3 recommended spares and consumables, 4 tools required, 5 fastener torques – Flowserve Guardian Sealless Metallic User Manual
Page 37: 6 setting impeller clearance
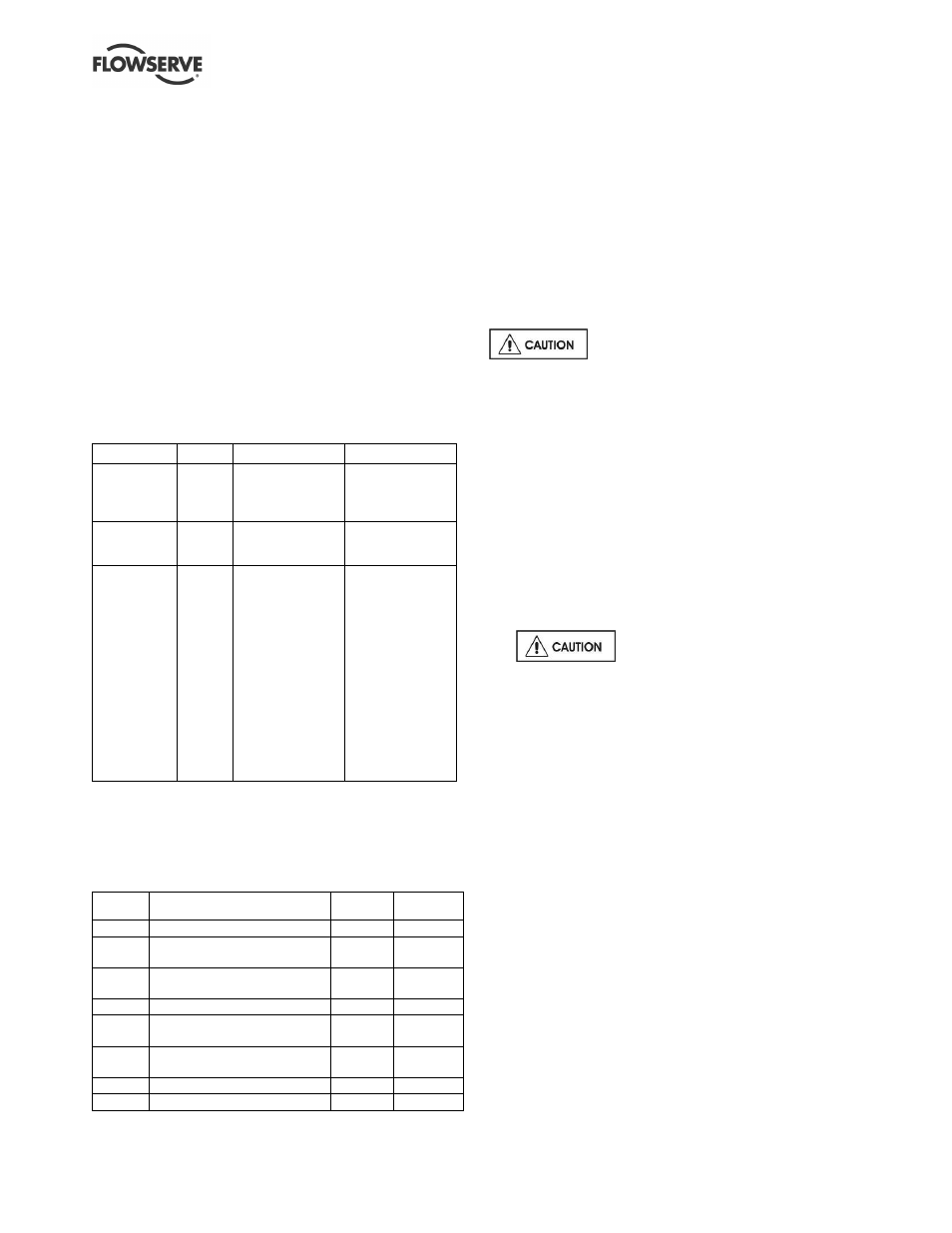
GUARDIAN USER INSTRUCTIONS ENGLISH 71569212 08-11
Page 37 of 68
flowserve.com
6.3 Recommended spares and
consumables
On very critical services, where downtime is especially
crucial it may be best to stock spare pumps or the
rotating assembly, allowing complete service to be
quickly restored. The damaged assembly can be taken
to a shop, repaired and stored for back-up.
6.4 Tools required
Do not perform maintenance on a steel workbench.
The magnets present in the pump are strongly attracted
to ferrous materials. Use a non-magnetic (such as
wood or plastic) workbench instead. The use of non
magnetic tools is also recommended. See Figure 6-1
for a list of recommended maintenance tools.
Figure 6-1: Recommended maintenance tools –
Guardian G & H Series pumps
Task
Section Group 1
Group 2
Power end
back pullout
6.7.1
¾ in. open end
wrench
5/8 in. socket
9/16 in. socket
¾ in. open end
wrench
5/8 in. socket
9/16 in. socket
Complete
pullout
6.7.2
¾ in. open end
wrench
¾ in. socket
¾ in. open end
wrench
15/16 in. socket
Disassembly
/assembly
6.7.3 to
6.9.5
Torque wrench
Arbor or bench
press
Rubber mallet
Durco impeller
wrench
Coupling key
1-1/2 in. open end
wrench
7/16 in. wrench
3/16 in. hex head
wrench
¾ in. socket
½ in. socket
Torque wrench
Arbor or bench
press
Rubber mallet
Durco impeller
wrench
Coupling key
1-5/8 in. open end
wrench
9/16 in. wrench
1/2 in. wrench
5/16 in. hex head
wrench
9/16 in. socket
Spanner wrench
6.5 Fastener torques
See Figure 6-2 for recommended fastener torques for
Guardian G & H series pumps.
Figure 6-2: Recommended bolt torques
Item
Description
Group 1
Nm (lbf•ft)
Group 2
Nm (lbf•ft)
222
Pump shaft cap
34 (25)
47 (35)
6570.3
Bearing housing cap to bearing
housing
11 (8)
41 (30)
6570.4
Bearing housing foot to bearing
housing
34 (25)
127 (94)
6570.5 Bearing housing to adapter
15 (11)
15 (11)
6570.6
Containment shell to bearing
holder
15 (11)
34 (25)
6570.8
Outer magnet flange to power
end shaft
7 (5)
7 (5)
6580.1 Pump casing to adapter (1/2 in.)
34 (25)
34 (25)
6580.1 Pump casing to adapter (5/8 in.)
n/a
61 (45)
6.6 Setting impeller clearance
A new impeller gasket [4590.2] must be installed
whenever the impeller has been removed from the
shaft. Impeller clearance settings may be found in
Section 5.3
6.6.1
Installation and clearance setting for
Guardian G & H series reverse vane
impellers
Install the impeller [2200] by screwing it onto the shaft
(use heavy gloves) until it firmly seats against the
shaft shoulder.
The impeller could have sharp edges,
which could cause an injury. It is very important to
wear heavy gloves.
Tighten the impeller with the impeller wrench from the
Flowserve Mark 3 tool kit. To do this, grasp the impeller
in both hands and, with the impeller wrench handle to the
left (viewed from the impeller end of the shaft) spin the
impeller forcefully in a clockwise direction to impact the
impeller wrench handle on the work surface to the right.
6.6.2
Setting the impeller clearance
a) Temporarily tighten the impeller [2200] to the
pump shaft [2100.1]. Turn the impeller in a
clockwise direction until the impeller is firmly
seated but only hand tight.
Do not attempt to tighten the
impeller on the shaft by hitting the impeller with a
hammer or any other object or by inserting a pry bar
between the impeller vanes. Serious damage to
the impeller may result from such actions.
b) Place the entire assembly vertically on the
workbench with the impeller down and supporting
the weight of the assembly. Measure the
minimum clearance between the bearing holder
face [3830] and the impeller [2200] with a feeler
gauge without forcing the impeller away from the
face. Measure the clearance between the bearing
holder and ALL THE VANES to determine closest
vane. Use the smallest measurement as your
guide and record this number.
c) The Guardian Magnetic Drive requires a
clearance of 0.45 ±0.08mm (0.018 ±0.003 in.),
regardless of operating temperature, between the
closest impeller vane and the face of the bearing
holder. Determine the number of shims that must
be placed between the impeller and the thrust
collar by subtracting the minimum clearance
between the bearing holder and the impeller from
the thickness of the impeller shims already
inserted. Add 0.45 mm (0.018 in.) to this