, in accordance with local regulations.
The driver and pump weights to be noted before
lifting is attempted.
2.4 Storage
Store the pump in a clean, dry location
away from vibration. Leave piping connection covers
in place to keep dirt and other foreign material out of
pump casing. Turn pump at intervals to prevent
brinelling of the bearings and the seal faces (if fitted),
from sticking.
2.4.1 Inspection before storage
a) Inspect the preservative coating/painted surfaces
on the various parts. Touch up whereever
necessary.
b) Inspect all covers over pump openings and piping
connections. If found damaged, remove the
covers and inspect interiors of the opening for any
deposits of foreign materials or water.
c) If necessary, clean and preserve the interior parts
as noted above to restore the parts to the "as
shipped" condition. Replace covers and fasten
securely.
2.4.2 Short term storage (less than 6 months)
When it is necessary to store a pump for a short time
before it can be installed, place it in a dry location
and protect it thoroughly from moisture.
When protective flanges are bolted to the suction and
discharge nozzles at the factory, they should not be
removed. Protect the bearings and the shaft against
moisture, dirt, or other foreign matter. To prevent
rusting in or seizing, lubricate the unit; see Section
5.2,
Pump Lubricants
.
Rotate the pump shaft a
minimum of 5 revolutions every two weeks to keep
the bearings coated with lubricant and to minimize
the effects of brinelling.
MNV and MNZ standard pumps are
grease lubricated. Oil lubricated anti-friction bearings
are factory lubricated to prevent rusting for a short
period of time only. It is important to fill the
recommended oil lubricant to proper level
immediately upon receiving the equipment.
2.4.3 Long term storage (6 months and over)
More thorough precautions are required if
the pump is scheduled to be stored for an extended
period of time. Contact Flowserve before long-term
storage is attempted for specific storage
requirements and warranty information.
The following is a general procedure and could vary
depending upon the pump design and specific
application.
The storage area should be a clean
and dry. The storage location not be subjected to
rapid changes in temperature, light (no direct lighting)
or humidity, and relatively free of ground transmitted
vibration due to heavy construction and/or
machinery.
A temperature range of 5
o
to 50
o
C ( 40
o
to 120
o
F)
with non-condensing humidity is recommended.
a) Drain fluid from the pump, rotate the pump rotor
once in the proper direction and blow the liquid
end dry with air.
b) Coat the interior surfaces of the liquid end with
rust inhibitor by brushing, spraying or fogging.
Rotate the pump shaft one turn in the proper
direction while coating.
c) Remove the packing and seal cage from the
stuffing box to prevent corrosion due to
condensation. Coat the interior machined
surfaces of stuffing box with a rust inhibitor. This
step may be omitted if the pumps are stored prior
to initial use.
d) For grease lubricated bearing frames, fill the
cavity between the bearing covers and bearings
with a good grade of NGLI No. 2 lithium base
grease to prevent contamination of the bearings.
Ensure the bearings are thoroughly packed with
grease. Lubrication quality and quantity must be
checked every six months and replaced or
replenished as necessary.
e) Coat all threaded openings with rust inhibitor and
plug. Coat machined surfaces of exposed
flanges with rust inhibitor and then cover with
fiberboard or wood flange covers. Desiccant
bags should be secured to the covers prior to
putting them in place and must not contact metal
surfaces.
f) Coat exposed, unpainted, and machined
surfaces with a rust inhibitor.