BECKHOFF BC3100 User Manual
Page 20
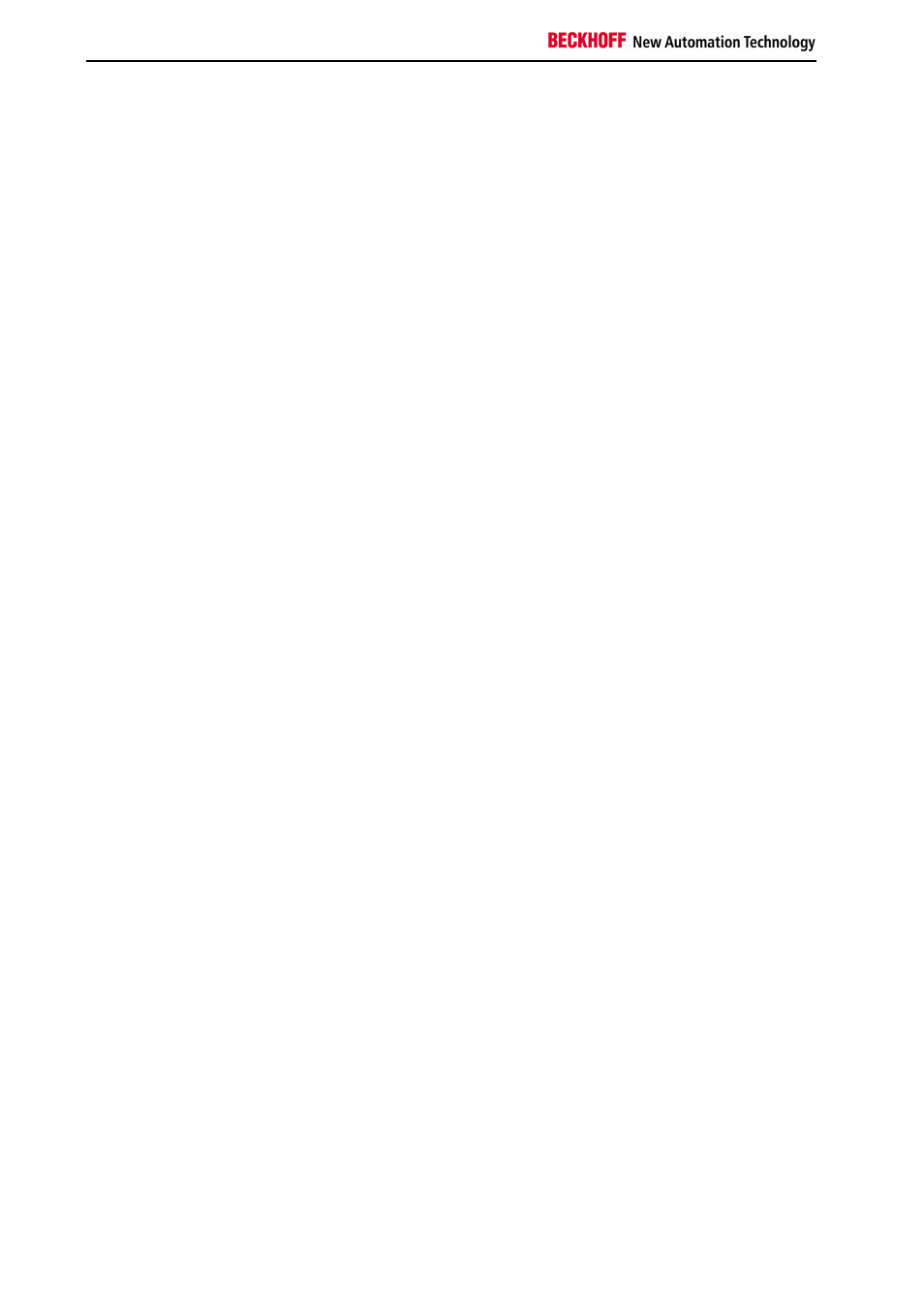
PROFIBUS-DP basics
20
BC3100
attached to one bus. The bus couplers BK3xx0 permit you to select a
station address between 0 and 99. The quantities specified in the system
configuration include the number of stations, the assignments of station
addresses to I/O addresses, the consistency of the I/O data, the format to
be used for diagnostic messages and bus parameters that are to be used.
Each PROFIBUS DP system is made up of a number of different types of
device. We distinguish three types, depending on the tasks involved:
DP master class 1 (DPM1), such as an IM308-C or TwinCAT
This is a central control unit which exchanges information with the
decentralized stations (DP slaves) in a fixed message cycle. Typical
devices include stored program control units (PLC), numeric control units
(CNC) or robot control units (RC).
DP master class 2 (DPM2)
Devices of this type are programming, planning or diagnostic devices. They
are used to configure the DP system when the equipment is set up and
taken into service.
DP slave, e.g. the bus couplers or bus terminal controllers.
A DP slave is a peripheral device (sensor/actor), which reads in input
information and passes output information to the peripherals. Devices
which only input information, or only output information, are also possible.
Typical DP slaves are devices with binary I/O ports for 24V or 230V,
analog inputs, analog outputs, counters etc.. The volume of input and
output information depends on the individual device, up to a maximum of
244 bytes for input data and 244 bytes for output data. Due to cost factors,
and for technical and implementational reasons, many of the currently
available devices operate with a maximum data length of 32 bytes. The
Profibus coupler BK3000 can use the full length of 244 bytes, although the
master unit IM308-C restricts this to 52 bytes for input data. The IM308-B
enables you to use up to 122 bytes of input data.
In a mono-master system, only one master is active on the bus during the
operating phase of the bus system. The SPS control unit is die central
control element. The DP slaves are coupled to the SPS control unit
decentrally by means of the transfer medium. This system configuration
achieves the shortest bus cycle time.
In multi-master operation there are a number of masters on a single bus.
These either constitute independent subsystems, each consisting of one
DPM1 and the corresponding DP slaves or additional planning and
diagnostic devices. All the DP masters can read the input and output
mappings of the DP slaves. Although the output can be written by only one
DP master (namely the DPM1 which was appointed when the system was
specified). Multi-master systems achieve an average bus cycle time. If
timing is critical to your application you should connect up a diagnostic tool
to monitor increases in the bus cycle time.
Device master file (GSD)
The manufacturers of PROFIBUS DP provide users with documentation
covering the performance characteristics of the devices, in the form of a
device data sheet and a device master data file. The layout, content and
coding of this device master data (the GSD) are standardized. It facilitates
convenient project planning with any desired DP slaves using planning