Bimba PCS Rod Lock User Manual
Page 6
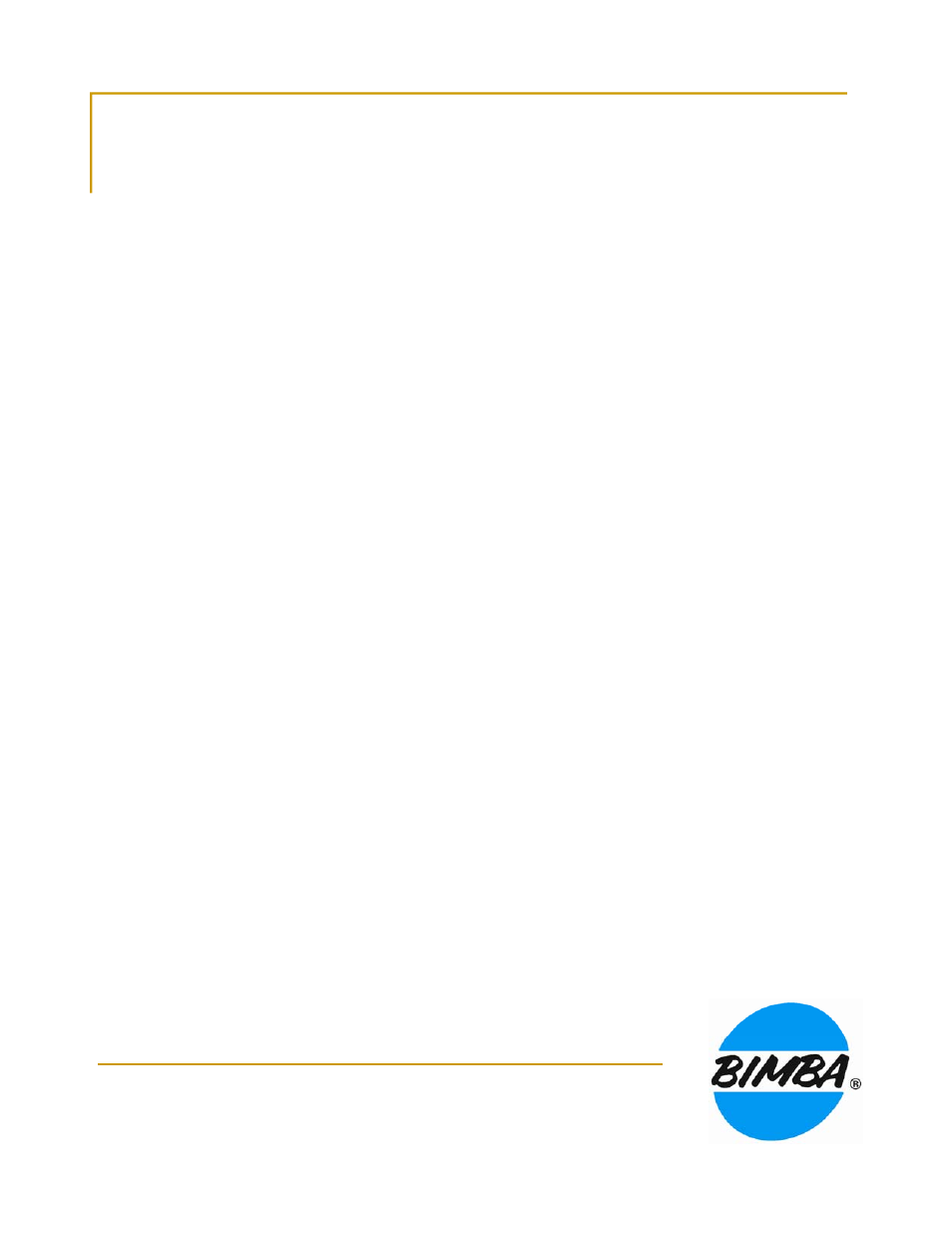
Employing a Rod Lock with a PCS System
in a Linear Motion Control System
The Rod Lock is intended to be used as a failsafe to lock the PFC piston rod. It is not
intended to be used as a dynamic brake. The PFC’s piston rod must be at rest before
engaging the Rod Lock.
The Rod Lock allows rod movement when air pressure is applied, and clamps the rod
when air pressure is removed. When air pressure is removed, an internal spring engages
the Rod Lock mecahnism. The spring is overcome when the Rod Lock is pressurized.
Use a three-way, normally closed, spring return valve with the Rod Lock. The valve must
be energized to release the rod. If power or air pressure is lost, the Rod Lock/3-way
valve subsystem will clamp the cylinder’s rod.
Limitation of Using a Rod Lock with a PCS Control System
Limitation of Using a Rod Lock with a PCS Control System
To accurately move the piston rod and hold it in position, the PCS controls the pressure
on both sides of piston. When a Rod Lock is added, a leak in the system could engage
the Rod Lock, clamping the rod. The PCS control may attempt to overcome the Rod Lock
in order to move the rod into position, potentially applying a large pressure to one side of
the piston which could wear out the Rod Lock and eventually cause failure or cause
violent motion or loss of control
violent motion or loss of control.
Pneumatic Circuit for Using the Rod Lock with a PCS
Refer to the figure on the next page. The valve labeled “Rod Clamp Valve” in the left
center of the figure is a three-way, normally open, spring return valve that operates the
Rod Lock. The PCS control’s valves are shown at the top center of the figure. The extend
and retract ports of the PCS are connected to additional valves which are only required
when the Rod Lock is employed. These must be 4-way valves with 5 ports. They allow
the PCS to operate normally when in motion. The valves are switched after the cylinder
comes to its commanded position. This places full line pressure at both the extend and
retract ports. As a result, the worst-case loading condition is reduced to the payload plus
the area of the cylinder’s rod times the line pressure. Spring return valves should be
added between the cylinder and the PCS. When power is lost, both the extend and
retract ports would be supplied with full line pressure Port 2 (shown in the figure) must
retract ports would be supplied with full line pressure. Port 2 (shown in the figure) must
be plugged on both these valves to prevent the normal valve blow by from reducing the
effectiveness of this circuit. The 3-way valve recommended for the Rod Lock will clamp
the cylinder’s rod when power or compressed air is lost.