Maintenance of kit fan, Performance troubleshooting – Twin City Air Kit Fans - ES-56 User Manual
Page 2
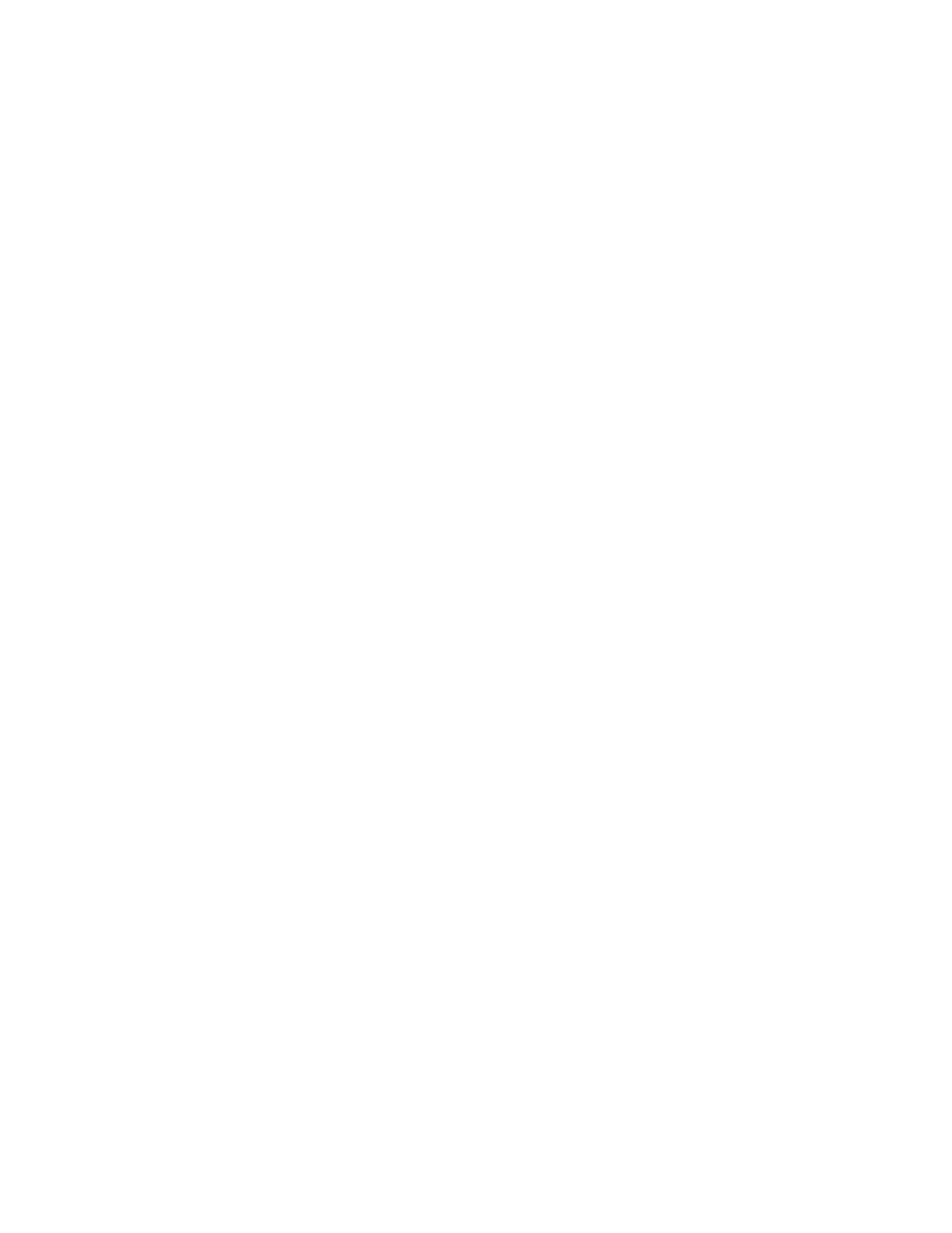
end of the shaft. The head of the inverted
socket head capscrew will fit in the short
keyway. Make sure that the shaft can expand
without the end of the keyway hitting the
screw head.
(2) With shaft at the proper centerline height and
bearing square with the shaft, bolt bearing
into position.
c. Tighten all setscrews remaining in bearings. (If
shaft expansion modification was used, do not
use any other setscrews on expansion side bear-
ing other than the inverted screw provided.)
5. Position wheel in housing so that it will be centered
when hot. Shaft expansion must be allowed for high
temperature applications. The wheel will move away
from the drive (or fixed) bearing by an amount equal
to the distance to the wheel from the drive bearing
times the temperature rise times the coefficient of
thermal expansion — about 0.0000067/°F/inch for
steel. Tighten Allen-head setscrews. (Allen-head
setscrews are normally provided.)
6. Accessories may now be permanently mounted and
bolted into position (recess cone, shaft seal, shaft
cooler and cooler guard). Rotate shaft manually to
insure adequate clearance.
7. Assemble drives as listed in ES-52.
8. Install cut-off in discharge of housing with bolts
through sides and base of cut-off.
9. Check and tighten all screws, nuts and bolts.
10. The installer may need to fine-tune balance the final
assembly. (All wheels are factory balanced. Low
speed FC units will generally not require a final
balance.)
Maintenance of Kit Fan
See Bulletin ES-52 for normal maintenance instructions
for bearings, drives, etc. High temperature applications
should avoid heat soaking of shaft. Stationary (nonrotat-
ing) shafting should never be exposed to elevated tem-
peratures or bending may occur. Shaft should always
be rotating in an elevated temperature environment.
On high-temperature applications, check all fasteners
(nuts, bolts, screws, and rivets) for tightness. Cyclic
heating and cooling can loosen fasteners from thermal
expansion and contraction. Check after the first few
cycles of thermal change or 48 hours, whichever comes
first. Then check on a monthly basis.
Performance Troubleshooting
See troubleshooting section of Bulletin ES-52 to iden-
tify causes of problems normally encountered. In addi-
tion to those mentioned, on kit type installations check
for:
1. Vibration — Bent shaft caused by exposure of shaft
to high temperatures while not rotating.
2. Fan will not start or motor trips out after start-up
— Motor was not sized for WR
2
required. Motor
horsepower too low for cold start.
are installed so that the bearings can be shimmed for
proper centerline height.
Provide for passage of shaft through the wall of the
oven. Relief must be provided for recess cone mounting
and shaft seal (see Figure 1). Installation of a recess
cone may also require the use of a cylindrical section
to restrain insulation and maintain proper depth of oven
wall.
Clean the wheel bore with solvent and check for
burrs, rust paint, or other obstruction. Use 80 grit emery
cloth by hand to remove foreign particles. Flush any grit
remaining and wipe clean. Place an even film of oil in
the wheel bore.
Extra care should be taken with shafting. Shafts for
air kits tend to be quite long and heavy and can be
easily damaged. Clean the shaft with solvent and check
for nicks, scratches, and burrs. Remove rough spots
with emery cloth and clean again. Cover the shaft with
a light film of oil.
Assembly
Fan housing and bearing supports are installed as previ-
ously described. Inlet funnels which may have been
supplied separately should be mounted to the housing
at this time.
1. Place wheel into housing through discharge of hous-
ing. Check wheel for proper wheel rotation before
proceeding (see Figure 1). Block wheel so that
wheel inlets are centered with housing inlets.
2. Insert the shaft through housing inlet and wheel
bore. Kits which have the shaft extension modifica-
tion will have keyways at both ends of the shaft.
Identify the drive end from fan drawings to insure
proper shaft orientation. Temporarily support the
shaft and wheel assembly on blocks across the full
length of wheel. Do not support on housing sides,
inlet funnels, wheel end rings, or accessories.
3. The optional accessories are installed in this order
onto the shaft: recess cone, shaft seal, shaft cooler,
and cooler guard. These parts are installed outside
the oven wall except the recess cone, which
becomes part of the wall. All fasteners should
remain loose until bearing mounting is complete.
4. Slip the bearings onto the shaft and pedestal and
secure, making sure the following instructions are
followed:
a. Mounting expansion bearings — no shaft expan-
sion modification.
(1) Place bearing onto the shaft with bearing col-
lar facing away from wheel.
(2) Adjust expansion capability of bearing so that
the bearing is toward the wheel in the bearing
housing. (When the shaft expands from heat,
the bearing will be pushed away from wheel
in the bearing housing.)
(3) With bearing properly aligned and shaft at the
required centerline height, bolt bearing to the
pedestal. Go to step 4c.
b. Mounting bearing with shaft expansion modifica-
tion:
(1) Slide bearing onto shaft with bearing collar
pointed away from the wheel and toward the
3MPP1/00
Twin ciTy fan & blower | www.Tcf.com
5959 Trenton Lane N | Minneapolis, MN 55442 | Phone: 763-551-7600 | Fax: 763-551-7601