Viconics VWZS Application Guide User Manual
Page 24
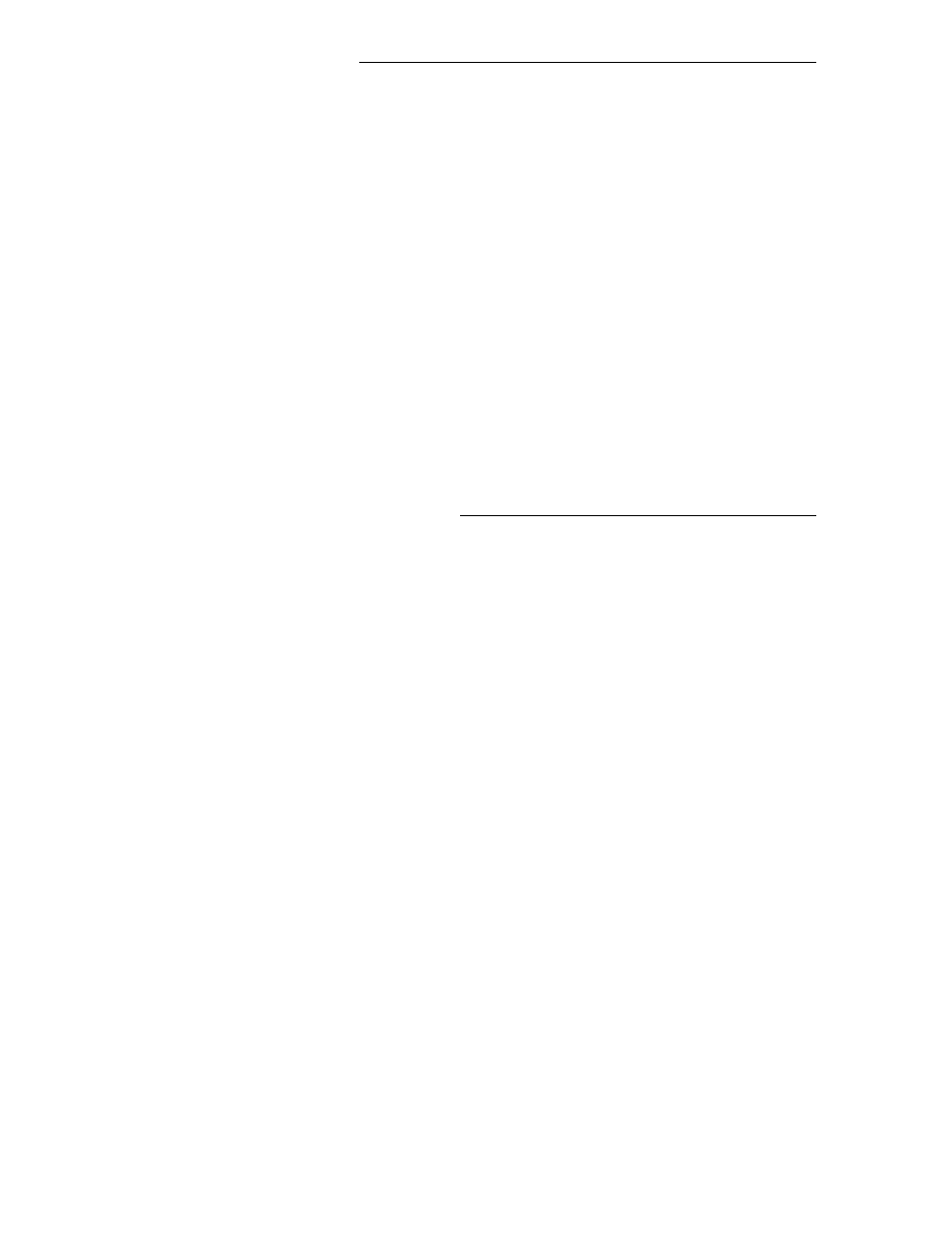
24
3F) Critical Mid-Season Changeover
Heating and cooling RTU equipment cycling during mid-seasons is inevitable with a zoning VAV system if
any degree of comfort is to be maintained.
A properly setup system will be able to deliver comfort to conflicting zone demands during the mid-season
period by alternating heating and cooling at the RTU.
Normally, a lot of the unwanted heating and cooling switchovers can be eliminated by authorizing terminal
reheat or by limiting the RTU heating or cooling capacity throughput based on the outdoor temperature
( H
Lock and C Lock ). However, limiting the RTU heating or cooling throughput based on outdoor
temperature will have an impact on control performance of certain zones when the required heating or
cooling capacity is not available due to the lockout conditions.
Typically, the number of RTU heating or cooling switchovers cycles during conflicting demand situations
will be around the same as the RTU CPH settings
(Default of 4 cycles per hour for both heating and
cooling). This will translate into two cooling and two heating cycle periods per hour.
Also, the recorded RTU supply delta temperature and demand variances will always be higher when using
a highest demand control type operation versus an average demand method. Energy consumption is also
expected to be higher with a highest demand control type operation versus an average demand method of
calculating the system requirements.
3G) By-Pass Damper / VFD Control and Operation
The RTU controller has a built in static pressure control loop with an analog 0 to 10 VDC output that can be
configured to control a by-pass damper or a variable frequency drive (VFD). In order to operate, the static
pressure control loop needs to have a static pressure sensor connected to the static pressure input on the
RTU controller (terminal SP).
The type of pressure transducer used needs to be of voltage type (0 to 5 VDC) and have a 24 VAC half-
bridge power supply.
The range of the pressure transducer needs to be one of the following and needs to be properly configured
using the static pressure configuration parameter (SP range).
Static pressure transducer range.
Voltage input range is 0 to 5 VDC.
-
0 = 0 to 1.5 in WC
-
1 = 0 to 2 in WC
-
2 = 0 to 3 in WC
-
3 = 0 to 4 in WC
-
4 = 0 to 5 in WC
Typically, the static pressure sensor probe is installed 2/3 of the way down the main ventilation duct.
The static pressure set point is set by the configuration parameter (Pressure). The default value is 0.8” WC.
The range and adjustability of the set point is: 0 to 2 in WC (0 Pa to 500 Pa) (increments: 0.1” WC or 25
Pa).
Please note that the static pressure scale will automatically change from inches of WC to PA (Pascals)
when the local units configuration parameter is changed.
-
0 = SI for Celsius / Pa pressure scale
-
1 = Imp for Fahrenheit / in. WC pressure scale
Operation of the static pressure control loop is dependent on the fan running or not, and the setting of the
pressure control type parameter SP Cntrl. For proper operation of the control loop, the static pressure
control actuator or VFD need to be properly installed.