Top Flite Elder 60 biplane User Manual
Page 12
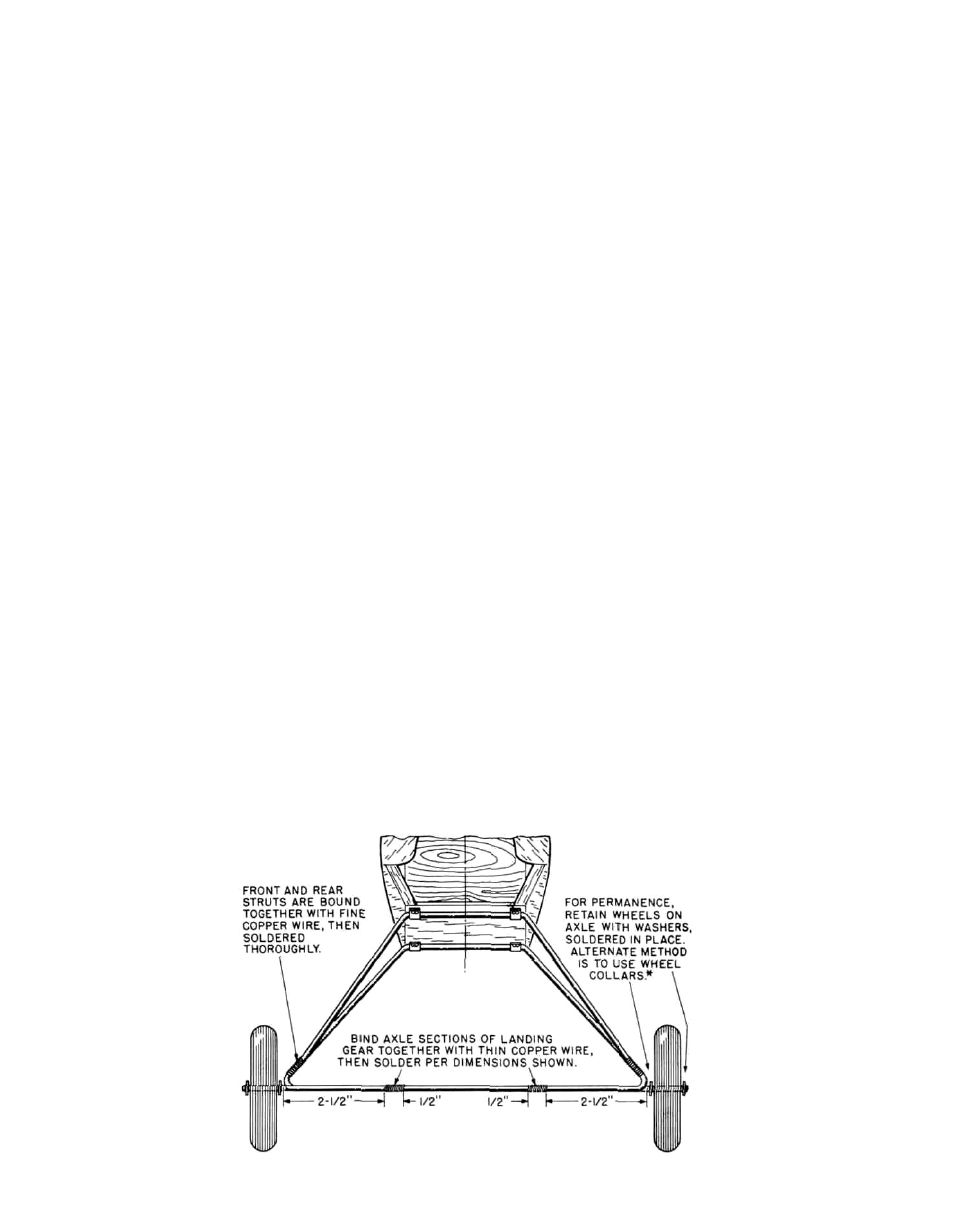
adhesive works very well here, eliminating the need
for pins. If you've taken your time and fitted these
pieces in place with a minimum of gaps, all that re-
mains is sanding to shape.
20. Use your sanding block and coarse paper to now
bevel the inside ends of the spruce fuselage
framework at the tailpost—see Top View of plans.
Once satisfied, careful ly epoxy these ends together,
providing equal bends to each side of the fuselage
when viewed from the top. Also view the structure
from the rear making sure everything is square.
When satisfied, clamp securely and allow to cure.
Accurately cut five (5) pairs of top and bottom 1/4" sq.
spruce cross braces which will correspond, in loca-
tion, to the exposed uprights. We suggest cutting
these pieces at the same time, taking care to ensure
that they are of equal length. With the tailpost joint
fully cured, glue cross braces in place, working from
the front to the back. Check each cross brace in-
stallation as you go, making sure the structure stays
square.
21. The complete fuselage, including the exposed
spruce framework should now be given a complete
sanding. Any gaps, nicks or dings should be filled
and sanded-off. Remove the two F-10 (ply) pushrod
guides from their die-cut sheets. Use your sanding
block to clean-up their edges and the slot. Once
satisfied, glue F-10's in place to the outside of the
vertical uprights, beneath the stabilizer location.
The last thing to do is to make the cut-outs for the
cockpit locations for your "pilots". At this point, you
can choose to make the model a one or two "holer."
With the exception of the cabane struts and some
other details which will follow, your fuselage is com-
plete.
WIRE PARTS ASSEMBLY
I. LANDING GEAR
The pre-bent front and rear 1/8" dia. M.W. landing gear
(L/G) forms must be joined together at the bottom,
towards the wheels. We recommend soft copper wire for
firmly and neatly wrapping the two pieces together prior
to soldering. We would highly recommend the use of
HARRIS'S STAY-CLEAN FLUX and their silver solder for
this operation. Although a soldering iron will work, with
patience, these joints can be quickly and permanently
made with the use of a small hobby-type gas torch.
1 . Locate the position of the rear "cross-axle" wire to
the bottom rear ply L/G plate on the fuselage bottom.
While holding the wire in place, slip the two formed
metal clips onto the wire. Use a pencil to mark the
hole locations of these clips onto the ply base, then
remove the wire and clips. Drill shallow, small-
diameter "guide holes" for the clip's #2 x 3/8"
screws. Now attach the landing gear wire to the
fuselage with the clips and screws— do not over-
tighten. Repeat this process with the forward lan-
ding gear wire.
2 . Pull the two wire parts togetheruntiltheytouch.The
two short bent 'arms' on the forward leg should line-
up with the legs of the rear L/G wire. If needed, use
pliers to adjust these arms until they fit neatly and
uniformly.
3 . Use soft copper wire to now neatly wrap the forward
short arms to the rear L/G wire as shown in the il-
lustration in the plans. Apply some STAY-CLEAN
flux to the joint and solder. Repeat the process on
the opposite side. Be neat and try to be sure that the
joint is sol id without a lot of excess solder. Once the
joint has been made, clean with water to remove all
flux and dry-off with a paper towel.
4 . As shown, the crossed-axle landing gear system
derives its ability to accept landing loads and shock
from the two independent axle legs. These need to
be joined at two points, each 2-1/2" in from the wheels.
This distance has shown very good shock-absorbing
abilityforEIderBiplanesweighing 7-1/2 to8-1/2 Ibs.Join
these axles by first measuring the 2-1/2" distance re-
quired, wrapping with soft wire (about 1/2") and
soldering. Again, clean the solder joints completely
with water and dry.
12