Sonics GXT User Manual
Page 29
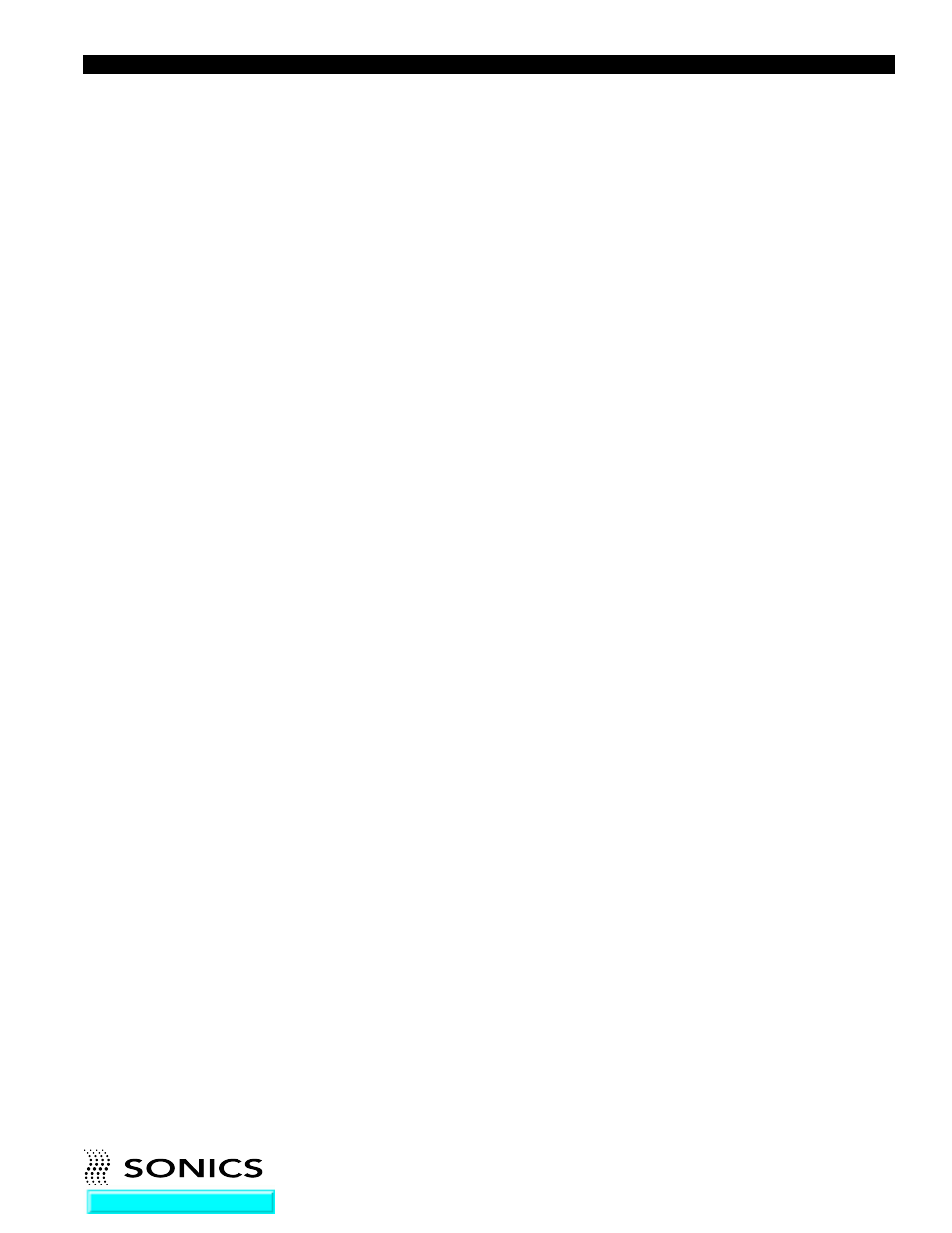
• • • • • • • • • • • • • • • • • • • • • • • • • • • • • • • • • • • • • • • • • • • • • • • • • • • • • • • • • • • • • • • • • • • • • • • • • • • • • • • • • • • • • • • • • • • • • • • • • • • • • • • • • • • •
I N S T R U C T I O N M A N U A L • M O D E L G X T P O W E R S U P P LY
28
signal to qualify these outputs, if ready is true, then the Good Part / Bad
Part outputs are valid.
4. DO4 – There is one extra digital output that is reserved for future
application.
5. DI1, DI2, DI3 and DI4 – Four digital input signals are used for setting an
external job selection when the keyboard is “Locked.” 15 sets of weld
control parameters may be stored in the controller’s battery RAM area.
(see page 21, Job Storage). They may be recalled into the working job
area by setting a binary address code with these digital inputs (see table
below). Valid jobs must exist and have been previously stored via the
keyboard entries. All valid jobs must have a non-zero weld time entry. If a
job does not contain a non-zero time entry, a weld cycle cannot be
initiated.
The keyboard must be locked (see page 23) and the system must be at a
Ready screen for the job address inputs to be active. The inputs are ignored
if these conditions are not set. The keyboard must be locked so that job or
data changes cannot be requested from two different sources – the keypad
and remote address lines – at the same time. Only one source of job change
is allowed: the keyboard (if not locked) or the digital inputs (when the
keyboard is locked).
The job address lines may be changed anytime but must be held stable for
a minimum of 50 ms prior to initiating a weld cycle with the impulse input
command contact. When a job change has been recognized, the system will
momentarily indicate Not Ready for a maximum of 30 ms while the job
settings are recalled from battery backed RAM and the system internals are
reset for a new cycle. The impulse command should be delayed until the
Ready signal returns from the job recall operation if external job setting is
used.
For the quickest possible cycle time, the next job address may be set after
the present weld cycle begins as indicated by the ready signal (false). This
does not affect the present weld cycle as it is already underway and the
settings cannot be changed during the present cycle. They are locked once
a cycle has started. If the job address has been changed during the present
weld to reflect the desired job for the next weld cycle, the recall operation will
happen at the end of the weld cycle before the final Ready indication.
Once Ready is true, the job has already been changed and the system is
Ready to initiate the next cycle. This method extends the weld cycle by 30
ms which are needed to recall the job settings for the next cycle. Depending
on weld times, up to 80 cycles per minute may be achieved including job
changes between each weld (print line must be OFF to achieve this cycle
rate).