12 servicing – Glow-worm EnergySaverCombi 100 User Manual
Page 25
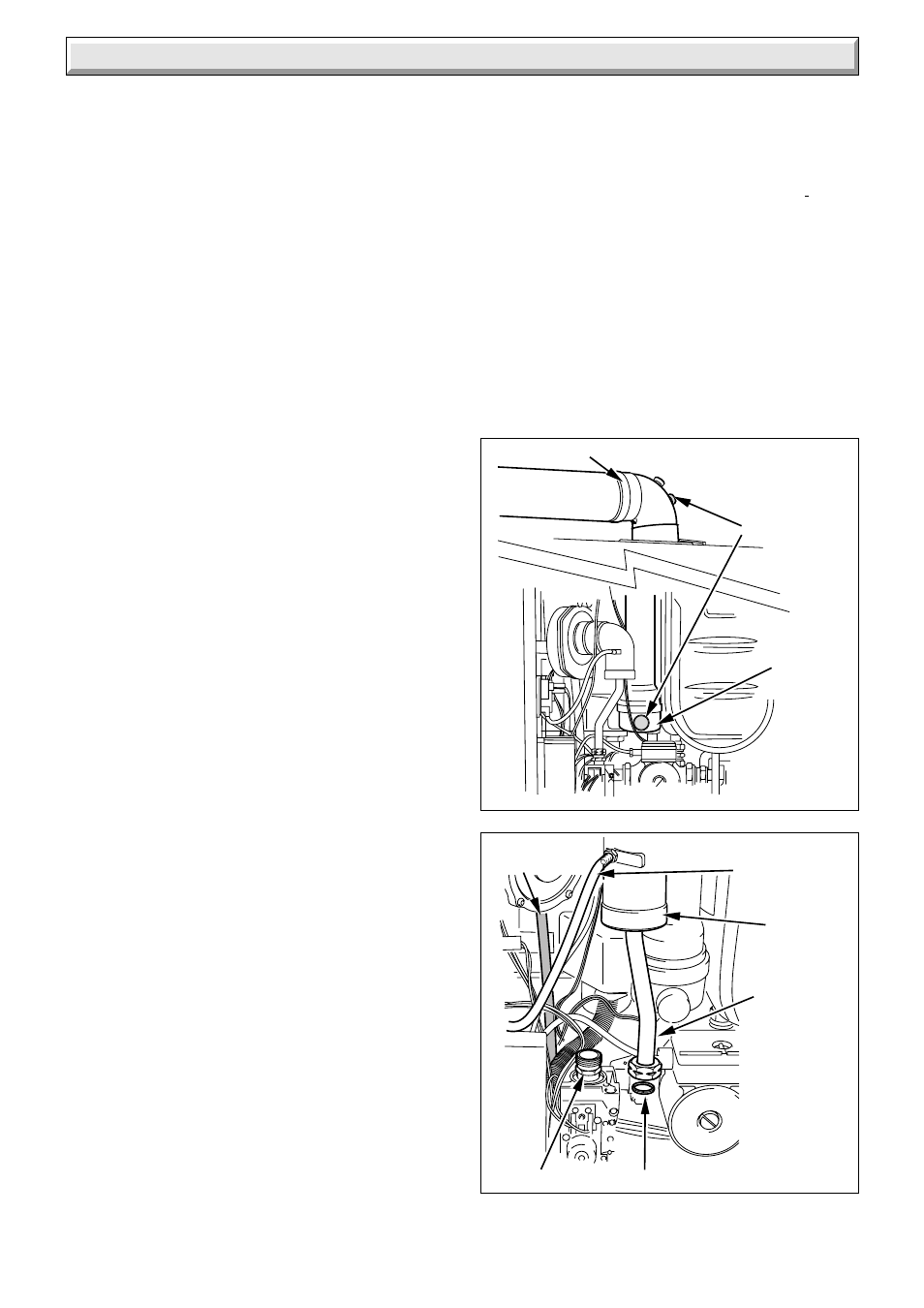
25
221854B
12.1 General
To ensure the continued efficient and safe operation of the
boiler it is recommended that it is checked and serviced at
regular intervals. The frequency of servicing will depend upon
the particular installation and usage, but in general, once a year
should be sufficient.
It is the law that any servicing is carried out by a competent
person.
Measurement of the products of combustion can be achieved
by connection of a probe to the flue elbow or alternatively to the
sample point at the base of the flue outlet pipe inside the boiler,
see diagram 12.1.
Before commencing with a service or replacement of parts the
boiler should be isolated from the electrical supply and the gas
supply should be turned off at the gas isolation valve, see
diagram 8.1.
All routine servicing requirements can be achieved by the
removal of the front panel only. To remove, simply lower the
control door and remove the two screws at the bottom of the
front panel.
Unless stated otherwise any part removed during servicing
should be replaced in the reverse order to removal.
Servicing should always include the removal of any debris from
the condensate pipe and siphon.
After completing any servicing of gas carrying components,
ALWAYS test for gas soundness and carry out a functional test
of the controls.
12.2 Combustion Chamber and Heat
Exchanger
The Combustion Chamber and Heat Exchanger do not require
cleaning during routine servicing. See section 12.11 for major
servicing.
12.3 Burner and Fan
Undo the union nut on the injector tube. Lift the tube clear of the
injector on the gas valve and then twist the tube and pull
downwards to disengage from the fan inlet flange, see diagram
12.2.
Remove Air pressure switch tube, see diagram 12.2.
Remove spark plug lead, see diagram 12.3.
While supporting the fan, remove the wing nut and screw and
pull out the fan securing plate, see diagrams 12.3 & 12.4.
Gently lower the fan and burner assembly out of the combustion
chamber.
Disconnect the electrical lead from the fan.
Inspect the burner for any signs of damage.
The burner can be cleaned if necessary by washing in warm
soapy water and rinsing with clean water. DO NOT use wire or
sharp instruments to clean the holes of the burner.
Clean the inlet holes of the fan inlet flange with a soft brush or
vacuum cleaner, see diagrams 12.2 and 12.5.
Examine the fan inlet and outlet seals and replace if necessary.
When refitting the fan securing plate, ensure that the dimples
are uppermost and that the fork on the plate engages onto the
ledge on the Heat Exchanger, see diagram 12.6.
When refitting the injector tube make sure the ‘O’ ring seal is
fitted.
12.4 Spark Electrode
Remove the spark plug lead and two securing screws. Withdraw
the spark electrode and viewing window from the combustion
chamber, see diagram12.3.
Inspect the tips for damage.
Clean away any debris and check the spark gap is 3.5
+
0.5mm,
see diagram 12.7.
Check the electrode gasket for signs of leakage and replace if
necessary.
Diagram 12.2
6528
Diagram 12.1
6527
FLUE ELBOW
ALTERNATIVE
PROBE
POSITIONS
FLUE
OUTLET
PIPE
“O” RING SEAL
INJECTOR
TUBE
AIR
PRESSURE
SWITCH TUBE
INJECTOR
VENT
PIPE
12 Servicing
FAN INLET
FLANGE