Installation – Lingenfelter L460160000 Lingenfelter RPM-003 RPM Activated Switch Instructions v1.5 User Manual
Page 5
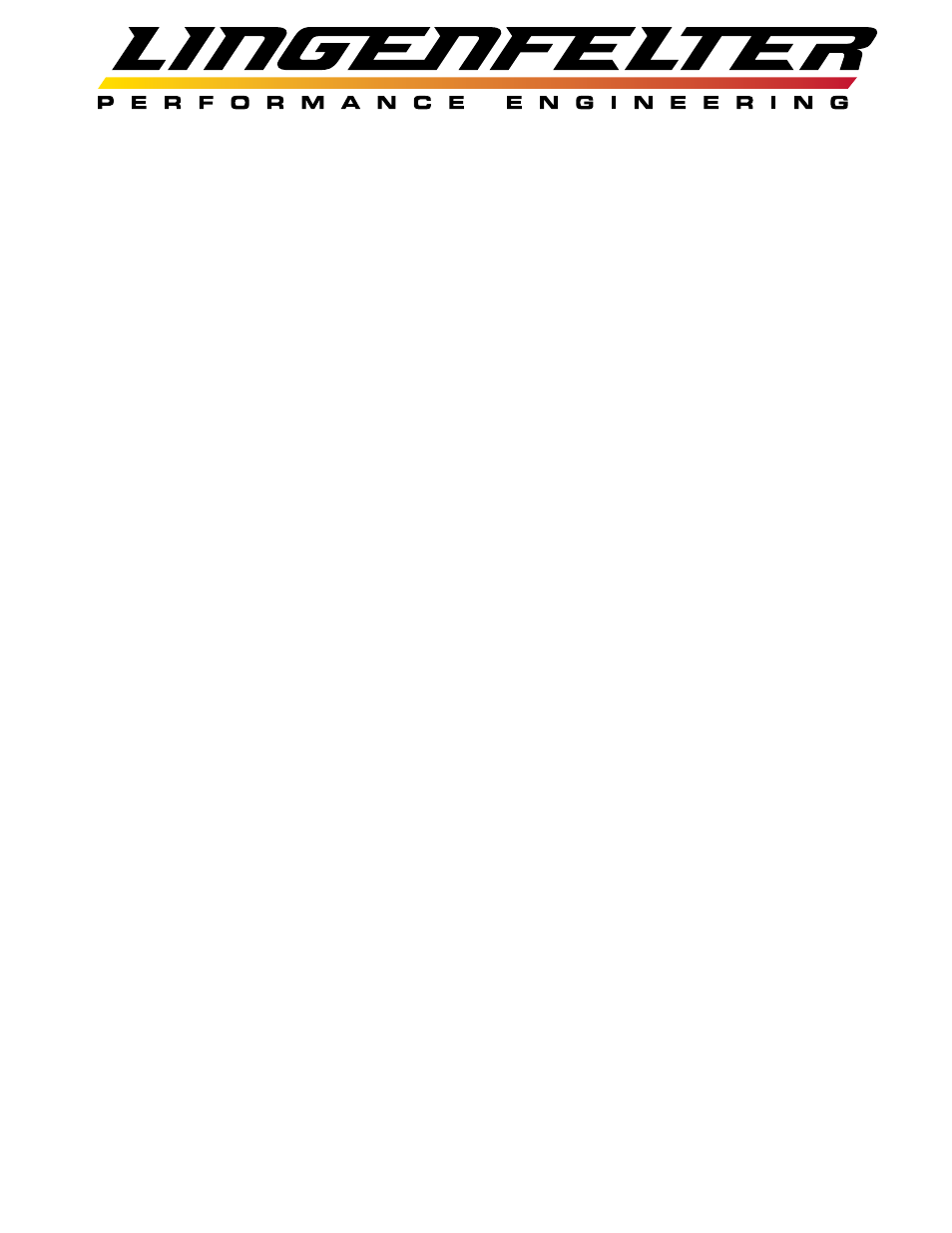
Page 4 of 17
Operation LED Status:
• Solid RED when the unit is powered up but no tachometer signal is detected
• Solid GREEN when a tachometer signal is detected, but is not within the RPM window or has not reached the RPM
activation point
• GREEN blinking when outputs are active in RPM switch mode or Window switch mode
• GREEN blinking when module is in programming mode (all 10 position switches set to zero and 16 position switch set
to 0.5, low range)
• Blinking GREEN+RED after the programming button has been pressed and the RPM-003 is recording the analog input
voltages. The LED will continue blinking GREEN+RED until two sweeps (from closed throttle/released clutch to Wide
Open Throttle/depressed clutch) of at least 1.5 volts are taken. Once this parameter is met, the LED will change to one
of the following colors:
• In programming mode, a solid GREEN LED signifies that the programming of the analog voltage range was
successful.
• Blinking RED when an error occurs, which can be fixed by reprogramming the module. The following conditions
must be met for the programming to be successful:
• The range between the closed throttle/released clutch voltage and the wide open throttle (WOT)/depressed
clutch voltages must be at least 1.5 volts.
• The difference between the first WOT/depressed signal voltage and the second WOT/depressed signal voltage
must be less than or equal to 0.1 volts.
Installation:
• Disconnect the negative battery terminal.
• Connect black wire of RPM switch to a suitable vehicle ground. Failure to fully secure the ground wire to a vehicle
ground source could result in malfunction of the module.
• Connect the red wire to a switched and fused +12 volt DC source. The +12vdc source that the red wire is connected to
should be powered anytime the ECM is powered. A 5-10 amp fuse should be sufficient, but remember that each output
is rated for up to only 0.75 amps, so a relay should be used if any of the RPM-003 outputs will be controlling a device
that pulls more than 0.75 amps.
• Connect the white wire to the RPM signal source. This can be the tachometer output lead of the vehicle, the switched
side of the ignition coil (negative side) or the 5 volt RPM reference signal.
• See Table A on page 14 for information on some of the common vehicle ECM/PCM tachometer signal wiring
information.
• If you will be using the Normally Off (open) ground activation output, such as to control a shift light, connect the
yellow wire to the ground side of the device you plan to activate.
• If you will be using the Normally On (closed) ground activation output, connect the gray wire to the ground side of the
device you plan to activate.
• If you will be using the Normally OFF (open) +12 Vdc activation output, connect the orange wire to the +12 Vdc side of
the device you plan to activate.
• If you will be using the analog input, connect the purple wire to a rising or falling 0-5 volt analog signal wire running
from the TPS, CPP sensor, APP sensor, MAP sensor, or other analog 0-5 volt signal vehicle sensor.
• If the device you will be controlling draws more than 0.75 amps, make sure to control the device through a relay.
• Secure the RPM-003 using the supplied hook and loop tape or using the supplied self-tapping screws.
• Set the Input Signal Pulse Per Revolution switch to the correct setting for your vehicle application. See Table B on page
15 for the settings.
• Set the DIP switch settings inside the back cover of the module. Refer to page 3 for an explanation of DIP switch
settings (hysteresis, tach pull-up, and analog input) and to Figure 1 on page 3 for a table of DIP switch settings.
• Reconnect the negative battery terminal.