Product handling, Controllers, 5400 tubular reactor system – Parr Instrument 5400 User Manual
Page 8
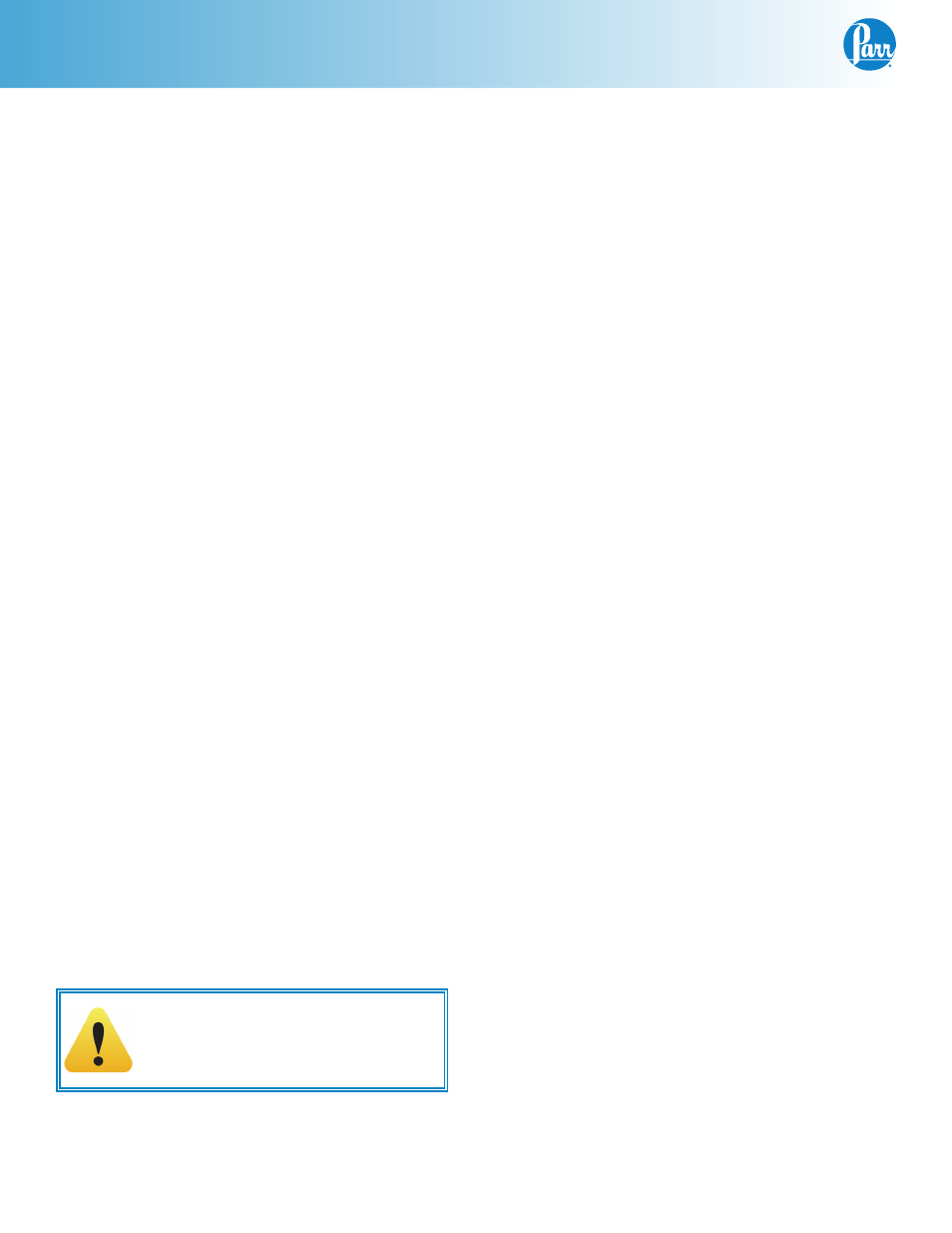
5400 Tubular Reactor System
P a r r I n s t r u m e n t C o m p a n y
8
5400 Tubular Reactor System generally consists of
one or more HPLC pumps rated for up toeither 1500
or 5000 psig. For best results, the pumps should
be located on the bottom shelf of the reactor cart
with the liquid supply source located on the upper
shelf. The inlet to the pump should be connected
using the tubing and filter assembly provided by
the pump manufacturer with the pump. The pump
outlet utilizes 1/16” tubing connected to a check
valve at the top of the tubular reactor. The flow rate
delivered by the HPLC pump can be manually set
on the faceplate of the pump as well as the starting/
stopping of the pump. If a 4871 Process Controller
is being used, these functions can also be per-
formed remotely. For operation and maintenance of
the pumps, see the supplier manual provided with
each pump.
Product Handling
The product handling components of a typical
Series 5400 Tubular Reactor System consist of a
cooling condenser, a gas/liquid separator and a
back pressure regulator (BPR). In order to cool the
product stream from the reactor, a tube-and-shell
heat exchanger is used to act as a cooling con-
denser. Generally a low flow of water is all that is
required to significantly cool the product. With the
tube side of the condenser connected between the
reactor and the gas/liquid separator, water can be
connected to the hose barbs on the shell side of the
condenser for cooling. The outlet side of the shell
should be routed to a drain for continuous flow of
water through the condenser.
The cooled product stream is generally routed to a
gas/liquid separator. In the separator vessel, liquids
are condensed and collected in the bottom of the
vessel. Gases and non-condensed vapors are allowed
to leave the top of the vessel. The gas/liquid separator
is generally sized to act as a liquid product receiver
that can be manually drained periodically. The gas/
liquid separator is generally one of the non-stirred
pressure vessels made by Parr Instrument Company.
More information about our non-stirred
pressure vessels can be found in operating
instruction no. 239M for series 4600 & 4700
General Purpose Vessels.
The reactor and separator vessel are kept at a con-
stant pressure through the use of a back pressure
regulator (BPR). This style of regulator will release
products only when the system pressure exceeds a
preset value. The BPR can either be a manual style
regulator with a knob, adjustable by the operator,
to set the desired system pressure or an automated
BPR system controlled by a 4871 Process Controller.
The automatic system consists of a current-to-pres-
sure (I/P) converter and an air loaded BPR. Through
the controller, the system pressure is monitored and
compared to the set point and adjusted by send-
ing an electronic signal to the I/P converter which
adjusts the air pressure to the diaphragm on the air
loaded BPR. A source of 100 psig of dry air or nitro-
gen is required to be connected to the I/P converter.
For complete details on each of the components,
see the supplied manufacturer manuals.
Because of the inherent nature of the BPRs (both
manual and automated) there may be some sys-
tems which the pressure may not vent completely to
atmospheric pressure using the BPR only. A manual
valve is included in the vent line upstream of the
BPR so that the system pressure can be vented
completely when desired.
Controllers
Series 5400 Tubular Reactor Systems are generally
equipped with one of two different types of control-
ler solutions: a “manual” system which utilizes a
number of different controllers to provide the over-
all control system or the 4871 Process Controller.
The manual control system will include a Parr 4848
or 4838 controller for each heater zone. The external
temperature of each zone is monitored and con-
trolled in order to maintain the desired temperature
set point. Additionally, variables such as the system
pressure or internal temperatures can be displayed
on modules dedicated to these functions on the
individual controllers. Similarly, the Parr A2200E
controller is utilized to provide the flow set point to
the MFC as well as display the resulting flow. The
A2200E can be utilized to interface with up to four
MFCs. A manual BPR is used to control the system
pressure. For a detailed description of each of these
controllers, the corresponding manuals should be
referenced.