Typical components, Reactor, Gas feed – Parr Instrument 5400 User Manual
Page 7: Liquid feed, 5400 tubular reactor system
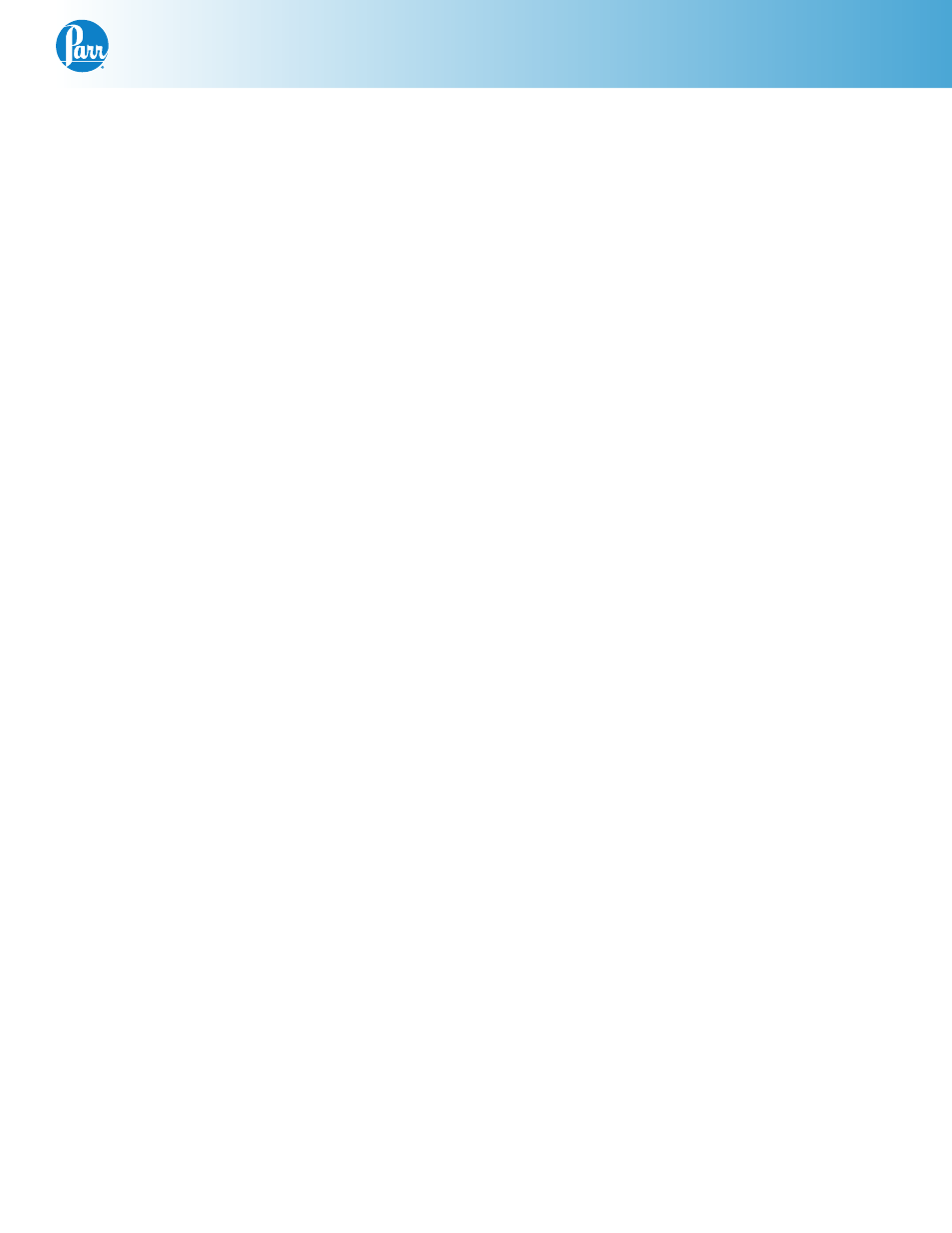
5400 Tubular Reactor System
w w w . p a r r i n s t . c o m
7
Typical Components
Reactor
There are two basic styles of tubular reactors avail-
able from Parr Instrument Company. The smaller
diameter reactors are available with either a 3/8”
O.D. (model 5401) or a ½” O.D. (model 5402). The
larger diameter reactors are available with either
a 1” I.D. (model 5403) or a 1.5” I.D. (model 5404).
Either style can be easily removed from the assem-
bly for catalyst loading, cleaning or inspection.
To remove the smaller diameter reactors, the pres-
sure should be released either through the BPR or
the manual vent valve. Loosen the compression
fittings on the top and bottom of the reactor. The tu-
bular reactor can now be removed from the system.
Catalyst should be loaded into the bottom of the
reactor with a small amount of glass wool or other
inert material to hold the catalyst in place. Once
the catalyst is installed, the tubular reactor can be
reinstalled and the compression fittings tightened
with wrenches for a pressure tight seal.
The larger diameter reactors utilize a split ring
assembly on the top and bottom as well as a flat
gasket. As with the smaller units, the pressure
should be released either through the BPR or the
manual vent valve. Loosen the compression fit-
tings on both the reactor inlet and outlet. The entire
reactor assembly can now be removed and taken to
a bench for catalyst loading, cleaning and inspec-
tion. Loosen the six Compression bolts on the split
ring sections for each end. If equipped, the internal
pre-heat spiral can be inserted into the top of the
reactor. Catalyst should be loaded into the bottom
of the reactor with glass wool to hold it in place.
Catalyst support spools can also be loaded into the
bottom of the reactor if desired.
Examine the head gaskets on both the top and
bottom heads. If flexible graphite gaskets were
used, the old gaskets may need to be removed and
replaced each time the reactor is disassembled.
Typically PTFE gaskets can be used multiple times.
After considerable use, some of the PTFE gasket
may extrude into a thin, ragged edge around the
inside and outside diameters. This does not neces-
sarily mean that the gasket must be replaced, but
the extruded portion should be removed with a
sharp knife.
Once everything has been inspected, the heads can
be reinstalled to the reactor cylinder with the split
ring closures. Tighten each of the cap screws with
the wrench furnished with the apparatus. Tighten-
ing should proceed in a criss-cross pattern rather
than progressively around the circle. When the
split ring assembly is completed, the reactor can
be reinserted into the complete assembly and the
compression fittings can be retightened.
Gas Feed
The gas feed system typically consists of at least
one gas mass flow controller (MFC) and a gas purge
line. Either a 4871 controller or an A2200E controller
are required to introduce the set point to the MFC.
The instrument will then compare the actual flow
rate delivered to the set point and automatically
adjust an integral control valve to assure a constant
flow. Each MFC will be marked with the type of gas
to be metered, the maximum operating pressure,
the maximum flow rate and the calibrated pres-
sure settings. The gas source should be connected
with a suitable tubing connector to the inlet of the
gas manifold with care taken as to not exceed the
pressure ratings of the MFC. Each MFC provided
will include the suppliers manual for reference. The
purge line should similarly be connected with a
suitable tubing connector to the purge connection.
The needle valve in the purge line can be used to
manually set the flow of the purge gas through the
system.
If the Tubular Reactor System is controlled by a 4871
Process Controller, the shut-off valves are typically
automated on/off valves. Valves connected to a gas
feed line equipped with any MFC are typically pro-
grammed to open when a set point is entered into
the controller and to close when the flow set point
is set to zero or upon loss of power or pressure. The
automated valves require a Parr 4877 Valve Control-
ler to interface with the 4871 Process Controller. A
source of 100 psig of dry air or nitrogen is required
to be connected to the 4877 controller in order
to operate the automated valves. Reference the
supplemental manual for the 4877 Valve Controller
for a more detailed description.
Liquid Feed
High pressure piston pumps are most often used to
inject liquids into a pressurized reactor operating in
a continuous-flow mode. The liquid feed in a Series