C8000, Digital audio modular processing system, System configuration – Junger Audio C8000 System User Manual
Page 11
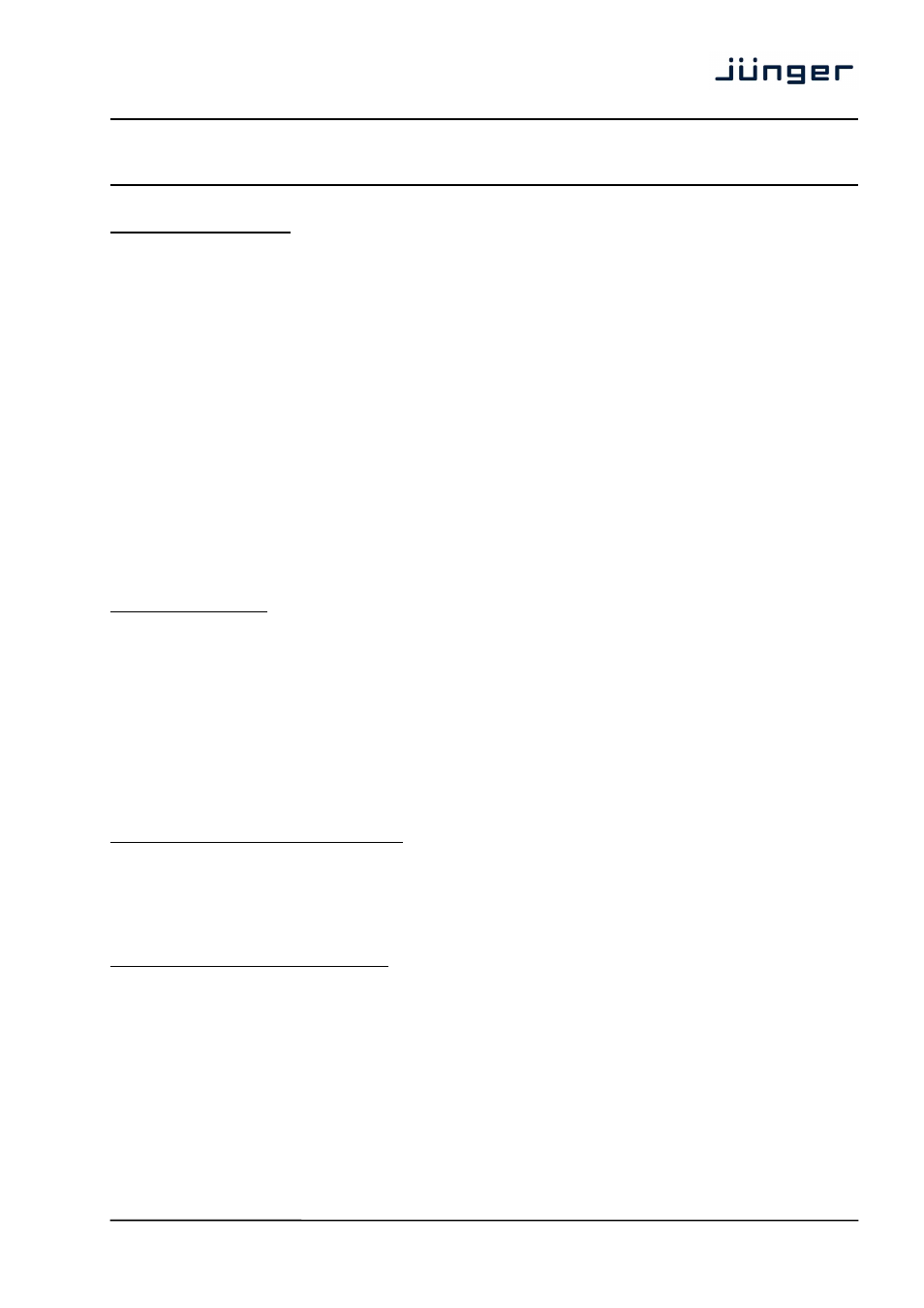
digital audio
modular
processing system
C8000
system configuration
5/7
CAN address assignment:
In the above images you can see a very important switch labeled “ADDRESS” or “CAN” or “CAN/BUS”
respectively. It determines the module address for the CAN-bus. All devices that can be remote controlled
are connected to the CAN-bus of the frame. The CAN-bus is a two wire bi-directional bus. Each party must
have a unique address to allow for proper communication. Therefore it is of major importance that you
set a unique address for each module inside a frame. This allows for 16 different module addresses per
frame: 0 – F.
We have extended the range of addresses for a frame to 32 (0x0 – 0x1F). A defined DIP-switch is used to
set the CAN address “+16” offset. See manual for details. Special modules like the new GPI/O C8817 have
an automatic “+16” offset.
Because the C8k System does not have slot encoding, you may place a module where ever you like. The
virtual location of modules in the OVERVIEW window of the GUI is derived from its CAN-address. The
window is divided into 6 rows with 8 columns. First row contains the Frame Controller and Sync-Module(s).
Second row is empty. 3
rd
to 6
th
rows show all kind of manageable modules. Address “0” puts the modules
graphical box to the upper left place (row #3 left hand side), while address “1F” puts it to the bottom right
place (row #6 right hand side).
Synchronizing a frame:
The C8k frame is a digital audio processing system. Therefore it is of major importance that you synchronize
its digital inputs and outputs with other equipment in a signal distribution chain.
For standard applications the frame is equipped with a Sync-Module C8830 (see manual for details). This
module generates all relevant processing clocks and puts those clock signals on the back plane so all
devices can be synchronized properly. Because the sync signal distribution is driven by active components on
the back plane, there are only 4 slots (marked with red slide bars) at the rear of a frame which must be used
to insert a module that synchronizes the frame. The sync module can run on internal clock for stand alone
applications or may be synchronized externally either by AES sync, Word Clock or Video Black Burst. On a
BNC output it provides the internal Word Clock of the frame for other external devices.
Fail save operation with two sync modules:
For automatic fail over operation the frame may be equipped with two Sync-Modules (see manual for details).
One acts as the master while the other one is the slave. If the master loses its reference or dies, the slave
automatically takes over the clock generation for the frame.
Synchronizing a frame to an input signal:
If there is a demand by the application, the frame can also be synchronized via SDI or MADI. This must be
performed with great care because the synchronization relies on one signal feed. If this SDI or MADI signal
fails for any reason the whole frame is no longer synchronized. In this case the frame will run “free” on
approx. 48 kHz sample rate and other processing channels will be influenced (clicks and pops).
If synchronizing the frame via SDI or MADI, such interface must be inserted
instead
of the SYNC-
Module C8830 into one of the four above mentioned red colored slots and must be set to
MASTER
mode.