BECKHOFF CX1020 User Manual
Page 12
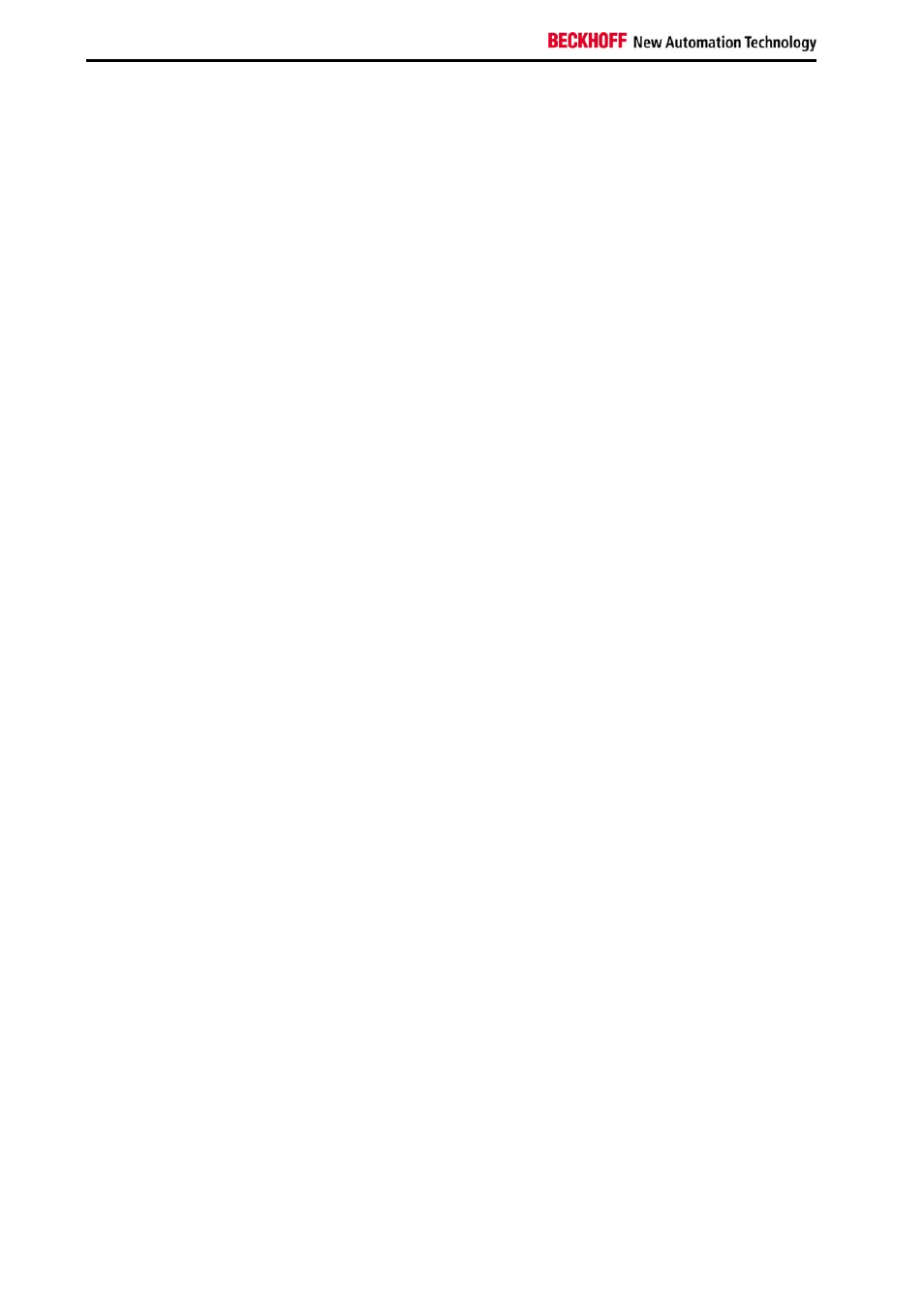
Product overview
10
Embedded PC
characteristics - e.g. both support PROFIBUS DP-V2. In practice, this means that the PROFIBUS master can be
positioned exactly where it is required within a machine. It no longer has to be implemented as a plug-in card in the
IPC or a master controller in the control cabinet.
PLC, Motion Control, interpolation and visualisation
As a top-hat rail IPC and in conjunction with the TwinCAT software from Beckhoff, the CX1020 offers the same
functionality as large Industrial PCs. In terms of PLC, up to four virtual IEC 61131 CPUs can be programmed with up
to four tasks each, with a minimum cycle time of 50 µs. All IEC 61131-3 languages can be used.
Moreover, all TwinCAT functionalities are available for Motion Control applications:
In theory, up to 256 axes can be controlled. In addition to simple point-to-point movements, more complex multi-axis
functions such as "electronic gearbox", "cam plates" and "flying saw" can be implemented. In contrast to the CX1000,
due to its higher CPU performance the CX1020 can now also execute interpolating 3D path movements and
DIN66025 programs.
In addition to real-time execution of control tasks, the TwinCAT real-time kernel ensures that enough time remains for
the user interface (HMI), to communicate with the real-time components via software interfaces such as ADS or OPC.
For the CX1020 the same basic principle applies: it is a programming tool for all controllers.
The complete programming of PLC, Motion Control and visualisation is transferable to all PC controls from Beckhoff,
which is reassuring in cases where it becomes apparent during a project that more processing power is required after
all. In this case a system with higher performance can be used.
Basic CPU module
Further system interfaces or fieldbus connections can be added to the basic CPU module. The CPU module requires
a CX1100 type power supply module.
All CX1500 fieldbus modules and all CX1100 power supply units from the CX1000 series can be used in combination
with the CX1020.
The CX1100-0004 power supply unit offers a direct interface between the CX1020 and the EtherCAT Terminals. The
combination of CX1020, EtherCAT and TwinCAT enables cycle and response times of less than 1 millisecond.
The CPU module is available in several variants. These relate to:
- Internal memory configuration: there are three options - either 64 MB Flash/256 MB DDR RAM (standard), 512 MB
RAM, or 1 GB RAM.
- System interface configuration: as an option, a DVI and two USB Interfaces can be added to the combination of two
Ethernet and RJ 45 ports that are always present.
- Operating system: There is a choice between "Microsoft Windows CE.NET" or "Microsoft Windows XP Embedded".
- Pre-installed TwinCAT software: CX1020 can be pre-installed without a TwinCAT system, with TwinCAT CE PLC,
TwinCAT CE NC PTP or TwinCAT CE NCI, or with the associated full version of the individual TwinCAT levels for
PLC and Motion Control.
System interfaces
Further system interfaces for serial communication (2x RS 232 or RS422, RS485), 2 x USB 2.0 interfaces, video
output (DVI +) , CF card reader/writer or audio signals can be ordered separately.
Fieldbus interfaces
All CX1500 fieldbus modules and all CX1100 power supply units from the CX1000 series can be used in combination
with the CX1020.
The fieldbus interfaces are currently available as master and slave versions for the following fieldbuses:
Beckhoff Lightbus, Profibus DP, CANopen, DeviceNet or SERCOS interface (only master)
The master fieldbus connections enable a CX1020 system to use Beckhoff fieldbus components (such as Bus
Coupler, Bus Terminal Controller or Drive Technology) as local control components for complex systems.
Slave fieldbus connections enable the CX1020 system to be used as a subordinate distributed control system for
complex or modular systems.
Note:
Documentation describing the fieldbus connections is available separately.