BUG-O Systems BGW-5000 User Manual
Page 12
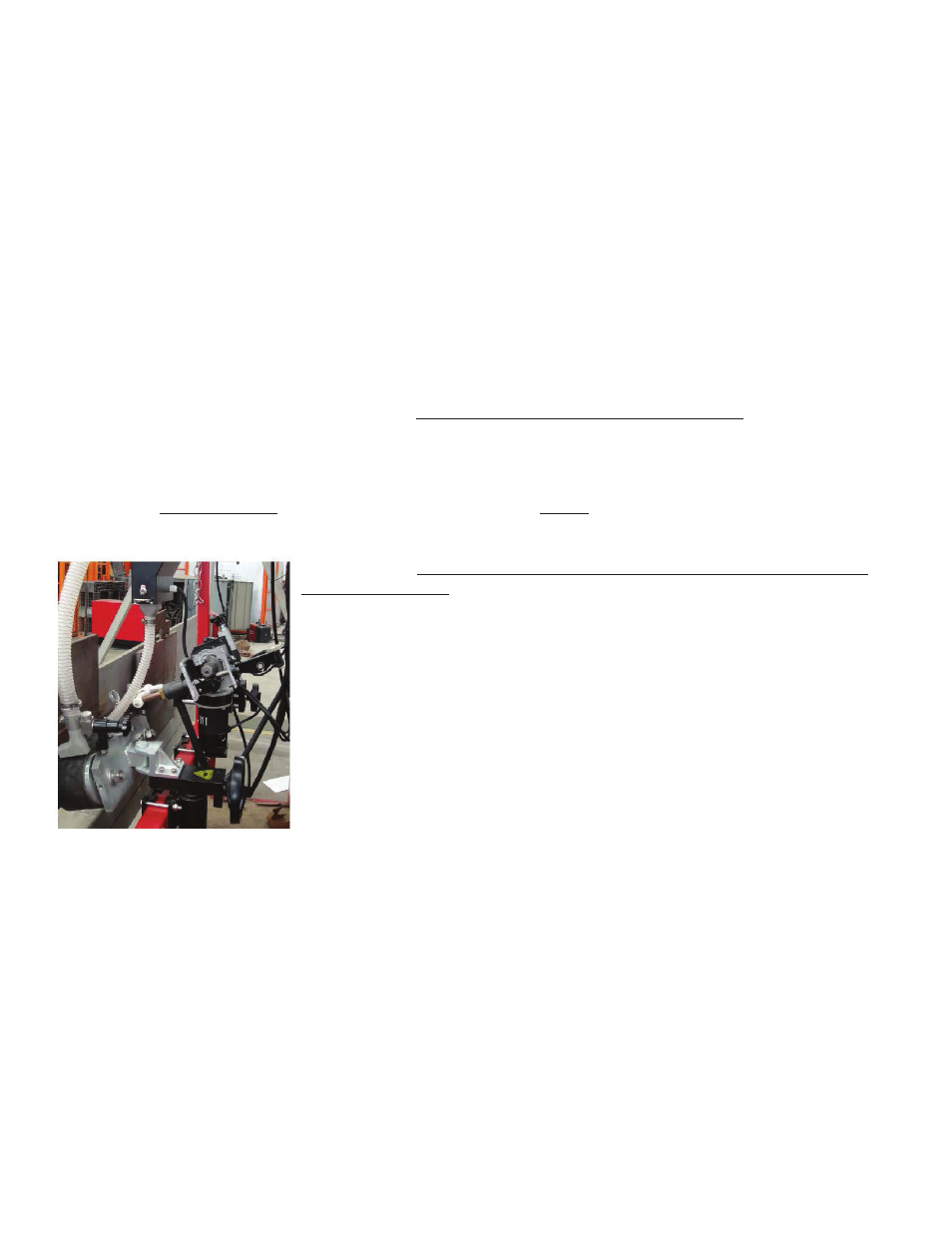
12
AC inverter:
1. Single-phase 220VAC input voltage
2. Automatic lift in torsion, 150% lift torsion in 6Hz.
3. Fully programmed & calibrated in factory
4. Soft PWM, running in low noise
5. 15 speed, PID, 4-20 MA input
6. Provides RS-485 communication
Caution: All inverter drives inside the GIRTH WELDER control are pre-programmed before the Girth
welder is delivered to users on site, please consult factory if re-programming is required.
The SEW motors and reducer require minimal maintenance with advantages of low noise & vibration, with
96% high efficiency through the reducer. It consists of a high rigid housing and spur gear; all parts are
precisely machined with minimum tolerance for accurate travel mechanism.
3.3 Welding Gear
The standard welding equipment supplied is the Lincoln’s NA-3S/MAXsa 29 wire feed head and weld head
fitted with nozzle, wire feed rolls, wire straightener, and 50lbs (23Kg) wire reels for feeding up to 3.2 mm
(1/8") diameter wire.
Lincoln USA DC600 /DC1000/ACDC1000SD is the standard power supply for the girth welder. Standard
input power is 380V/3ph/50Hz and the line power requirement is 40kVA. Other voltages and frequencies are
available, please consult factory for details.
Please refer to Lincoln’s NA-3S/MAXsa 29 DC600 /DC1000/ACDC1000SD
Instruction manuals for more information on their welding equipment.
Power supplies are installed on a steel storage case with the electrical
cabinet for weather protection.
3.4 Weld Head Assembly
The BGW weld head is mounted on a manual cross slide system, which
allows the operator complete control of wire placement and joint tracking.
Due to the lack of visibility of the submerged arc welding process, a
laser pointer is mounted on the nozzle to provide a position reference for
operator while welding.