Housing maintenance, Structural maintenance, Duct connections – Twin City Heavy Duty Composite Fiber Fans - IM-410 User Manual
Page 6: Optional accessories, Fan operation - safety
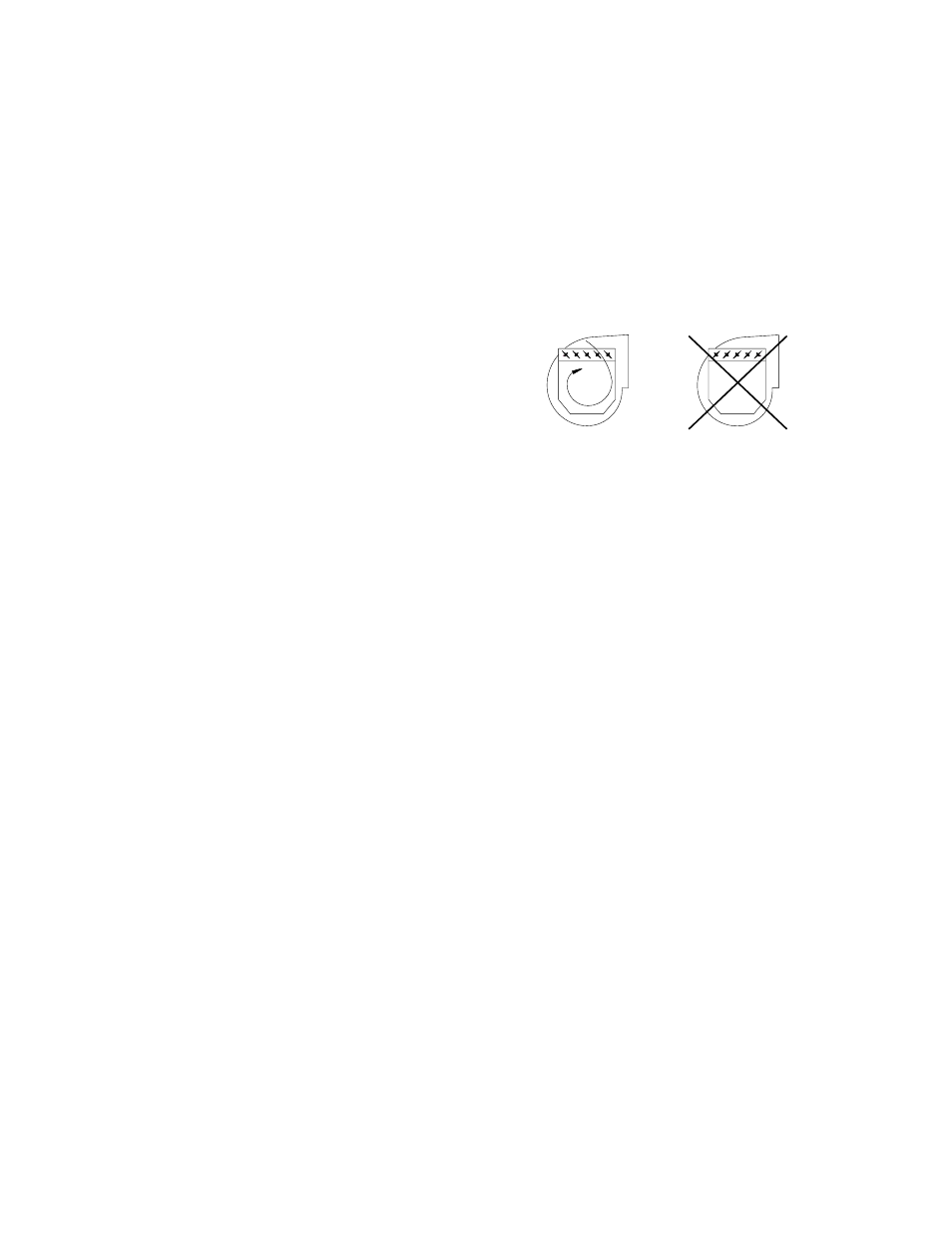
6
Twin City IM-410
Check the condition of the shaft to verify it has not
suffered any corrosive attack. Replace the sub-assembly
if needed.
HOUSING MAINTENANCE
The fan housing is assembled from two FRP halves that
are bolted together with stainless steel bolts and the inte-
rior joint is secondary bonded to prevent leakage. Check
the interior surfaces for any evidence of FRP damage and
repair, if possible, or replace if necessary. An optional
Inspection Door and Drain is available.
The inspection door is bolted to the housing with stainless
steel bolts and sealed with a corrosion resistant gasket.
The FRP drain is secondarily bonded to the low point
in the housing to minimize accumulations of liquid. Check
to insure the drain is not clogged and any fluid is dis-
charged appropriately.
STRUCTURAL MAINTENANCE
All structural components or devices used to support or
attach the fan to a structure should be checked at regular
intervals. Vibration isolators, bolts, foundation, etc. are all
subject to failure from corrosion, erosion, and other causes.
Improper mounting can lead to poor operation characteris-
tics or fan fatigue and failure. Check metallic components
for corrosion, cracks, or other signs of stress. Concrete
should be checked to insure the structural integrity of the
foundation.
DUCT CONNECTIONS
The fan support structure is normally not designed to
carry static loads imposed by the weight of ducts, silencers,
stacks, etc. or dynamic loads from wind or seismic events.
Supporting these loads on the fan inlet and discharge can
cause housing distortion and may cause performance prob-
lems due to the relation of fan housing to wheel. Excessive
loads on the fan housing may damage the FRP housing
and render it unfit for service.
Since FRP is used primarily for its corrosion resistance,
it is recommended that stainless steel fasteners be used.
Use a large washer under the head of the bolt and nut to
increase the load bearing area in contact with the FRP. Do
not tighten these fasteners to the point of crushing the FRP
laminate.
Use of flexible connections is recommended for all
installations and especially when the fan is mounted on
vibration isolators.
OPTIONAL ACCESSORIES
1. Shaft Seals – The standard shaft seal is a Teflon
membrane style shaft closure seal that minimizes
leakage around a FRP sleeve that is encapsulated
over a carbon steel shaft. Optional shaft seal is
either a Viton or Teflon lip seal that is installed in
a cast FRP seal housing. The shaft is encased with
a stainless steel shaft sleeve over a steel shaft. Care
must be taken to insure the integrity of the joint
between the shaft sleeve and the wheel backplate.
Other configurations of shaft seals are available for
special applications.
2. Bolt-On Variable Inlet Vanes – Variable inlet vanes
made of FRP are provided as assemblies externally
to the fan in flanged cylinders that are bolted to the
fan inlet. The vanes are used to control volume and
save power in installations where different volumetric
operating conditions are used. Variable inlet vanes
may be provided for operation with powered opera-
tors or for manual operation. Powered operator
instructions and operating manuals will be provided
when included.
3. Inlet Box and Inlet Box Dampers – FRP inlet boxes
may be provided to allow transition from a rectan-
gular duct to the fan inlet. FRP inlet box dampers
may also be provided for volumetric regulation
similar to inlet vanes. FRP inlet dampers are usu-
ally provided as a complete assembly and are
installed with the damper axis parallel to the fan
shaft. They must be installed to pre-spin the air in
the direction of fan rotation. See Figure 6 below.
Damage may occur if the fan is operated regularly
with dampers less than 30% open.
4. Outlet Dampers – FRP outlet dampers are usually
provided completely assembled like the inlet damp-
ers. The damper is bolted to the fan discharge
flange for volume control.
5. Oil Circulating System – Usually the following mod-
ifications will have to be made to the split pillow
block bearings if an oil circulating system is used.
a. Four drain holes will be drilled in the bearing,
two on each side of the bearing. Because of
this, the bearing may be drained from either
side. (Drain from both holes on one side of the
bearing.)
b. The bearing will be packed with grease to pre-
vent corrosion until installed and started up.
The drain holes will be plugged with plastic
coversto make sure they are open. NOTE: The
customer MUST REMOVE most of the grease
using solvent and remove the plastic covers
prior to starting the oil circulating system.
c. A wet sump will be added in case of circulat-
ing oil pump failure. Seals will be provided to
minimize oil leakage due to oil splashing.
d. The grease zerk on top of the bearing will be
removed for that hole to be used as the oil
inlet.
6. Anti-Rotation Clutch – Damage will occur if the fan
is operated in the wrong rotation. Run the motor
uncoupled from the fan to establish the proper rota-
tion.
FAN OPERATION - SAFETY
For general safety practices relating to air moving
equipment, see AMCA Publication 410.
Twin City Fan & Blower has many safety accessories
available. These safety devices include (but are not lim-
ited to) belt guards, shaft guards, inlet guards, and
discharge screens. The use, abuse, or non-use of
safety devices is the responsibility of the purchaser.
Facility-related safety conditions include fan accessi-
bility and location.
• How easily can non-service personnel access
the unit?
•
Is the fan in a hazardous duty environment?
•
Was the unit ordered for this duty?
Other concerns must also be addressed.
All fans should be powered through safety switches
which are easily accessible to service personnel and in
close proximity to the fan. Every safety switch should
RIGHT
WRONG
Figure 6. Orientation of Damper Blades